Мощное оборудование для производства термоусадочной пленки ПВХ
Производство пленки в наше время может быть выгодным бизнесом. Особенно если говорить о такой области, как производство термоусадочной пленки. Последняя бывает нескольких видов: из ПВХ, ПП, ПОФ и т.п. Оборудование для производства пленки позволяет выпускать большие объемы. Поэтому завод по производству пленки при хороших продажах окупает затраченные на его строительство средства уже через несколько лет. Производство термоусадочной пленки пвх дает в результате качественный и недорогой продукт. Такая пленка способна сокращаться при повышении температуры, а также очень плотно обтягивать упакованные изделия.
В ближайшие три годы на российском рынке стоит ожидать массового запуска производств трех- и пятислойной термоусадочной пленки.
Свойства термоусадочных пленок
Физико-механические и экcплуатационные свойства пленок обусловлены химической природой применяемого полимера и степенью его ориентации.
Важными характеристиками термоусадочных пленок являются степень усадки (коэффициент усадки) и напряжение усадки.
Степень усадки характеризуют отношением линейных размеров образца до, и после усадки.
Напряжение усадки — это напряжение, возникающее в ориентированном материале при нагревании до определенной температуры.
Напряжение усадки зависит от температуры и продолжительности нагрева пленки. Чем ниже температура усадки, тем больше времени требуется для усадки пленки. Если производить усадку при высоких температурах, то время усадки может быть незначительным.
Прочность пленок после усадки несколько уменьшается, но остается достаточной, чтобы обеспечить целостность упаковки.
Для упаковывания единичных изделий небольшой массы, например, хлебобулочных изделий, тушек птиц, аэрозольных баллонов, сувенирные наборов применяются пленки толщиной 20 — 50 мкм, для групповой упаковки выбирается пленка толщиной 50 — 100 мкм, для пакетирования на поддонах (штабельной упаковки) — пленка толщиной 100 — 250 мкм.
Основные свойства термоусадочных пленок
Полимер |
|
Степень усадки, % |
Напряжение усадки, МПа |
Температура усадки при упаковывании, °С |
Температура сварки, °С |
ПЭНП |
0,92 |
15-50 |
0,3-3,5 |
120-150 |
150-200 |
ПЭНП радиационно-модифицированный |
0,92 |
70-80 |
1,0 -3,5 |
110-210 |
170-230 |
ПП |
0,9 |
70-80 |
2,0-4,0 |
150-230 |
175-200 |
ПВХ |
1,4 |
50-70 |
1,0-2,0 |
110-155 |
135-175 |
ВХВД |
1,65 |
30-60 |
1,0-1,5 |
95-140 |
200-315 |
ПС |
1,05 |
40-60 |
0,7-4,0 |
130-160 |
120-150 |
Эскаплен |
1,1 |
30-50 |
|
100-150 |
180-250 |
Для достижения высоких физико-механических и технологических характеристик термоусадочной пленки, как упаковочного материала к ней предъявляются следующие требования: рецептура, высокая однородность свойств по всему полю полотна, высокое качество намотки.
Варианты упаковывания в термоусадочную пленку
Возможные варианты упаковывания в термоусадочную пленку могут быть условно разделены на три основные группы:
Единичная упаковка. Ее называют штучной, или индивидуальной. Каждое отдельное изделие обертывается пленкой, которая после усадки плотно облегает изделие, повторяя его конфигурацию.
Групповая упаковка. Предварительно комплектуется набор из нескольких однотипных или разнотипных изделий, которые, как и при единичной упаковке, обертываются пленкой, после усадки которой получается плотный пакет.
Упаковывание может производиться только в пленку или с использованием предварительной укладки изделий на специальные подложки. Этот вид упаковки может применяться в качестве транспортной тары.
Штабельная упаковка. На жесткий поддон укладываются несколькими рядами изделия (мешки, коробки, книги, кирпичи, лотки с банками, бутылками и т.д.), которые сверху покрываются чехлом из термоусадочной пленки и подаются в туннельную печь.
Штабельная упаковка представляет собой современный и перспективный вид транспортной упаковки товаров.
Оболочки из термоусадочной пленки по конструктивному исполнению подразделяются на обандероливающие, полностью обертывающие и зачехляющего типа.
Обандероливающие пакетирующие оболочки покрывают группу изделий (упаковочных единиц) или транспортный пакет (блок-пакет) по периметру полностью, а на торцевых сторонах имеют отверстия.
При полном обертывании пленочная оболочка полностью покрывает транспортный пакет или группу изделий (упаковочных единиц).
Для скрепления транспортных пакетов пакетирующими оболочками зачехляющего типа из рукавной термоусадочной пленки изготавливаются чехлы путем соединения сварным швом верхних краев отрезка рукава.
Применение термоусадочной пленки
По опыту зарубежных предприятий 95% термоусадочных пленок используется для упаковки непищевых продуктов и только 5% для пищевых (чаще всего для упаковки пиццы и овощей).
— упаковка хлебобулочных изделий — применяется для увеличения сроков реализации и, кроме того, в такой упаковке хлебобулочные изделия приобретают эстетичный товарный вид;
— упаковка мяса и птицы – для увеличения сроков хранения, придания эстетичного вида и удобства для розничной продажи;
— упаковка кондитерских изделий или полуфабрикатов с использованием лотков соответствующих размеров. Такая упаковка, благодаря жёсткому лотку, обеспечивает большую сохранность продукта по сравнению с обычной расфасовкой в пакеты и имеет более привлекательный для потребителя объём фасовки.
Также термоусадочная пленка используется и в сфере непищевых товаров.
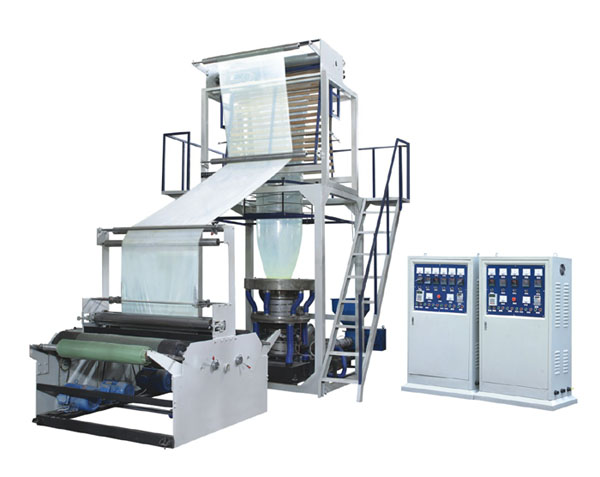
— упаковку бумажных изделий – бумаги для факсов, полиграфической продукции. В данном случае используется термоусадочные пленки с низкой степенью усадки;
— упаковку хозяйственных изделий;
— упаковку химических, пищевых, медицинских, парфюмерных товаров;
— упаковку строительных материалов: плинтусов, штапика, наличников, карнизов, жалюзи, обоев и многих других длинномеров. В данном случае используется термоусадочные пленки с различной усадкой в продольном и поперечном направлениях;
— упаковку видеокассет, CD-, DVD-дисков, сувениров и др.
Также термоусадочные пленки применяют для упаковывания продукции на кирпичных и стекольных заводах.
История термоусадочной пленки
История термоусадочных упаковочных материалов началась в 1938 году с изобретения французского ученого Анри де Пуа. Производство термоусадочных пакетов началось в США в 1939 году, а патент был оплачен и защищен в 1945 году.
Последующее развитие термоусадочной пленки из пластика в начале 1940-х гг. связано с выходом американских производителей на рынок Европы. Это событие стало поворотным моментом в упаковке пищевых продуктов и технике продаж.
Термоусадочные пакеты для упаковки птицы перевернул всю промышленность США по производству индейки, а затем практически захлестнули весь мир и в настоящее время используется почти во всех странах-производителях и экспортерах пищевых и непищевых продуктов в мире для широчайшего ассортимента продуктов.
Первые термоусадочные пленки изготавливались из ПВХ, как наиболее технологически простого и недорого материала. Однако, традиционные ПВХ-пленки, имеющие в своем составе активный элемент хлор, вызвали массу претензий со стороны «зеленых».
Первоначально в качестве заменителя ПВХ-пленок предлагались полипропиленовые пленки, изготовленные таким образом, что у них возникал эффект термоусаживания. Однако в силу ряда причин — ограниченной величины и более высокой, чем у ПВХ, температуры термоусадки, худшей свариваемости, потере свойств при низких температурах и т. д. — полипропиленовые пленки не смогли заменить ПВХ.
Следующим шагом стало создание соэкструдированных пленок, имеющих в составе сополимеры полипропилена и линейного полиэтилена. Они приблизились по потребительским свойствам к ПВХ-пленкам и в некоторых случаях даже превзошли их.
Наиболее современными и качественными являются термоусадочные пленки на основе полиолефинов, в частности линейного полиэтилена. Полиолефиновые пленки на основе линейного полиэтилена способны заменить ПВХ практически во всех сферах применения, а также обеспечивают ряд дополнительных полезных свойств.
Термоусадочные полиолефиновые пленки, широко применяющиеся в ЕС (сегодня Европа уже практически перешла с термоусадочных ПВХ-пленок на полиолефиновые) и США, завоевывают и российский рынок.
Переходу с термоусадочных ПВХ-пленок на ПО-пленки способствует рост интереса к полиолефиновым пленкам со стороны отечественных производителей, в основном, кондитеров, производителей хлебобулочных изделий. По некоторым данным, в России за последний год спрос на них увеличился на 100%.
Кроме того, запрещение использования ПВХ-пленок во многих странах Европы, приводит отечественных производителей, поставляющих свой товар на внешний рынок, к необходимости использования альтернатив термоусадочной ПВХ-пленки.
В отношении состояния отечественного производства термоусадочных полиолефиновых пленок следует отметить, что пока оно практически все основывается на методе экструзии, что отчасти связано, как с относительно дорогостоящей организацией производства многослойных пленок, так и с отсутствием российского производства линейного полиэтилена (вводимого в наружные слои многослойных термоусадочных пленок).
Многослойные пленки – лучше и дешевле
Многослойность в случае пленок срабатывает, как эффект «веника». Можно существенно снизить толщину при сохранении всех потребительских свойств. Это позволяет существенно экономить на упаковке.
Многослойная термоусадочная пленка включает первый слой сополимера с кислотой, сополимера этилена с α-олефином или их смесь, второй слой, содержащий сополимер этилена с 9-20 мас.% винилацетата. Пленка может иметь третий слой из барьерного полимера, четвертый слой — сополимера этилена с 9-20 мас.% винилацетата и пятый слой.
Формирование каждого слоя многослойной термоусадочной пленки происходит отдельно. Поэтому возможные дефекты каждого слоя не совпадают, и пленка оказывается на 15-20% прочнее, чем аналогичная по толщине однослойная. Таким образом, становится реальным уменьшение толщины (а значит и себестоимости) многослойной «термоусадки» без ухудшения ее эксплутационных характеристик. Кроме того, уменьшение толщины пленки дает возможность снизить температуру в термотуннеле, что позволяет потребителю пленки экономить электроэнергию.
Обладает отличной прозрачностью и глянцем в сочетании с высокой прочностью сварного шва и плотностью.
В дальнейшем на российском рынке будет происходить замещение однослойных пленок на многослойные. Устойчивость тенденции перехода российского производства на многослойные термоусадочные пленки обеспечивается экономичностью и оптимизацией производства на основе соэкструзии. Так, увеличение прочности многослойных пленок приводит к возможности уменьшения ее толщины, а соответственно и себестоимости производства.
В ближайшие годы однослойная пленка будет вытеснена
Бурное развитие производств многослойной термоусадочной пленки в ближайшие годы обусловлено следующими факторами:
1. Огромный потенциал для замещения однослойной пленки
Согласно результатам проведенного исследования на территории РФ по итогам 2005 года действует около 130 предприятий, занимающихся производством термоусадочной пленки. Более половины объема производства 2005 года (около 65,7%) многослойных термоусадочных пленок составляют трехслойные пленки.
При этом объем производства трехслойных термоусадочных пленок в натуральном выражении в 2005 году составил около 27,2 тыс. тонн, что на 23,8% больше объема производства трехслойных термоусадочных пленок в 2004 году.
2. Масштаб российского рынка термоусадочной пленки в целом
Несмотря на то, что уровень потребления упаковочных материалов на российском рынке, заметно ниже показателей развитых стран, в силу размеров территории и численности населения отечественный рынок обладает значительным объемом. В 2005 году объем производства термоусадочной пленки составил 205 тыс.тонн. (Этот объем способны покрыть более 40 крупных по западным меркам производств)
Относительный низкий уровень потребления продукта говорит о потенциале рынка.
3. Высокие темпы развития российского рынка термоусадочной пленки
В 2006 году темпы роста объемов потребления термоусадочной пленки составили 20%. Темпы роста объемов производства многослойных пленок (21%) опережают темпы прироста объемов однослойных пленок (15,5%). При этом наиболее высокие темпы имеют производства трехслойных (27,3%) и пятислойных (28,4%) термоусадочных пленок.
4. Ужесточение конкуренции на рынке однослойной пленки
Низкие барьеры входа обуславливают существование множества местных локальных производств. В настоящее время на российском рынке термоусадочную пленку изготавливают около 140 производств. Подобный характер размещения производств обуславливает низкий уровень доходности и прибыльности.
5. Тенденция укрупнения производств
Укрупнение производств – закономерный этап становления любого рынка. Если в Европе среднее пленочное производство характеризуется мощностью около 5 тыс.тонн в год, то в России этот показатель составляет 300-400 тонн. По мере становления рынка идет процесс укрупнения одних производителей и отмирания других. В результате на рынке останется несколько десятков крупных производителей. Они смогут предлагать более качественный продукт по более низкой цене, большой ассортимент и набор сервисных услуг. Крупные производители способны позволить себе применять дорогие добавки.
6. Развитие спроса на печать на термоусадочной пленки
Одной из этих сервисных услуг является печать на термоусадочной пленке. Развитие данного направления связано со стремительным ростом спроса на печать на групповой упаковке, а также с модой на объединяющую два предмета упаковку.
7. Открытие внутренних производств линейного полиэтилена
Рецептура внутреннего слоя требует использования ЛПЭВД. Запуск отечественных производств, безусловно, облегчит доступ к сырьевой базе. А во-вторых, снизит себестоимость готовой пленки. Тем самым, делая ее более конкурентной по сравнению с однослойной пленкой.
Таким образом, ожидается бум открытия производств многослойных термоусадочных пленок. Рынок характеризуется относительно неравномерной концентрацией производителей, что влияет на степень насыщения и развития региональных рынков. Учитывая также крайне ограниченное предложение многослойной термоусадочной пленки, в настоящее время для потенциальных инвесторов главным является изучение спроса и конкуренции на региональных рынках.
Объявления о покупке и продаже оборудования можно посмотреть на
Обсудить достоинства марок полимеров и их свойства можно на
Зарегистрировать свою компанию в Каталоге предприятий
полиолефиновая пленка — Справочник химика 21
Пленки из ПЭВД и других полиолефинов применяются в сельском хозяйстве. Высокий экономический эффект достигается от применения полиэтиленовой пленки в овощеводстве при сооружении теплиц, парников (стоимость пленочных теплиц и парников за счет упрощения конструкций в 2—3 раза ниже, чем стеклянных). Вследствие прозрачности полиолефиновые пленки п )опускают ультрафиолетовые лучи, что обусловливает сокращение сроков вызревания овощей в теплицах. Полиэтиленовая пленка применяется для укрытия буртов овощей и зерна при временном хранении их в полевых условиях. Из пленки изготавливаются мешки для минеральных удобрений. Пленка применяется и при силосовании. [c.36]Технология производства полиолефиновых пленок [c.

В настоящей главе представлен обзор полиолефиновых пленок. Прежде всего, рассматриваются различные типы полиолефинов и их пригодность для изготовления пленок (табл. 1.1). Строение, а также реологические и иные свойства полимеров обсуждаются применительно к тем процессам изготовления пленки, которые в наибольшей степени подходят именно для данных материалов. Также мы коснемся постэкструзионной обработки пленок, в том числе ориентации, химической модификации поверхности и введения химикатов-добавок. Описываются методы определения механических свойств пленок, их строения и присутствия добавок, а также некоторых более специфических свойств. Наконец, рассматриваются некоторые конкретные применения, требующие получения пленок особого строения или модифицирования. [c.15]
Полиолефиновые пленки (полиэтилен, полистирол, сополимеры и т. д.) [c.120]
Морфология полиолефиновых пленок [c.19]
Поверхностная энергия полиолефиновых пленок очень низка — трудно найти другие вещества, которые обладают адгезией к полиолефинам. Приемлемую адгезию можно получить в расплавах, но только если полиолефины имеют близкое строение. Например, хорошую взаимную адгезию имеют полиэтилены. Разветвленные полиэтилены с низкой температурой плавления используются наиболее широко, потому что их можно быстрее расплавить и они имеют подходящие реологические свойства для течения на подложку. [c.30]
Существует ряд стандартных методов испытаний для определения адекватности требований к рабочим характеристикам, предъявляемых к полиолефиновым пленкам. Их спецификации содержатся в соответствующих стандартах Л 5ГМ, DIN [c.35]
Ползучесть — это деформация образца под действием постоянного напряжения. Полиолефиновые пленки, подвергающиеся давлению в течение длительного периода, постепенно вытягиваются. Полз) есть является свойством, дополняющим свойство релаксации напряжения, и те же самые молекулярные характеристики усиливают сопротивление ползучести. Механизм ползучести схематически представлен на рис. 1.13 под действием постоянной нагрузки молекулы постепенно скользят одна относительно другой, в результате чего возникает удлинение. [c.37]
Скользящие детали клавиатуры музыкальных инструментов могут обрабатываться коллоидным кремнеземом для того, чтобы повысить илошадь соприкосновения и уменьшить проскальзывание пальцев [572]. Качество поверхности чертежной пленки из полиэтилентерефталата улучшается в отношении способности воспринимать карандаш и чернила при применении коллоидного кремнезема [573]. Точно так же полиолефи-новая пленка или бумага, покрытая полиолефиновой пленкой, хорошо воспринимают чернила в результате применения коллоидного кремнезема наряду с добавлением растворимого в кислоте пленкообразующего вещества [574]. [c.590]
Гомогенные мембраны с высокими характеристиками были также получены путем радикальной привитой сополимеризации стирола к полиолефиновым пленкам [342—344].

Отделочные и конструкционно-отделочные материалы. Для отделочных работ широко используют рулонные материалы — нолнвппилхлоридиые и полиэтиленовые пленки (см. Поливинилхлоридные плеики, Полиолефиновые пленки), а также влагостойкие бумажные [c.480]
Характеристики конденсатора существенно улучшаются при использовании комбинированного диэлектрика, состоящего из нолипропиленовой пленки (см. Полиолефиновые пленки) и пропитанной жидким дифе-нилхлоридом конденсаторной бумаги, к-рая выполняет гл. обр. функции фитиля, обеспечивающего хорошую пропитку конденсаторов. Применение такого диэлектрика позволяет примерно в 1,5 раза повысить уд. мощность конденсаторов при одновременном снижении их перегревов. Благодаря этому оказалось возможным изготовление монщых конденсаторов, эксплуатируемых при частоте 500 — 20 ООО гц без водяного охлаждения. [c.489]
Способы производства и обработки полиолефиновых пленок. И. II. иолучают экструзией. 1) тонкостенной трубы с последующим ее раздувом при этом образуется пленка в виде рукава (рукавный метод) 2) пленочного полотна с последующим его охлаждением на металлнч. барабане или, реже, в водяной ванне (илоскощелевой метод). Для производства П. п. применяют экструдеры с длиной пшека 20—30 d (d — диаметр шнека) и степенью сжатия материала 1 (2,5—4,0). [c.7]
Переработка и применение. Примерпо половину всего производимого П. перерабатывают литьем под давлением (индекс расплава П. 2—4) при 200—220°С и давлении в форме 35—42 Мн/м (350—420 кгс/см ). Этим методом из П. изготавливают детали машин, различную арматуру, бытовые изделия, коптейперы для хранения и перевозки сыпучих грузов и емкости для жидкостей. Ок. 30% П. (индекс расплава 4 — 20) перерабатывают в волокна (см. Полиолефиновые волокна). Методом экструзии из П. получают пленки (см. Полиолефиновые пленки), трубы и профилированные изделия. По трубам из полипропилена транспортируют агрессивные жидкости. [c.107]
Применение. П. и различные композиции на его оспове используют для изоляции проводов и кабелей, как диэлектрики в высокочастотных и телевизионных установках. Из П. изготавливают емкости д.ш хранения агрессивных сред, конструкционные детЕли, арматуру, вентиляционные установки, гальванич. вашш, скрубберы, струйные насосы, кессоны, отстойники, оросительные колонны, центробежные насссы для к-т, щелочей, солевых р-ров, детали автомашиг . П. широко применяют для производства пленок техник, и бытового назначения (см. Полиолефиновые пленки). [c.506]
Если полиолефиновая пленка существенно растянута, то ориентация ее кристаллической структуры становится значительной и полимер будет более твердым. Морфология может варьироваться от конфигурации складчатых цепей до комплексов с выпрямленными цепями. Связующие молекулы становятся полностью выпрямленными и дальнейшая деформация невозможна вплоть до разрыва пленки. Деформационное упрочнение определяет предел полезного растяжения пленки, поскольку ее упругость утрачивается. Кривая зависимости напряжения от деформации для ЛПЭНП, на которой видны области пластической деформации и деформационного упрочнения, показана на рис. 1.12. [c.36]
Поверхность полиолефиновой пленки может нести информацию об объеме. Рост кристаллов и другие неоднородности на поверхности, которые могут возникать при изготовлении и обработке, например, коронным разрядом, можно исследовать с помощью АСМ. Можно изучать изменение твердости или трения по поверхности, имеющие место в смесях. На рис. 1.16 приведено полученное с помощью АСМ изображение поверхности ЛПЭНП-пленки, полученной экструзией с раздувом рукава. [c.40]
Инфракрасная спектроскопия является удобным методом для идентификации полиолефиновых пленок. Основные классы полиолефинов легко распознаются. Детальная расшифровка инфракрасного спектра позволяет различить даже очень близкие структуры. Косвенным образом можно измерить степень разветв-ленности и кристалличности [27]. [c.42]
Классификация современной термоусадочной пленки
Существует несколько критериев, которые являются основой классификации современной термоусадочной пленки термоусадочной пленки. Прежде всего внимание обращают на тип исходного сырья, которым может быть:
1) полипропилен;
2) полиамид;
3) полистирол;
4) поливинилхлорид;
5) полиэтилен;
6) полимерные комбинации.
ПОФ
Первым делом необходимо рассказать о полиолефиновой термоусадочной пленке (ПОФ), пользующейся сегодня огромным спросом во многих европейских странах. Этот материал обладает довольно необычной молекулярной структурой, а именно перекрестно-пересеченной. Благодаря этому даже самая тонкая пленка способна выдерживать значительные нагрузки.
ПОФ обладает рядом преимуществ перед другим аналогичным материалом — термоусадочным поливинилхлоридом. Прежде всего это отсутствие мутности и заметный блеск, а также более высокая степень и пониженная температура усадки. Полиолефиновая пленка допускается к применению в гораздо более широком интервале температур.
Эта разновидность термоусадочной пленки характеризуется большей степенью эластичности по сравнению с ПВХ, а благодаря полному отсутствию в ней элементарных частиц хлора из нее не исходит абсолютно никаких запахов при усадке. ПОФ лучше подходит для упаковывания продуктов, нежели материалы на основе поливинилхлорида. Полиолефиновая пленка из-за высокой цены применяется довольно ограничено — отечественные предприятия зачастую применяют полиэтиленовую термоусадочную пленку (ПЭ), произведенную из полиэтилена с высокой или низкой степенью плотности.
ПЭ
Такая разновидность термоусадочной пленки характеризуется хорошей механической прочностью, способной сохраняться при температуре в пределах —50…+50 °C. Пленка из полиэтилена легко сваривается и является абсолютно инертной по отношению к многим веществам. Стоимость этого материала значительно ниже, чем стоимость всех остальных разновидностей термоусадочных пленок. Более качественными считаются пленки, для производства которых используется линейный полиэтилен.
Главное преимущество полиэтиленовой термоусадочной пленки перед ее полипропиленовым аналогом — это неспособность деформировать товар после его упаковывания. Именно благодаря этому свойству ПЭ широко применяется в полиграфии — с ее помощью упаковывают книги и различные журналы. Поскольку пленки, для изготовления которых используется линейный полиэтилен, являются многослойными изделиями, их можно спокойно эксплуатировать с упакованными ими товарами при температуре в пределах —80…+80 °C.
Термоусадочные материалы из полипропиленовой пленки обладают более высокой прочностью и жесткостью, чем аналогичные изделия из полиэтилена. Они трескаются гораздо меньше, практически не пропуская при этом запахов и водяных паров, и характеризуются низкой степенью паропроницаемости.
Особенности использования термоусадочных пленок
Если говорить о толщине различных термоусадочных пленочных материалов, то покупатель легко может выбрать наиболее подходящий вариант для решения той или иной задачи, естественно, учитывая тип товара, который требуется упаковать. К примеру, чтобы единожды упаковать продукт, достаточно будет пленки толщиной 20–50 микрон, для упаковывания комплекта товаров обычно применяется материал, имеющий толщину 50–100 микрон, а для штапельного упаковывания — пленочные изделия толщиной 100–250 микрон. Готовые термоусадочные пленки поставляются на рынок в виде рукавов (экструзионный метод с раздуванием), полотен и полурукавов (технология плоскощелевой экструзии).
На правах рекламы
Полиолефин – производство пленки, необходимое всем
Подробнее о полиолефиновой пленке >>
Заказать полиолефиновую пленку >>
Полиолефин относится к числу наиболее распространенных термопластов, представители которых – полиэтилен, полибутилен, полипропилен и их сополимеры.
Из полиолефинов методом экструзии получают пленку, трубы, кабельные изделия, разные емкости, профильные и другие изделия. Высокая химическая стойкость ко многим химически активным средам, пробивная и высокая электрическая прочность, а также отличные диэлектрические показатели и сохранение высокой прочности и эластичности при низкой температуре – это еще не весь перечень свойств данного класса полимеров, производство которого растет постоянно.
Полиолефиновая пленка, производство которой происходит на современном оборудовании – это упаковочный надежный материал высокого качества. Само производство выполняется из нетоксичных материалов, а именно их полиолефинов. Заказать такую пленку из полиолефина можно как оптом, так и в розницу, это зависит от того, с какой целью данная упаковка будет использоваться. Например, для крупных производителей практично покупать оптовые партии, а для ежедневных хозяйственных нужд достаточно покупки и обычного рулона в магазине.
Пленка из полиолефина бесцветная и без запаха. Данная упаковочная продукция прозрачнай и имеет глянцевый блеск, поэтому товар, запечатанный в нее, смотрится привлекательно для покупателей. В связи с тем, что полиолефиновая пленка является нетоксичной, в нее можно запечатать абсолютно все: начиная от разных изделий и заканчивая продуктами питания.
В современном мире пленка из полиолефина используется везде: во многих отраслях промышленного производства, во всевозможных торговых точках, в полиграфии, в отраслях непищевого производства.
Каким же образом появляется полиолефиновая пленка? Основная составляющая данного материала – это полиолефин, который обладает замечательными свойствами. Пленка из полиолефина имеет несколько слоев, способных визуально увеличить механический и оптический вид продукции. Она термоустойчивая, легко производится из нетоксичных компонентов, что очень важно для пищевых продуктов.
О преимуществах такой упаковки можно сказать еще очень много. Если производитель мечтает о том, чтобы его продукт выглядел в глазах покупателей эстетично и при этом не хочет расходовать много времени и денег на тару, то пищевая пленка из полиолефина создана именно для него. Сегодня много крупных и мелких предприятий останавливаются свой выбор на данном виде упаковки.
Пленка полиолефиновая термоусадочная – это универсальный и прочный упаковочный материал. Особенность такой пленки – это ее способность сокращаться под действием высокой температуры. Она обтягивает изделие по периметру и принимает его форму, а также защищает его от повреждений и неблагоприятных сред.
Пленка полиолефиновая термоусадочная изготавливается из разных материалов на специализированном оборудовании с применением высококачественного сырья, где за счет внедрения последних технологий она имеет улучшенные физические свойства, высокую упругость и улучшенные изоляционные качества.
Производство термоусадочных пленок из полиолефина происходит на автоматических современных линиях методом экструзии расплавов используемых материалов с дальнейшим раздувом рукавной пленки. Также следует отметить, что для каждого вида пленки применяется своя рецептура, позволяющая получить на выходе продукцию высокого качества. Термоусадочная пленка экологически чистая. Она не выделяет при нагревании раздражающих веществ. Такая упаковка защищает товар от негативного действия в процессе хранения и транспортировки. К тому же термоусадочная пленка из полеолефина имеет прочностные характеристики. Она дает термоусадку при температуре шестьдесят градусов Цельсия. В связи с тем, что данная пленка более прочная, есть возможность использовать более тонкие варианты. Еще один важный плюс такой упаковки заключается в ее небольшой цене при большом количестве. Термоусадочную пленку используют для упаковки хлебобулочных изделий, мясных полуфабрикатов и кондитерских изделий. Она увеличивает срок службы продуктов и защищает их от повреждений.
Пленка Термоусадочная Полиолефиновая полурукав ПОФ пятислойная
Полиолефиновая пленка или пленка ПОФ — это полимерный пятислойный материал.
Термоусадочная полиолефиновая пленка способна усаживаться облегая упаковываемый продукт под воздействием температуры в термотунеле.
Пленка ПОФ имеет большую прозрачность и глянцевый блеск стойкая к маслам, жирам и растворителям. Основные преимущества пленки ПОФ: отсутствие разнотолщинности, низкий удельный вес (плотность ПВХ – от 1,25 до 1,4, полиолефина – 0,92 г/м3) другим словами в одном килограмме пленки ПВХ и пленки ПОФ погонных метров будет больше на 30% в пленке ПОФ.
Термоусадочная полиолефиновая пленка способна сохранять свои свойства и выполнять свою функцию в диапазоне температур: от – 30 до +40 С0. В процессе упаковки не выделяет запаха, и едких вредных веществ.
Полиолефиновая пленка подходит для применения как на высокоскоростных (термонож), так и на купольных упаковочных машинах (термоструна).
Полиолефиновая пленка или пленка ПОФ идеально подходит как для индивидуальной упаковки пищевых изделий и товаров народного потребления, так и для групповой упаковки.
Особое Внимание к этой упаковочной пленке уделяют Кондитерские цеха и пищевые комбинаты, используя пленку ПОФ для упаковки гофролотков, Кондитерских лотков (телевизоров), и индивидуальной упаковки кондитерских изделий.
Пленка Термоусадочная Полиолефиновая полу-рукав ПОФ пятислойная
Поставляется в рулонах упакованных в гофокороб
ширина с шагом в 50 мм шириной от 200 до 600, плотность от 12,5 мкм или 15 мкм и 19 мкм чуть реже используют 25 мкм.
Рекомендуемая плотность
12,5 мкм
Издательско-полиграфическая продукция
Единичная упаковка продукции непрямоугольной формы
15 мкм
Хлебобулочные изделия
Продукция в картонной упаковке
Единичная упаковка продукции непрямоугольной формы
19 мкм
Хлебобулочные изделия
Фасованная продукция на лоточках
Продукция в картонной упаковке
Единичная упаковка продукции непрямоугольной формы
25 мкм
Единичная упаковка продукции прямоугольной форм и острыми концами
Металлические изделия
Для упаковки любых изделий но с большим количеством этапов логистики
Объяснение процесса экструзии выдувной пленки
Экструзия пленки с раздувом — один из многих процессов производства полимеров. Этот метод используется для производства товарных и специализированных полимерных пленок, которые обычно используются в упаковке, такой как термоусадочные, растягивающиеся, барьерные пленки (используемые для защиты мясных деликатесов), упаковки для замороженных пищевых продуктов и пакетов для покупок.
Существует много типов полимеров, которые можно использовать при экструзии пленки с раздувом, наиболее распространенными из которых являются полипропилен и полиэтилен (LDPE, HDPE и LLDPE).С помощью этого метода можно производить однослойные пленки, а также более сложные многослойные пленки, которые включают совместную экструзию для объединения более чем одного пластика в одну пленку.
Процесс экструзии пленки с раздувом
Экструзия пленки с раздувом может быть сложной задачей, поэтому мы подробно объясним каждый этап процесса! Первый шаг — расплавить полимер в экструдере. Полимерная смола, часто в форме шариков, загружается в бункер и с помощью шнека подается в нагретую бочку. Винт используется для транспортировки полимера по стволу.Гранулы постепенно нагревают до расплавления полимера. Температурный профиль является важной частью экструзии, поскольку полимер может термически разрушиться при перегреве. Когда расплавленный материал достигает конца цилиндра, он экструдируется через фильеру. Именно в этом отношении экструзия пленки с раздувом отличается от других процессов экструзии.
Существует несколько различных типов головок, используемых при экструзии пленки с раздувом, наиболее распространенной из которых является кольцевая матрица, которая представляет собой простую круглую головку. Расплавленный полимер поступает в головку фильеры, и воздух нагнетается через отверстие в центре фильеры для радиального надувания полимера в тонкую трубку, диаметр которой во много раз превышает исходный диаметр, полученный при экструдировании.Именно этот этап процесса можно отрегулировать для достижения желаемой толщины и ширины пленки.
Пленка горячей трубы затем охлаждается, обычно с помощью высокоскоростного воздуха, и вытягивается вверх с помощью оборудования, называемого прижимными роликами. На большинстве линий пленки среднего и большого размера эта вертикальная труба может подниматься в воздух на несколько этажей. По мере охлаждения пленка кристаллизуется на так называемой линии замерзания. Когда трубка достигает прижимных роликов в верхней части линии, пленка становится достаточно холодной, чтобы сплющиться, и тогда ее называют плоской или свернутой трубкой.Затем пленка транспортируется роликами вниз по потоку для дальнейшей обработки (например, разрезается, печатается, вентилируется, превращается в пакеты) и в конечном итоге наматывается в рулоны.
Есть несколько преимуществ производства пленки с использованием процесса экструзии с раздувом, включая возможность манипулировать механическими свойствами конечного пластика в зависимости от условий процесса и используемого основного полимера (ов). Например, экструзия пленки с раздувом раздувает полимер в радиальном направлении, одновременно вытягивая его вверх роликами.Эти силы растягивают полимер как в поперечном направлении, так и в направлении вытяжки, обеспечивая прочность пленки. Степень накачивания и вытяжки можно регулировать для достижения желаемой прочности в поперечном направлении и направлении вытяжки конечного продукта. Экструзия пленки с раздувом также универсальна и позволяет производить различные однослойные или многослойные пленки с диапазоном толщины и ширины пленки.
Предложения фильмов Amcor
Как предпочтительный поставщик пластиковых пленок и пакетов, Amcor устранила канал сбыта и продает продукцию напрямую производителям.Сроки выполнения заказа обычно на 50% меньше, чем у наших конкурентов — около 2–3 недель по сравнению с 4–6 неделями. Благодаря широкому спектру возможностей и решений мы являемся жизненно важным партнером в успехе вашей компании в области упаковки. Наши предложения кинопродукции включают:
- Термоусадочные пакеты, трубки, пленка
- Ширина до 240 дюймов
- Цвет и печать
- UVI, VCI, антистат
- Ручная и машинная стретч-пленка
- Пленка БОПП / литая полипропиленовая
- тканый
- Лента
Помимо пластиковой пленки и пакетов, мы специализируемся на полиолефиновых компаундах, добавках, смесях и суперконцентратах. Amcor также является дистрибьютором различных химикатов, смол и газов для пластмассовой промышленности. Имея складские и распределительные мощности в США, Мексике, Восточной Европе и Китае, мы обслуживаем компании любого размера и местоположения в различных отраслях. Помимо продажи продукции, мы также предоставляем техническую поддержку, помощь с вашим оборудованием и рекомендации по технологическим процессам.
Мы понимаем, что своевременная доставка, качественный продукт и индивидуальное обслуживание — это все, что нужно.Свяжитесь с нами сегодня, чтобы узнать, как мы можем помочь с вашим следующим проектом!
Основы экструзии литых пленок
Процесс экструзии литой пленки становится все более популярным и устойчивым во всем мире. Новые линии устанавливаются в значительном количестве, и сегменты рынка, на которые распространяется эта технология, находятся на подъеме. В этой статье определяются основные компоненты линии экструзии литья и представлены фундаментальные аспекты, которые необходимо учитывать при подходе к технологии литья пленки.
Применение экструзии литья
Литые пленки используются для упаковки пищевых продуктов и текстиля, упаковки цветов, в качестве защитных материалов для страниц фотоальбомов, в качестве подложек для нанесения покрытий в процессах нанесения экструзионного покрытия или ламинируются с другими материалами, в частности, с образованием более сложных пленок. Обычно процесс литья пленки включает использование соэкструзии, которая представляет собой одновременную экструзию двух или более материалов из одной головки с образованием многослойной пленки.Это связано с тем, что во многих случаях окончательное нанесение пластиковой пленки требует рабочих характеристик, которые не могут быть достигнуты, если пленка состоит только из одного материала. Например, во многих случаях для упаковки пищевых продуктов требуется использование пленок с кислородным барьером. Чтобы удовлетворить это требование, материал с высоким кислородным барьером, такой как EVOH, объединяется с полиолефиновыми материалами в многослойную структуру. Соэкструдированные пленки обычно содержат до семи слоев; однако использование большего количества слоев становится все более распространенным.Количество слоев, их положение в соэкструдате и их индивидуальная толщина — все это переменные, которые меняются в зависимости от конкретного применения пленки.
Преимущества / ограничения экструзии литья
В отличие от процесса экструзии с раздувом, охлаждение пленки при экструзии литья очень эффективно. Это позволяет увеличить скорость производственной линии, что приводит к более высокой производительности с превосходными оптическими свойствами продукта.Степень вытяжки и ориентации в процессе литья пленки значительно ниже, чем в процессе экструзии с раздувом. По этой причине распределение толщины
в поперечном направлении машины более однороден с процессами литья (с отклонениями, которые могут составлять всего ± 1,5%). Однако механические свойства пленки в поперечном направлении машины ниже по сравнению со свойствами, полученными с помощью процесса экструзии с раздувом, из-за более высокого уровня ориентации, которую пленка испытывает в процессе экструзии с раздувом.
При литьевой экструзии края пленки обрезаются из-за неровностей размеров и / или плохого распределения слоев. В результате на процесс может негативно повлиять, если обрезанный материал не может быть переработан. Недавние технологии систем плоских фильер позволили свести к минимуму эту проблему за счет значительного сокращения количества отходов, расходуемых в процессах совместной экструзии. В некоторой степени этот вопрос будет рассмотрен в следующем разделе.
Основные концепции экструзии литья
В процессе экструзии литой пленки расплавленный полимер проходит через систему плоских фильер, чтобы принять свою окончательную форму плоской пленки.Система фильер образована фильерой и блоком подачи (если процесс требует совместной экструзии) или просто фильерой, если процесс представляет собой однослойную экструзию.
Процесс начинается с подачи пластмассовых смол с помощью гравиметрической системы подачи в один или несколько экструдеров. Затем материалы плавятся и смешиваются экструдерами, фильтруются и подаются в систему фильер.
Сразу после выхода из фильеры расплавленная завеса поступает в охлаждающую установку, где ее температура понижается охлаждающим валком с водяным охлаждением, чтобы «заморозить» пленку.Затем пленка проходит вниз по потоку, где кромки обрезаются, применяется обработка коронным разрядом (если требуется производственный процесс, такой как печать или нанесение покрытия), и пленка наматывается в рулоны. Описание основных компонентов типовой линии для литья пленки представлено ниже.
Компоненты линии литья пленки
Система гравиметрической подачи
Системы гравиметрической подачи контролируют количество материала, подаваемого в экструдеры, по весу, а не по объему.Система более точна, чем ее объемный аналог, и отличается пониженным допуском погрешности порядка ± 0,5%. Во многих случаях пленка изготавливается из материалов, которые представляют собой смеси основного полимера с одним или несколькими вторичными компонентами. На современных производственных линиях это смешивание осуществляется поточно.
Необходима особая осторожность, чтобы предотвратить преждевременное плавление гранул, особенно при обработке материалов с низкими температурами плавления или при небольшом размере гранул.Для решения этой проблемы рекомендуется использовать вибрацию и охлаждение загрузочных бункеров. Также важно следить за тем, чтобы подаваемый материал не содержал влаги, которая могла бы вызвать появление маленьких пузырьков, также известных как «рыбий глаз», в конечной пленке. В некоторых случаях требуется сушка материала. Это может быть выполнено с помощью отдельного устройства или сложной системы подачи со встроенными функциями сушки.
Экструдер
Основные функции экструдера — расплавить пластмассовые гранулы и смешать полученный расплавленный полимер для достижения однородного расплава.Для этого материал перемещается по нагретому цилиндру с помощью вращающегося винта. Имеющиеся в продаже цилиндры экструдеров обычно имеют диаметр от 3½ дюймов (90 мм) до 6 дюймов (150 мм). Шнеки адаптированы к конкретным характеристикам экструдированных материалов и параметрам процесса. На длину винта сильно влияет их диаметр. Отношение длины винта к диаметру (L / D) обычно находится в диапазоне от 26: 1 до 30: 1.
Крайне важно обеспечить, чтобы поток, выходящий из экструдера, хорошо контролировался и был постоянным, с вариациями скорости вращения шнека, не превышающими ± 1%.Неспособность точно контролировать скорость вращения шнека обычно приводит к нежелательному пульсирующему потоку, который может вызывать периодические изменения толщины пленки в машинном направлении.
Дозирующая секция или последняя секция экструдера предназначена для обеспечения точного дозирования материала из экструдера. Для достижения вышеуказанного зазор между винтом и стволом очень мал. Это создает еще одну проблему, поскольку трудно поддерживать постоянный зазор между вращающимся винтом и цилиндром.
Для преодоления вышеупомянутых потенциальных проблем после экструдера обычно используется насос для расплава. Насос представляет собой устройство прямого вытеснения, которое обеспечивает постоянный поток независимо от давления на выходе экструдера (рисунки 2 и 3). Насос снижает нагрузку на экструдер, создавая давление. Пониженное давление в головке экструдера приводит к экономии энергии, падению температуры расплава и меньшему износу цилиндра и шнека.
В линиях совместной экструзии количество экструдеров зависит от количества различных экструдируемых материалов, а не обязательно от количества слоев. Это связано с тем, что существующая технология блока подачи позволяет разделить поток из одного экструдера на два или более слоев в конечном соэкструдате.
Система фильтрации
Целью системы фильтрации является предотвращение прохождения ниже по потоку примесей из расплава и / или гелей, которые образуются в процессе экструзии.Правильный контроль на этом этапе является обязательным для предотвращения загрязнения расплава. Наиболее распространены фильтры с металлической сеткой. Корпус, в котором размещается фильтрующий материал, должен быть способен выдерживать силы, создаваемые потоком полимера, когда он подвергается максимальному давлению, допускаемому процессом экструзии.
Настоятельно рекомендуется использовать устройства смены сита непрерывного действия, в которых сетка постоянно регенерируется, чтобы минимизировать время замены сита.
Система с плоской матрицей
Можно сказать, что система фильер — это сердце любой линии соэкструзии. Система фильеры образована блоком подачи для совместной экструзии, плоской головкой и адаптерами для переноса расплава, которые транспортируют различные расплавленные полимеры из экструдеров к входным отверстиям блока подачи. Качество соэкструдированной пленки и производительность процесса во многом зависят от конструкции и рабочих характеристик системы фильер.
Основная функция системы фильер заключается в формировании многослойной пленки, которая равномерно распределена по ширине фильеры с вариациями толщины пленки и вариаций толщины каждого отдельного слоя в пределах принятых в промышленности допусков (не превышающих ± 2,5% для общей толщины и в пределах от ± 15 до ± 20% для каждого слоя).
Перед блоком подачи находятся переходники для переноса расплава. Критерии проектирования этой капиллярной системы должны учитывать такие параметры, как время пребывания материала, падение давления и контроль температуры.Например, чрезмерное падение давления можно решить путем увеличения диаметра трубы; однако это, в свою очередь, увеличит время пребывания материала и повысит вероятность разрушения материала. Кроме того, необходимы точный выбор толщины стенок и надлежащие характеристики нагревателя, чтобы трубы не нагревали или охлаждали расплавы, которые они транспортируют. Задача дизайнера — найти правильный баланс между всеми этими переменными.
Блок подачи соэкструзии размещает различные потоки расплава в заданной последовательности слоев и генерирует столько потоков расплава, сколько слоев должно быть в конечном соэкструдате.Как только это будет сделано, каждый поток принимает плоскую геометрию, встречается с соседними слоями, и формируется конечный плоский соэкструдат.
Фидблоки соэкструзии сгруппированы в две категории: блоки с фиксированной и переменной геометрией. В верхней части этих блоков находится так называемая селекторная заглушка или селекторная катушка. Эта съемная часть цилиндрической формы отвечает за направление каждого потока расплава в его окончательное положение в соэкструдате. Пробка, если требуется, также разделяет эти потоки с материалом, который питает более одного слоя в конструкции.Если требуется другая последовательность слоев, это может быть достигнуто путем простой замены заглушки.
Блоки с фиксированной геометрией наиболее эффективны, когда производственная линия предназначена только для нескольких различных продуктов, схожих по своим реологическим свойствам. Однако стоит отметить, что эти блоки имеют съемные проточные вставки, которые можно обрабатывать или заменять при необходимости обработки более широкого спектра материалов.
Фидблоки с изменяемой геометрией идеальны для совместной экструзии материалов с высокой добавленной стоимостью или когда объем производственной линии более разнообразен.Как правило, эти блоки имеют подвижные внутренние компоненты, которые могут регулировать распределение ширины отдельного слоя до встречи с соседними слоями и / или его скорость, что, в свою очередь, влияет на скорость сдвига и вязкость. Таким образом, проблемы, присущие совместной экструзии, такие как искажение слоя и межфазная нестабильность, могут быть преодолены путем регулировки блока питания.
Несмотря на все возможности технологии соэкструзионного фидблока по устранению аномалий потока, присущих потокам соэкструзии, производство оптимального соэкструдата возможно только в том случае, если фидблок работает вместе с головкой, спроектированной и должным образом спроектированной для обработки потока соэкструзии.Идеальная синергия между штампом и фидблоком — это то, что гарантирует высокое качество продукта.
Хорошо сконструированная фильера должна гарантировать, что в процессе распределения соэкструдата, выходящего из блока подачи, плоскостность каждого отдельного слоя поддерживается в пределах от ± 15 до ± 20%. Он также должен быть спроектирован так, чтобы время пребывания не было чрезмерным, чтобы предотвратить проблемы деградации или, в некоторых случаях, предотвратить нежелательную теплопередачу между слоями.Мундштук также должен быть спроектирован так, чтобы падение давления поддерживалось на уровне, нормальном для процесса экструзии.
Также критически важно, чтобы матрица имела соответствующий размер, достаточную массу стали и надлежащую механическую конструкцию, чтобы гарантировать термическую стабильность и минимизировать так называемую проблему расслоения, которая проявляется как чрезмерная деформация кромок матрицы при перемещении матрицы. подвергается воздействию высоких давлений, свойственных экструзии тонких пленок.
Последние достижения в технологии штампов повысили производительность линий по производству литых пленок. Особо следует отметить так называемые внутренние декели. Установленные на обоих концах матрицы, декели позволяют изменять ширину пленки и, как следствие, уменьшать обрезку. Они могут быть фиксированными или регулируемыми, а их длина может превышать 20 дюймов.
В последнее время была внедрена технология герметизации кромок для снижения негативного финансового воздействия отходов материала, вызванного тем, что обрезки соэкструдата не подлежат вторичной переработке.На предыдущем рисунке показана полоса из одного материала, совместно экструдируемая вместе с соэкструдатом. Инкапсулирующий материал имеет низкую стоимость, пригоден для вторичной переработки и обладает высокими механическими свойствами. Герметизирующий материал в основном образует облицовку, что позволяет повторно использовать ее в производственном процессе и значительно экономить на стоимости материала. Кроме того, технология герметизации кромок полностью совместима с технологией внутреннего декеля.
Блок охлаждения
Блок охлаждения состоит из первичного закалочного валка, вторичного валка, моторизованной системы позиционирования валков для правильного выравнивания валков в вертикальном и поперечном машинном направлении и во многих случаях вакуумной камеры и / или воздушного ножа.
Ролики обычно хромируются для достижения лучшего качества поверхности и улучшения процесса теплопередачи во время пленочного охлаждения. Охлаждающим агентом обычно является вода, которая циркулирует внутри валков. Валок первичной закалки охлаждает одну сторону пленки, а вторичный валок охлаждает противоположную сторону пленки.
Матрица расположена над валком первичной закалки под углом от 45 ° до 90 °.Расстояние между выходом кромки матрицы и валком составляет от 0,8 до 2 дюймов.
Система охлаждения позволяет линии работать на высоких скоростях. По мере того, как требования к скорости линии возрастают, диаметры валков увеличиваются.
Ролики должны быть точно выровнены по полотну, чтобы гарантировать равномерное натяжение и свести к минимуму отклонения толщины по ширине пленки. Кроме того, необходимо хорошо контролировать угловую скорость валков, чтобы предотвратить колебания толщины пленки в машинном направлении.
Использование вакуумной камеры, соединенной с неподвижным корпусом матрицы, необходимо в определенных областях применения, таких как применение литого полипропилена, где требуется более эффективное охлаждение. Материалы из полипропилена, если не охлаждают их агрессивно, имеют тенденцию к образованию кристаллов, которые в конечном итоге приводят к образованию мутных пленок.
Вакуумная камера удаляет увлеченный воздух между поверхностью первичного закалочного валка и пленкой, чтобы минимизировать воздушный барьер между горячим полотном и валком. Этот воздушный барьер, если его не уменьшить, действует как теплоизоляционная подушка, препятствующая процессу охлаждения пленки.Коробка также уменьшает количество сужений в пленке и воздушный зазор и позволяет использовать более высокие линейные скорости.
Вакуумный ящик можно комбинировать с воздушным ножом или воздушной камерой для дальнейшего улучшения охлаждения полотна.
Система автоматического управления манометром
Встроенное измерение и контроль распределения толщины пленки по ее ширине — это функция системы контроля толщины или APC (автоматический контроль профиля).Когда гибкая кромка на матрице управляется вручную и производственный процесс хорошо отлажен, изменения толщины пленки будут в диапазоне от ± 3 до ± 5%. В автоматическом режиме эти отклонения можно уменьшить вдвое. На рисунке ниже показан автоматический штамп с модулем автоматического управления, установленным на гибком корпусе штампа. Так называемые термопреобразователи или термоболты образуют модуль. Расстояние между болтами обычно составляет 1,125 дюйма.
Система управления датчиками включает в себя блок излучения излучения и пульт управления.Блок излучения движется в поперечном направлении машины, циклически сканируя пленку (измеряется в минутах). Обычно излучение исходит от источника бета-излучения; хотя также можно использовать источники рентгеновского и инфракрасного излучения. В общих чертах, толщина пленки определяется как функция скорости поглощения излучения пленкой. Таким образом, изменение скорости поглощения приводит к изменению толщины пленки.
Пульт управления — это интерфейс между системой управления и автоматическим штампом.Каждая точка регулировки или термопреобразователь на матрице пространственно коррелирует с положением на пленке. Это называется отображением.
Система управления подает питание на термопреобразователи по мере необходимости, а зазор губ регулируется посредством теплового расширения регулирующего элемента. Важной переменной, связанной с APC, является постоянная времени. Он определяется как время, необходимое регулировочному элементу для удлинения 62,3% от его максимального удлинения. Чем короче постоянная времени, тем быстрее реагирует система, что приводит к увеличению производительности.
Корона лечение
Чтобы облегчить прилипание красок или покрытий к поверхности пленки, необходимо нанести поверхностную обработку. Лечение коронным разрядом — наиболее часто используемый из существующих методов. Обработка коронным разрядом увеличивает поверхностную энергию пленки и, следовательно, ее поверхностное натяжение. Система включает источник питания и станцию очистки. Источник питания преобразует мощность электростанции 50/60 Гц в мощность более высокой частоты в диапазоне от 10 до 30 кГц.Эта более высокочастотная энергия подается на станцию обработки и применяется к поверхности пленки с помощью двух электродов, один с высоким потенциалом, а другой с низким потенциалом, через воздушный зазор, который обычно составляет от 0,5 дюйма до 1 дюйма. Поверхностное натяжение на поверхности пленки увеличивается, когда возникающая высокая разность потенциалов ионизирует воздух.
Обработка коронным разрядом может проводиться на линии или как отдельный последующий процесс после производства пленки.Если выполняется на линии, особое внимание следует уделять потенциальному образованию токсичного озона. В некоторых случаях необходимо предусмотреть систему вентиляции в производственной зоне.
Winder
Проще говоря, намотчики используются для превращения экструдированной пленки в рулоны материала. Процесс наматывания должен быть таким, чтобы пленка сохраняла свои свойства и размеры, когда эти рулоны разматываются и превращаются в других последующих процессах.
Есть три основных типа намоточных машин; поверхностные намоточные устройства, револьверные или центральные намоточные устройства и центральные / поверхностные намоточные устройства. Поверхностные намотчики наматывают пленку через контакт между барабаном большого диаметра и намоточным валом, который прижимается к барабану с переменным давлением. Револьверные намоточные устройства или центральные намоточные устройства — это намоточные машины любого типа, в которых используется ведомый вал, проходящий через центр строительного валка или на зажимных патронах, поддерживающих сердечник, для приведения в движение строительного валка. Наконец, при комбинированном подходе с намоткой по центру / поверхности (или намоточной машине с зазором) сохраняется небольшой зазор между поверхностным намоточным валком или наматывающим валком и намоточным валком.Система центрального привода приводит в движение намоточный валок независимо от поверхностного барабана.
Пленки могут быть липкими или иметь некоторую степень скольжения, иметь высокую или низкую эластичность, тонкие или толстые, требуемый диаметр рулона может быть большим или маленьким; рулоны могут быть узкими или широкими, мягкими или твердыми. Технология намотки сложна, и правильный тип намоточной машины, используемой в конкретном приложении, зависит от всех вышеперечисленных переменных.
Использование револьверных или центральных мотальных машин типично для литья пленки.С этим типом намотки натяжение полотна уменьшается по мере увеличения диаметра рулона. Это контролируется скоростью вращения намоточного шпинделя. Укладка в рулон предотвращает или позволяет захватывать небольшое количество воздуха между слоями. Последний рекомендуется для намотки пленок с высокой липкостью или для намотки мягких рулонов.
Для равномерного распределения дефектов на экструдированной пленке (вариации толщины) используется рандомайзер. Рандомайзер перемещает пленку вперед и назад по мере того, как она разрезается и наматывается.Альтернативный подход заключается в перемещении продольно-резательного станка и намотчика вперед и назад относительно пленки.
Компьютеризированная система контроля и управления
Перечислены и описаны основные компоненты литейной экструзионной линии. Эти компоненты не действуют сами по себе, а интегрированы и управляются компьютеризированной системой контроля и управления.
Главный компьютер — это мозг, который объединяет и управляет всеми компонентами линии согласованным образом.
Основные задачи компьютера:
Контролировать пуск, останов и скорость линии;
Для контроля веса материала, подаваемого в экструдеры, и для контроля скорости экструдеров для поддержания постоянной производительности;
Контролировать все температурные зоны и температуру всех материалов;
Координировать взаимодействие между системой управления калибром, реакцией автоматического штампа и линейной скоростью;
Для контроля натяжения полотна; и
Для хранения и обработки всех рецептов продуктов, хранения рабочих данных и управления системой сигнализации.
Хорошая система управления должна предоставлять операторам простой в использовании графический интерфейс или систему мониторинга.
Специальные приложения
В этом разделе описаны некоторые сложные соэкструдированные структуры, которые включают материалы с высокой добавленной стоимостью, пользующиеся растущим спросом на международных рынках упаковки пищевых продуктов.
В таблице ниже приведены характеристики этих соэкструдированных пленок.В структурах EVOH используется для обеспечения кислородного барьера, присутствие PP в качестве поверхностного слоя способствует термоформованию пленки, а PE, используемый в качестве поверхностного слоя, действует как термосвариваемый материал. Комбинирование PVdC с EVOH является эффективным способом решения проблемы потенциальной потери кислородного барьера, которую испытывает EVOH при воздействии влаги, как в случае упаковки для мяса. Нейлоновый материал используется в сочетании с EVOH для обеспечения дополнительного барьера при термоформовании пленки, а жесткость EVOH ограничивает толщину слоя EVOH.
Как видно, процесс спецификации этих структур — непростая задача, и необходимо учитывать несколько переменных. Компании, желающие диверсифицировать свой продуктовый портфель за счет включения специальных пленок, должны знать, что высокая стоимость смол с добавленной стоимостью и постоянно меняющийся рынок являются факторами, которые требуют использования высокотехнологичного технологического оборудования, которое является достаточно гибким для эффективного использования в производство как товарных, так и специализированных пленок.
Заключительные замечания
В данной статье перечислены и приведены основные параметры функционирования всех основных компонентов линии по производству литой пленки. Технология каждого компонента сложна, как и их взаимодействие и функциональная интеграция в линию.
Во избежание преждевременного технологического устаревания оборудования перед покупкой оборудования необходимо уделить особое внимание.
Совершенно необходимо четко понимать, какой продукт и его область применения должны производиться на линии. Идея всеобъемлющей «универсальной» линии может быть привлекательной, но на самом деле такой линии не существует. Чем более обобщенно спроектирована линия, тем менее оптимизирован продукт, который может быть произведен, поскольку компоненты линии могут не подходить для требований процесса, специфичного для продукта. Кроме того, разливочные линии промышленных размеров рассчитаны на длительные производственные циклы, которые не подходят для частой смены продукта — работа литейных линий регулярно требует значительного количества корректировок процесса.Производство сложных и сложных пленок часто требует большого количества времени на точную настройку, особенно во время проявления структуры пленки. Даже с комплексным программным обеспечением Macro, которое помогает инженеру-технологу прогнозировать поведение многослойных структур, обычно требуется множество испытаний для достижения заданных механических, физических, оптических и технологических параметров.
Все компоненты литейной линии влияют на общую производительность всей линии. Чтобы получить первоклассную линию, подходящую для производства продукта превосходного качества, каждый из отдельных компонентов или систем должен быть одинаково высокого качества.
Ожидается, что представленные выше концепции служат целям ознакомления с технологией литых пленок для тех, кто плохо знаком с ней, и укрепления базы знаний тех, кто уже знаком с этим производственным процессом.
ЛИНИЯ ЭКСТРУЗИИ ИЗ ТРЕХ — ПЯТИ СЛОЙ ПОФ УСАДКИ, Пластиковый экструдер
информация о продуктеИспользование и особенности
Эта установка представляет собой установку для выдувания полиолефиновой термоусадочной пленки методом двойного формования, независимо разработанную нашей компанией с использованием передовых зарубежных технологий, и оснащена новыми технологиями трехслойной совместной экструзии, конической наложенной экструзионной головки, системы инфракрасного нагрева. , контроль температуры модуля регулирования мощности, инфракрасная система определения температуры, контроль натяжения и снижение тяги и вращения.Производимые термоусадочные пленки POF со структурой PP / PE / PP обладают комплексными характеристиками высокой прозрачности, устойчивости к низким температурам, устойчивости к замешиванию и высокой усадки, а усадку пленок в разных направлениях можно контролировать, меняя компоненты и регулируя технологию. Полиолефиновая термоусадочная пленка — это экологически чистый термоусадочный упаковочный материал, обычно используемый в термоусадочной упаковке для продуктов питания, напитков, лекарств, товаров здравоохранения, канцелярских товаров, косметики, предметов искусства, книг и газет, аудиовизуальных продуктов, электрических фурнитура, игрушки и тому подобное.
Основные технические параметры : | |||||
Модель | GJSM-1300 | GJSM-1500 | GJSM-1800 | GJSM-2400 | GJSM-2600 |
Макс.ширина фальцовки пленки | 1100 мм | 1300 мм | 1600 мм | 2200 мм | 2400 мм |
Толщина пленки | 0.012-0,03 мм | 0,012-0,03 мм | 0,012-0,03 мм | 0,012-0,025 мм | 0,012-0,026 мм |
Макс. Выход | 60-80 кг / ч | 70-100 кг / ч | 100-130 кг / ч | 150-200 кг / ч | 200-260 кг / ч |
Применяемые материалы | PP 、 PE | PP 、 PE | PP 、 PE | PP 、 PE | PP 、 PE |
Диаметр винта (мм) | Φ45мм | Φ45мм | Φ55мм | Φ60 мм | Φ65мм |
Отношение длины к диаметру винта | 30: 1 | 30: 1 | 30: 1 | 30: 1 | 30: 1 |
Скорость винта | 10-100 об / мин | 10-100 об / мин | 10-100 об / мин | 10-100 об / мин | 100об / мин |
Мощность двигателя | 11 кВт 、 37 кВт 、 11 кВт | 11 кВт 、 37 кВт 、 11 кВт | 15 кВт 、 55 кВт 、 15 кВт | 22 кВт 、 75 кВт 、 22 кВт | 37 кВт 、 90 кВт 、 37 кВт |
Макс.диаметр прокатки. | 500 мм | 500 мм | 500 мм | 500 мм | 500 мм |
Макс.скорость прокатки | 60 м / мин | 60 м / мин | 60 м / мин | 60 м / мин | 60 м / мин |
Суммарная мощность нагрузки | 250 кВт | 260 кВт | 300 кВт | 380 кВт | 480 кВт |
Габаритные размеры | 10000 × 5600 × 10500 мм | 10500 × 5600 × 10500 мм | 12000 × 6600 × 14200 мм | 14000 × 7600 × 16000 мм | 16000 × 8600 × 18000 мм |
Вес (приблизительный) | 30000 кг | 32000 кг | 38000 кг | 50000 кг | 60000 кг |
Дизайн и технические характеристики могут быть изменены без предварительного уведомления. |
Агенты скольжения: расширенный диапазон характеристик для полиолефиновых пленок
Инжир.1 — Немиграционные промахи показывают небольшое изменение COF за 62 дня, исключая одну технологическую переменную. (Маточная смесь Ampacet 101501 в двухслойной литой пленке LDPE толщиной 2 мил.)
Рис. 2 — Испытания с новым типом скользящей добавки (Ampacet 102794) показывают постоянный коэффициент трения до и после ламинирования, в отличие от стандартного 1% эрукамида (Ampacet 100497) и немигрирующего скользящего вещества (Ampacet 101501). Трехслойные соэкструдированные пленки толщиной 2 мил с герметизирующим слоем из мЛПЭНП и двумя слоями октен-ЛПЭНП ламинировали с ПЭТ с помощью полиуретанового клея на основе растворителя.
Предыдущий СледующийСегодняшние маточные смеси для шликера для полиэтиленовых пленок низкого давления, линейного полиэтилена низкой плотности и других полиолефиновых пленок предлагают более широкий диапазон эксплуатационных характеристик, чем в прошлом. Эти продукты варьируются от традиционных амидных шликеров — преобладающих марок, используемых в настоящее время, — до более новых специальных, немигрирующих марок, которые могут удовлетворить такие потребности, как способность хорошо работать при более высоких температурах, повышенная надежность и удерживающий коэффициент трения (COF). устойчивая до и после ламинирования.Процессоры должны знать о новых альтернативах, которые преодолевают предыдущие ограничения промахов.
Добавки, снижающие скольжение, снижают естественную липкость смол, поэтому они могут плавно перемещаться через оборудование для обработки и упаковки. Пленки LDPE и LLDPE обычно делятся на категории с низким, средним или высоким скольжением, в зависимости от их коэффициента трения. Уровень COF обычно соответствует тому, сколько скольжения они содержат (см. Таблицу 1).
Суперконцентраты скольжениядоступны в формулах, которые учитывают различные скорости диффузии, конечные температуры использования, базовые смолы и типы чернил.Традиционные шликеры основаны на амидах ненасыщенных жирных кислот, чаще всего олеамиде и эрукамиде. Эти первичные амиды быстро мигрируют через полиолефиновые пленки после экструзии и появляются на поверхности пленки, снижая COF.
Другие шликеры на основе вторичных амидов имеют почти вдвое большую молекулярную массу, чем первичные амиды, и поэтому мигрируют в полиолефинах медленнее. Традиционные первичные и вторичные амиды коммерчески предлагаются в виде носителей из LDPE, LLDPE и mLLDPE.
Новые суперконцентраты шликеров включают немигрирующие шликеры с очень большими молекулами и специализированные составы, адаптированные для ламинирования.Специальные марки могут состоять из смесей первичных шликеров или первичных и вторичных амидных шликеров, а также различных смол-носителей, таких как PP, EMA и EVA.
Стандартные миграционные талоны
Кинопроизводители склонны полагаться на амидные шликеры, потому что они снижают коэффициент трения по разумной цене. Плавки первичного и вторичного амида позволяют переработчикам выбирать коэффициент трения от 0,1 до 0,4.
Концентрация проскальзывания в маточной смеси обычно составляет от 5% до 10%. Концентрации мигрирующего скольжения обычно находятся в диапазоне от 200 до 2000 ppm в реальных пленках.Более тонкие пленки обычно требуют более высоких концентраций скольжения для достижения заданного коэффициента трения. Эрукамид более широко используется, поскольку он получен из неживотных источников и имеет тенденцию быть несколько более термостабильным, чем олеамид.
Пленкам требуется период кондиционирования после экструзии, чтобы можно было установить равновесие между скольжением на поверхности пленки и скольжением внутри нее. Поскольку большая часть снижения COF происходит в течение первого дня (таблица 2), COF в пленках LDPE и LLDPE обычно измеряется через 24 часа после экструзии.
COF и скорость миграции скольжения обычно подбираются для конечного использования. Более быстрое распространение проскальзывания важно для поточного формования и преобразования в пакеты и другие продукты. Для рулонного материала требуется более медленное распространение проскальзывания, чтобы COF не падал слишком быстро и не приводил к затруднениям намотки и выдвижению рулонов.
Факторы миграции
Многие переменные влияют на скорость миграции и конечный коэффициент трения. Диффузия в полимере происходит быстрее с меньшими молекулами скольжения и более высокими концентрациями.Также важна природа полимера. Молекулы скольжения диффундируют в основном через аморфные области полиолефина, поэтому миграция происходит медленнее в более кристаллических смолах, таких как HDPE и PP, чем в LDPE или LLDPE.
Высокоаморфные и липкие полимеры, такие как марки mLLDPE с низкой плотностью (<0,92 г / см 3), требуют высоких нагрузок скольжения. Полярные полимеры, такие как EVA или EMA, могут взаимодействовать с функциональными группами скольжения и замедлять его миграцию.
Миграция шликеров через полиолефины в намотанном рулоне происходит медленнее, чем в размотанном.Чем больше натяжение намотки, тем меньше скорость диффузии.
Кроме того, антистатики и противотуманные средства могут конкурировать с промахами за участки на поверхности и во время диффузии. Эти добавки имеют более крупные молекулы, чем первичные амидные шликеры, поэтому они перемещаются медленнее. Некоторые антиблоки могут адсорбировать молекулы скольжения и отрицательно влиять на их диффузию.
Обработка в нисходящем направлении также может влиять на COF. Например, обработка коронным разрядом перед печатью выжигает поверхностный слой скольжения и делает поверхность полярной.В результате к обработанной коронным разрядом стороне перемещается больше скольжения, чем к необработанной.
Первичные амидные шликеры имеют термические ограничения. Хотя они хорошо работают с пленками, полученными экструзией с раздувом, обрабатываемыми при 400 F, они имеют тенденцию улетучиваться при более высоких температурах. Они не подходят для использования с литыми пленками, которые обычно производятся при температуре от 500 F до 550 F, или для нанесения покрытия экструзией, которое обычно выполняется при 600 F. Это также относится к пленкам, которые должны проходить через элементы машины из горячего металла.
Вторичные амидные шликеры обладают лучшими тепловыми характеристиками и используются при более высоких температурах.Они мигрируют медленнее, чем их первичные амидные аналоги, и, следовательно, обеспечивают лучший контроль COF. Кроме того, они с меньшей вероятностью будут мешать печати и термосвариванию. Вторичные амиды иногда выбирают, когда решающее значение имеет баланс скольжения и антиблокировочные свойства.
Не миграционные талоны
Появившиеся в конце 1990-х годов немигрирующие шликеры имеют молекулярную массу от 30 до 50 раз больше, чем первичные и вторичные амиды. Их большой размер не позволяет им диффундировать через полимер, поэтому снижение их COF обеспечивается молекулами скольжения, которые оказываются на поверхности во время экструзии.
В результате им не требуется период кондиционирования, и их смазывающая способность остается относительно стабильной, поскольку пленка проходит через ламинирование, преобразование, печать, транспортировку и другие этапы. COF, который они обеспечивают, также имеет тенденцию быть более однородным по всей пленке, чем при использовании первичных амидных шликеров.
Немигрирующие промахи обычно дают COF от 0,20 до 0,40, в зависимости от уровня использования (таблица 3). Стабильность COF от 15 до 62 дней после отливки LDPE с немигрирующим шликером показана на рис.1.
В отличие от миграционных накладок, эти типы необходимы только во внешних слоях многослойных пленок. Это делает немигрирующие клинья более рентабельными в многослойных пленках, даже несмотря на то, что в этих внешних слоях требуются более высокие уровни (от 1% до 2%). Немигрирующие скольжения уменьшают потребность в передозировке количества скольжения, чтобы создать резервуар в пленке, чтобы обеспечить достаточную миграцию на поверхность. Кроме того, постоянный COF с немигрирующими клиньями устраняет одну переменную процесса, что помогает уменьшить брак во время преобразования.
Немигрирующие шликеры стабильны при высокой температуре и не могут отрицательно повлиять на термосварку полиэтиленовой пленки, если она выполняется при соответствующей температуре. Они также могут использоваться в литых пленках и выдерживать повышенные температуры горячего розлива, термоусадочных туннелей и других операций. Пленки, изготовленные с немигрирующими накладками, обладают хорошей прочностью герметизации. Например, прочность герметизации двухслойной литой пленки LDPE толщиной 2 мил с немигрирующим скольжением только в слое герметика составляла 2423 фунта на квадратный дюйм с добавлением 10% маточной смеси скольжения и 2491 фунтов на квадратный дюйм с 20% маточной смеси скольжения.
Суперконцентраты с немигрирующим скольжением доступны с 10% и 20% скольжения для выдувных пленок из ЛПЭНП, литых пленок из ПЭНП и экструзионных покрытий, а также для литых пленок из полипропилена. Эти шликеры могут перемещаться по поверхности пленки на плотно намотанных рулонах, и они снижают прозрачность пленки больше, чем первичные или вторичные амиды.
Новинка для ламинирования
Коэффициент трения полиэтиленовых пленок, содержащих эрукамидный агент скольжения, часто повышается, когда пленки приклеиваются к другим пленкам. Считается, что это происходит потому, что эрукамид притягивается к адгезивам или к полярным субстратам, таким как ПЭТ или нейлон, используемым при ламинировании клеем.
Скольжение, отводимое от поверхности полиэтиленового герметика, может привести к увеличению коэффициента трения до 1,0 или более, что затрудняет перемещение пленки при использовании вертикального формования-заполнения-уплотнения, печати и другого оборудования для обработки. Потеря COF более выражена в ламинированных пленках, которые остаются некоторое время перед преобразованием или печатью.
Недавно представленный тип скольжения может предотвратить эту проблему, оставаясь в полиэтиленовом слое. Тридцатидневные испытания показали, что одна из таких накладок (Ampacet 102794) удерживает устойчивый коэффициент трения до и после ламинирования (рис.2). Этот шликер сравнивали с обычным эрукамидом и немигрирующим шликером в пленках толщиной 2 мил с трехслойной соэкструдированной структурой, обычно встречающейся в гибкой пищевой упаковке — герметизирующий слой из мЛПЭНП плюс два слоя октен-ЛПЭНП. Пленки были ламинированы на пленку из полиэтилентерефталата полиуретановым клеем на основе растворителя.
COF в образцах, содержащих новый шликер, установилось на 0,2 до и после ламинирования. COF в пленках со стандартным эрукамидом подскочил более чем в пять раз до 0.68 и 0,85 после ламинирования, в то время как COF в пленках с немигрирующим проскальзыванием незначительно вырос с примерно 0,35 до примерно 0,5.
Опыт показывает, что новый состав скольжения должен аналогичным образом работать с другими пленочными структурами, такими как соэкструдированные пленки ЛПЭНП с герметизирующим слоем из этиленвинилацетата. Ampacet 102794 является рентабельным, поскольку его можно использовать с коэффициентом разбавления 2%. Кроме того, нет необходимости в передозировке, чтобы компенсировать потерю скольжения в слое герметика из-за ламинирования.
Экструзия пленки с раздувом |
Упаковочные пленки Styrolux сочетают в себе высокую прозрачность и блеск и стойкость.Области применения пленок Styrolux включают упаковку, термоусадку. упаковка и этикетки. Чрезвычайно высокая проницаемость для газов и воды пар по сравнению с другими пластиками может быть преимуществом для упаковки свежих продукты. Например, свежий хлеб и пирожные можно упаковать с помощью Styrolux. пленки вместо полиэтиленовых пленок с лазерной перфорацией. В упаковке фруктов и овощей, Styrolux обеспечивает газо- и влагообмен с среда. Поэтому овощи, упакованные в пленку Styrolux, можно продолжать их естественный процесс созревания.Это впечатляюще демонстрируется простой эксперимент с зелеными помидорами, которые созревают за 10 дней в Styrolux мешки, в то время как помидоры, упакованные в полиэтилен, застаиваются в процессе созревания обрабатываются и остаются зелеными. Печатные пленки Styrolux толщиной 50 мкм становятся все более популярными. используется в термоусадочной упаковке и этикетках из-за их хорошего качества. значения усадки. В отличие от полиолефиновых этикеточных пленок, Styrolux пленки можно наклеивать с помощью обычных клеев. |
Styrolux можно перерабатывать на экструдерах, рассчитанных на нормальную высокую плотность полиэтилен (HDPE) или ПВХ. Низкие колебания пропускной способности, высокая пропускная способность скорость и низкая температура плавления могут быть достигнуты с помощью 12-канавки втулка нагрета до 80 град. В то время как в случае зон плавной подачи производительность экструдера зависит от температурного трения между твердым телом и цилиндром и между твердым телом и винтом, в случае рифленая зона подачи: трение определяется геометрией ствола стена.Испытания показали, что осевые прямоугольные канавки работают лучше, чем другие стандартные формы канавок. Канавки мешают вращению сплошной с винтом. Следовательно, рифленый экструдер может одновременно скорость вращения, транспортирует больше материала, чем обычный экструдер с гладкая втулка. Используемый нами шнек 60/25 D (выдавливание канавок) имеет небольшую глубину вылета. в секции подачи и секции смешивания с диском с глубокими пазами: Использование канавок позволяет повысить производительность вместе с меньшим расплавом температура. Однако, если доступны только гладкие стволы, мы рекомендуем винты, которые были проверены при экструзии плоской пленки из Styrolux и, например, в случае винта 60/25 D имеют следующую геометрию: |
В Температура плавления очень важна для получения качественной пленки. Таять следует избегать температуры выше 220 ° C любой ценой.Типичная обработка условия приведены в Таблице 10. |
Материал Styrolux марки 693 D, который подходит для экструзии пленки с раздувом, имеет более высокую прочность, чем 684 D. Мы рекомендуем 684 D для начала при экструзии пленки с раздувом благодаря более высокой стабильности расплава. Styrolux 693 D и 684 D можно смешивать с полистиролом общего назначения. и обработаны с образованием высокопрозрачных пленок.Снижение прозрачности Наблюдаемое для экструдированной пленки толщиной 1 мм можно не учитывать для тонких пленок, имеющих толщиной 10-100 мкм из-за малой толщины пленки. В добавление недорогого универсального ПС имеет экономические преимущества а также служит для целенаправленного изменения свойств. При увеличении жесткости, твердости и температуры тепловой деформации добавление полистирола общего назначения снижает ударную вязкость. Для большинства тонкопленочных работ, пропорции Styrolux от 70 до 100 процентов были признаны подходящими.Состав можно быстро оптимизировать путем пробного производства нескольких пленок разного состава, а затем тестирование их эксплуатационных свойств. Следует внимательно отнестись к выбору марки полистирола. Для экструзии пленки с раздувом мы рекомендуем высокотекучую марку 143 E (MVI 200/5 = 25), который очень легко смешивается с Styrolux из-за его хороших свойств. поток. Марки PS с меньшей текучестью, например PS 168 N, смешиваются в большом количестве менее легко, дает заметные структуры течения на поверхности пленки и непригодны для экструзии пленки с раздувом. |
Помимо соотношения смешивания Styrolux и полистирола общего назначения, и скорость взлета оказывают важное влияние на механические свойства пленки. Например, удлинение при разрыве и текучесть напряжение в продольном и поперечном направлениях увеличивается с увеличением коэффициент удара. Величины усадки, параллельные направлению экструзии, равны гораздо меньше зависит от увеличения степени продувки, чем усадка значения перпендикулярны направлению экструзии; последние быстро увеличиваются с увеличением мощности удара и приближаются к значению для продольного направление. Когда смеси Styrolux и полистирола общего назначения обрабатываются с постоянной коэффициент удара, усадка в поперечном направлении уменьшается по мере увеличения доли ПС общего назначения. |
Styrolux можно смешивать с полистиролом общего назначения, предпочтительно PS 143 E. Доля PS 143 E ограничена максимум 30 процентами, так как риск смятия при намотке пленки увеличивается с подъемом PS содержание.Если возникают проблемы с блокировкой, добавление 4% пакетной NB обычно предоставляет средство правовой защиты. ASE периодического действия следует использовать, если трение скольжения и чувствительность к царапинам быть уменьшенным. Перед выключением экструдера смесь ПС общего назначения и Batch CL всегда следует пропускать через него. Стиролюкс нельзя оставлять в горячий экструдер или штамп на длительный период. Сшитые частицы геля (пятнышки) указывают на термическое напряжение.Они возникают, если мертвые углы, длительное время пребывания или высокие температуры повредили продукт. В В таком случае экструдер необходимо очистить, как описано в разделе «Очистка экструдер ». |
POLYSTAR MACHINERY CO., LTD.
- Сумка-майка
- Сумка для покупок
- Мешок для мусора
- Сумка для супермаркетов
Выберите свою модель
Фотографии установки
Технические характеристики
Наименование модели | Экструдер для выдувной пленки HA |
Конечный продукт | Полиэтиленовая пленка HDPE, LDPE, LLDPE |
заявка | Гибкие упаковочные пакеты, сумка для футболки, мешок для мусора, сумка для покупок |
Используемый материал | HDPE, LDPE, LLDPE первичное сырье, переработанный материал, соединение CaCO3, биоразлагаемый материал, маточная смесь и добавки |
Выходной диапазон | 75 ~ 150 кг / час (зависит от размера экструдера) |
Слой пленки | Моно слой (один слой) |
Диаметр винта | 55, 65 мм (индивидуально) |
Винт L / D | 28 / 1,30 / 1,32 / 1 (индивидуально) |
Материал винта | SACM-465 |
Ширина | 500 ~ 1500 мм |
Толщина | 0.008 ~ 0,1 мм |
Дополнительные устройства | Автозагрузчик, система дозирования маточной смеси, ротационная высекальная головка, контроллер пузырьков, устройство для обработки коронным разрядом, валик для тиснения, автоматическая намотка, двойная намотка, контроллер положения кромки, контроллер натяжения |
Срок поставки | 60 ~ 120 дней |
Гарантия | 1 год |
Техническая помощь | Инженеры, обслуживающие технику за рубежом |
Простой в конструкции, производительный и гибкий экструдер для производства однослойной пленки с раздувом
Экструдер для производства однослойной пленки HA с раздувом является хорошим решением для общей упаковки и производит качественную пленку.Подходит для упаковки обычных продуктов, таких как сумки для футболок, сумки для супермаркетов, плоские пакеты и многие другие. Ширина пленки составляет от 800 мм до 2300 мм и может быть изменена в зависимости от требований заказчика, подходит как для пленки HDPE, так и для пленки LDPE. Специально разработанный экструдер для производства пленки с раздувом обладает хорошей способностью плавить и смешивать материал с маточной смесью / добавками.Высокоточная фильерная головка и кольцо охлаждающего воздуха обеспечивают хороший контроль толщины пленки и ее сопротивление.
HDPE
LDPE
Экструдер для выдувания пленки HA — это простая и универсальная машина, которая может производить HDPE или LDPE, просто заменяя головку фильеры и воздушное кольцо.Для однослойной пленки для ламинирования может быть добавлен двойной намоточный блок, ручной или автоматический.Доступны типы «спина к спине» или «сверху вниз» в зависимости от производственного помещения и компоновки заказчика.
Китай Производитель машины для выдувания пленки POF, Экструдер пленки POF, поставщик термоусадочной пленки POF
FOOD Machinery Co., Ltd. — высокотехнологичное складское предприятие, специализирующееся на производстве оборудования для пластмассы. В состав корпорации вошла мануфактура DEP.И торговый DEP., Расположенный в зоне развития новых и высоких технологий города Лайу. Лайу — это гигиенический город государственного уровня, красивый город, пересеченный автострадами Цзихуан. Bolai Tailai Laixin и др. Автострады все попадаются …
FOOD Machinery Co., Ltd. — высокотехнологичное складское предприятие, специализирующееся на производстве оборудования для пластмассы. В состав корпорации вошла мануфактура DEP. И торговый DEP., расположенный в зоне развития новых и высоких технологий города Лайу. Лайу — это гигиенический город государственного уровня, красивый город, пересеченный автострадами Цзихуан. Bolai Tailai Laixin и т. Д. Все автострады проходят через LAIWU. Гора Тай, известная в стране и за рубежом, находится в 50 км к западу от Лайу, Цюйфу, родина Конфуция, находится в 120 км к западу к югу от Лайу. Таким образом, прекрасные гуманитарные науки и природное окружение воспитывают в FOOD выдающиеся характеры.FOOD Machinery Co., Ltd. Положитесь на технические силы Пекинского химического университета, собрав десятки экспертов, которые занимаются производством пластмассовых машин более десяти лет, поэтому мы обладаем мощной технической мощью.В соответствии с корпоративным духом, который является гармоничным, эффективным и сдержанным, мы занимаемся исследованиями и разработкой новой пластиковой машины, и наши продукты получили множество патентов. Наша линейка продуктов: машина для выдувания термоусадочной пленки POF, полностью автоматическая машина для производства пленки POF, машина для производства пленки POF, машина для выдувания пленки из ПВХ, машина для выдувания термоусадочной пленки из ПВХ, машина для производства антикоррозийной ленты и т. система.
FOOD работает в строгом соответствии с системой качества ISO 9001, с усовершенствованным процессом и безупречным методом проверки.На конкурентном рынке только мы уверены: «У меня есть то, чего нет у вас, то, что у меня есть, превосходит другие, мы более продвинуты, если у вас есть качественная продукция», и адаптируемся к рыночному спросу, разрабатываем новое оборудование для производства пластмасс специального типа, смог закрепиться в беспроигрышной позиции навсегда.