Линия для производства композитной стеклопластиковой арматуры
Характеристики технологической Линии:
Производимые диаметры (мм) | 4-20 |
Производительность (п.м./минуту) | 16-2 |
Печь полимеризации, количество секций х длина (м) | 4 х 1,5 |
Габариты линии (ДxШxВ) м | 21,0х4,0х1,6 |
Вид нагрева | ТЭН |
Тип протягивающего устройства | Траковый |
Количество одновременно изготавливаемых изделий | 2 |
Тип связующего | Ангидрид |
Электропитание — трех фазный электрический ток напряжением 380 В, 50 Гц, установленная мощность – 28 кВт.
Время работы линии составляет 24 часа в сутки с одним техническим перерывом в один час для промывания и технического осмотра линии. Один раз в месяц должен проводиться капитальный технический осмотр линии. Необходимое количество человек в смену на 1 линию – 2-3 чел.
Основные узлы линии ЛИСА-2
Тип комплектации | ЛИСА-2 | ЛИСА-2М |
Описание комплектации линии | Кол-во шт. | |
Шпулярник, внутренней размотки нитей в сборе (на 60 бобин) | 3 | 4 |
Устройство сушки ровинга | 2 | 4 |
Ванна пропиточная | 2 | 4 |
Стол большой | 2 | 2 |
Обмотчик | 2 | 2 |
Стол малый | 2 | 2 |
Камера полимеризации 4-ч секционная с ИФК нагревателями | 1 | 1 |
Ванна охлаждения | 1 | 1 |
Устройство протягивающее траковое | 1 | 1 |
Устройство отрезное | 1 | |
Шкаф (на стойке) управления с контрольноизмерительной аппаратурой |
1 | 1 |
youtube.com/embed/vjQ-fpKvYQE» frameborder=»0″ allow=»accelerometer; autoplay; encrypted-media; gyroscope; picture-in-picture» allowfullscreen=»true»>
Общие сведения о технологии изготовления стеклопластиковой арматуры
Технологический процесс изготовления арматуры со спиральным периодическим профилем основан на формирования стержня арматуры, методом безфильерной протяжки «нидлтрузии». Стержень состоит из непрерывных стеклянных или базальтовых нитей, пропитанных полимерным связующим, на основе эпоксидной смолы. Рифленая поверхность арматуры создается за счет дополнительной спиральной обмотки стержня арматуры жгутом в процессе формирования стержня. Стеклянные или базальтовые нити (далее нити) являются силовым армирующим элементом, обеспечивающим прочностные характеристики арматуры, а полимерное связующее обеспечивает совместную работу нитей после отверждения.
Стеклопластиковая арматура предназначена для замены стальной арматуры и выпускается в виде стержней длиной до 12 метров.
Описание технологического процесса
Заданное количество стеклянных (базальтовых) нитей сматываются с бобин (внутренняя размотка), находящихся на шпулярнике и поступают в устройство пропитки, где равномерно пропитываются полимерным связующим. Пропитанные полимерным связующим нити по направляющим попадают в собирающую воронку и далее в нитеприемную втулку – определенного диаметра – для каждого типоразмера арматуры. Неотвержденные сформированные стержни с периодическим профилем попадают в туннельную печь, где при плавном нагревании (по заданной программе) до определенной температуры, происходит процесс полимеризации (отверждения) связующего. Выходя из печи, отвержденные стержни арматуры попадают в ванну с проточной водой для охлаждения. Протяжка стержней арматуры происходит с помощью тракового тянущего устройства. После тянущего устройства стержни арматуры попадают в узел автоматической отрезки, где отрезается на определенную длину (задается программой).
Требования к производственному помещению
- Температурный режим не ниже +18С, относительная влажность не более 85%
- Общая занимаемая площадь для одной линии — около 100 м. кв.
- Приточно-вытяжная вентиляция с 3-5 кратным воздухообменом
- Канал удаления дыма над печью и канал пылеудаления над узлом обмотчика.
- Перепад высот пола – не более 40 мм.
- Система внутреннего и наружного освещения
- Система подачи питьевой и технической воды
- Соответствие категории В класс П-Па и оснащение системой пожаротушения
- Кран-балка грузоподъемностью до 5 тонн, на участке погрузки на транспорт.
Виды технического обслуживания
- ЕТО – внешний осмотр всех узлов Линии, в основном, подшипников, электрических соединений, насосного узла, фильтра очистки воды, ремней приводных, очистка от попаданий смолы, стеклопыли при резке арматуры, особенно, электродвигателей.
- ТО – электродвигателей и электроприборов проводится согласно требованиям техдокументации. Один раз в месяц – проводится полный технический осмотр Линии. Замена отдельных быстро изнашиваемых деталей – не потребует больших затрат и времени.
В процессе работы от нагревателей происходит выделение газообразных продуктов, которые необходимо устранять с помощью местной вытяжной вентиляции.
При изготовлении арматуры используются основные материалы: ровинг, компоненты связующих на основе эпоксидо-диановых смол. Возможна помощь в организации поставок необходимого сырья для производства арматуры.
Линия поставляется с документацией — паспорт, инструкция по эксплуатации.
Оказываем поддержку по техническому сопровождению и в отработке производственных процессов изготовления арматуры.
Гарантийный срок эксплуатации Линии – 12 месяцев, за исключением покупных комплектующих.
Технологический регламент на производство стеклопластиковой арматуры на Линии ЛИСА-2 (2-х ручьевая)
Арматура | Ровинг 4800 | Ровинг 9600 | Ванна пропиточная | Шпулярник | Производи- тельность линии | |
Диаметр (мм) | Кол-во бобин на 2 ручья | Кол-во шт.![]() |
кол-во п.м./мин | |||
4 | 18 | — | — | 2 | 2 | 16 |
6 | 24 | — | — | 2 | 2 | 10 |
8 | 48 | — | — | 2 | 2 | 6 |
10 | 82 | 42 | — | 2 | 2 | 6 |
12 | 112 | 62 | — | 2 | 5 | |
14 | 180 | 90 | 48 | 2 | 4/2/2 | 5 |
16 | 232 | 118 | 58 | 4/2 | 4/2/2 | 4 |
18 | — | 158 | 78 | 4/2 | 4/2 | 4 |
20 | — | 202 | 102 | 4/2 | 4/2 | 4 |
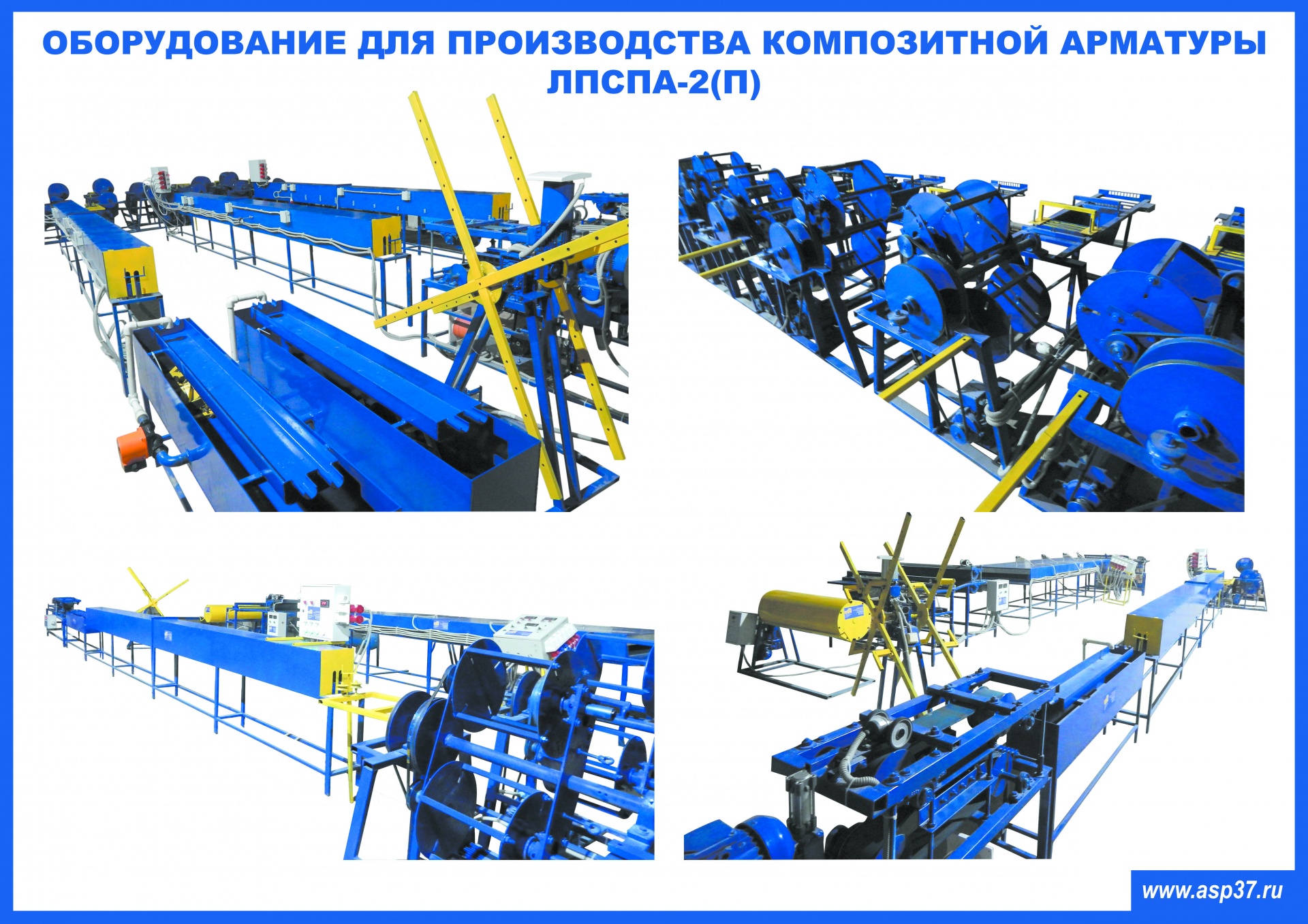
| |||||
| |||||
| |||||
| |||||
| |||||
Станки для производства арматуры и сетки
Станки для производства композитной арматуры и сетки
Компания “Армбазальт” также предлагает оборудование для производства композитной арматуры и сетки.
Основные сведения об оборудовании
— Потребление электроэнергии, кВт/ч: от 3.5 до 8.0, в зависимости от производительности;
— Электропитание: 3-х фазный электрический ток напряжением 380В;
— Количество одновременно выпускаемых прутков арматуры, шт.: 1 или 2;
— Выпускаемые диаметры, мм: от 4 до 32.
— Производительность, м/мин: до 12;
— Размеры линии, м: длина 18, ширина 0.6, высота 1.6.
Станок предназначен для работы в отапливаемых помещениях при температуре воздуха от 16°C.
Один раз в месяц должен проводиться капитальный технический контроль производственной линии согласно регламенту.
Наименование оборудования и его комплектующих |
Кол-во(ед) |
Шпулярник внутренней размотки нитей ровинга |
1 |
Устройство подогрева нитей |
1 |
Ванна для пропитки нитей |
1 |
Устройство формирования профиля и скручивание нитей |
1 или 2 |
Модуль подготовки нити |
1 |
Бухтонамотчик двойной намотки |
1 |
Печь тоннельная неметаллическая |
1 |
Ванна водяного охлаждения |
1 |
Стенд протяжки профиля гусеничного типа |
1 |
Отрезной механизм |
1 |
Шкаф управления |
1 |
Эксплуатационная документация: — Паспорт линии — Руководство по эксплуатации — Технологическая карта
|
1 |
Наука и технология композиционных материалов
Послушайте эту тему
В таком развитом обществе, как наше, все мы зависим от композитных материалов в некоторых аспектах нашей жизни. Стекловолокно был разработан в конце 1940-х годов и был первым современным композитом. Он по-прежнему самый распространенный, составляя около 65 процентов всех производимых сегодня композитов. Он используется для изготовления корпусов лодок, досок для серфинга, спортивных товаров, облицовки бассейнов, строительных панелей и кузовов автомобилей.Вы вполне можете использовать что-то из стекловолокна, даже не подозревая об этом.
Что делает материал композитным
Композиционные материалы образуются путем объединения двух или более материалов, которые имеют совершенно разные свойства. Различные материалы работают вместе, чтобы придать композиту уникальные свойства, но внутри композита вы можете легко отличить разные материалы друг от друга — они не растворяются и не смешиваются друг с другом.
Композиты существуют в природе. Кусок дерева представляет собой композит, состоящий из длинных волокон целлюлозы (очень сложной формы крахмала), удерживаемых вместе гораздо более слабым веществом, называемым лигнином. Целлюлоза также содержится в хлопке и льне, но именно связующая сила лигнина делает кусок древесины намного прочнее, чем пучок хлопковых волокон.
Идея не нова
Люди использовали композитные материалы на протяжении тысячелетий. Возьмем, к примеру, сырцовые кирпичи.Если вы попытаетесь согнуть лепешку из засохшей грязи, она легко сломается, но она окажется крепкой, если вы попытаетесь раздавить или сжать ее. Кусок соломы, с другой стороны, обладает большой силой, когда вы пытаетесь ее растянуть, но почти не имеет силы, когда вы ее сминаете. Когда вы объединяете грязь и солому в блок, свойства двух материалов также объединяются, и вы получаете кирпич, который прочен как на сжатие, так и на разрыв или изгиб. Говоря более технически, у него есть и хорошие
прочность на сжатие и хорошо
предел прочности .
Еще один известный композит — бетон. Здесь заполнитель (мелкие камни или гравий) скреплен цементом. Бетон имеет хорошую прочность при сжатии, и его можно сделать более прочным при растяжении, добавив в композит металлические стержни, проволоку, сетку или тросы (таким образом создавая железобетон).
Композиты были сделаны из формы углерода, называемой графеном, в сочетании с металлической медью, в результате чего был получен материал, в 500 раз более прочный, чем сама медь. Точно так же композит графена и никеля имеет прочность, более чем в 180 раз превышающую прочность никеля.
Что касается стекловолокна, то он сделан из
пластик армированный нитями или стекловолокном. Эти нити можно либо связать вместе и сплести в мат, либо их иногда можно разрезать на короткие отрезки, которые произвольно ориентированы в пластиковой матрице.
Больше чем сила
В настоящее время многие композиты производятся не только для улучшения прочности или других механических свойств, но и для других целей. Многие композиты предназначены для того, чтобы быть хорошими проводниками или изоляторами тепла или иметь определенные магнитные свойства; свойства, которые очень специфичны и специализированы, но также очень важны и полезны. Эти композиты используются в огромном количестве электрических устройств, включая транзисторы, солнечные элементы, датчики, детекторы, диоды и лазеры, а также для изготовления антикоррозионных и антистатических покрытий на поверхности.
Композиты, изготовленные из оксидов металлов, также могут иметь определенные электрические свойства и используются для производства кремниевых чипов, которые могут быть меньше и плотнее упакованы в компьютер. Это увеличивает объем памяти и скорость компьютера. Оксидные композиты также используются для создания высокотемпературных сверхпроводящих свойств, которые теперь используются в электрических кабелях.
Изготовление композита
Большинство композитов состоит всего из двух материалов.Один материал (матрица или связующее) окружает и связывает скопление волокон или фрагменты гораздо более прочного материала (армирования). В случае глиняных кирпичей две роли берут на себя грязь и солома; в бетоне — цементом и заполнителем; в дереве целлюлозой и лигнином. В стекловолокне армирование обеспечивается тонкими нитями или стекловолокном, часто вплетенными в нечто вроде ткани, а матрица представляет собой пластик.
Примеры различных форм армирования стекловолокном, которые будут использоваться при создании стекловолокна.Источник изображения: Cjp24 / Wikimedia Commons. Стекловолоконные нитки из стекловолокна очень прочные при растяжении, но они также хрупкие и ломаются при резком сгибании. Матрица не только удерживает волокна вместе, но и защищает их от повреждений, разделяя любые
стресс из их. Матрица достаточно мягкая, чтобы ее можно было придать инструментам, и ее можно размягчить подходящими растворителями, чтобы можно было произвести ремонт. Любая деформация листа стекловолокна обязательно растягивает часть стекловолокна, и они способны этому противостоять, поэтому даже тонкий лист очень прочен.Кроме того, он довольно легкий, что является преимуществом для многих приложений.
За последние десятилетия было разработано много новых композитов, некоторые из которых обладают очень ценными свойствами. Тщательно выбирая арматуру, матрицу и производственный процесс, объединяющий их, инженеры могут адаптировать свойства к конкретным требованиям. Они могут, например, сделать композитный лист очень прочным в одном направлении, выравнивая волокна таким образом, но более слабым в другом направлении, где прочность не так важна.Они также могут выбирать такие свойства, как устойчивость к теплу, химическим веществам и атмосферным воздействиям, выбирая подходящий матричный материал.
Выбор материалов для матрицы
В качестве матрицы во многих современных композитах используются термореактивные или термопластичные пластмассы (также называемые смолами). (Использование пластика в матрице объясняет название «армированный пластик», которое обычно дают композитам). Пластмассы
полимеры которые удерживают арматуру вместе и помогают определить физические свойства конечного продукта.
Термореактивные пластмассы являются жидкими при приготовлении, но затвердевают и становятся твердыми (т. Е. Затвердевают) при нагревании. Процесс схватывания необратим, поэтому эти материалы не становятся мягкими при высоких температурах. Эти пластмассы также устойчивы к износу и воздействию химикатов, что делает их очень прочными даже в экстремальных условиях окружающей среды.
Термопласты, как следует из названия, твердые при низких температурах, но размягчаются при нагревании. Хотя они используются реже, чем термореактивные пластмассы, они обладают некоторыми преимуществами, такими как более высокая вязкость разрушения, длительный срок хранения сырья, способность к переработке и более чистое и безопасное рабочее место, поскольку для процесса отверждения не требуются органические растворители.
Керамика, углерод и металлы используются в качестве матрицы для некоторых узкоспециализированных целей. Например, керамика используется, когда материал будет подвергаться воздействию высоких температур (например, теплообменники), а углерод используется для продуктов, которые подвергаются трению и износу (например, подшипники и шестерни).
Изображение под электронным микроскопом в искусственных цветах композита с магниевой матрицей, армированного карбидом титана-алюминия. Источник изображения: ZEISS Microscopy / Flickr.Выбор материалов для армирования
Хотя стекловолокно является наиболее распространенным армированием, во многих современных композитах сейчас используются тонкие волокна из чистого углерода.Можно использовать два основных типа углерода — графит и углеродные нанотрубки. Оба являются чистым углеродом, но атомы углерода расположены в разных кристаллических конфигурациях. Графит — очень мягкое вещество (используется в «свинцовых карандашах») и состоит из листов атомов углерода, расположенных в виде шестиугольников. Связи, удерживающие шестиугольники вместе, очень прочные, но связи, удерживающие вместе листы шестиугольников, довольно слабые, что и делает графит мягким. Углеродные нанотрубки изготавливаются путем скатывания одного листа графита (известного как графен) в трубку.Это создает чрезвычайно прочную структуру. Также возможно изготовление трубок из нескольких цилиндров — трубок внутри трубок.
Композиты из углеродного волокна легки и намного прочнее, чем стекловолокно, но при этом более дороги. Из этих двух графитовые волокна дешевле и их легче производить, чем углеродные нанотрубки. Они используются в конструкциях самолетов и в высокопроизводительном спортивном оборудовании, таком как клюшки для гольфа, теннисные ракетки и гребные лодки, и все чаще используются вместо металлов для ремонта или замены поврежденных костей.
Нити бора даже прочнее (и дороже) углеродных волокон. Нанотрубки из нитрида бора обладают дополнительным преимуществом, поскольку они намного более устойчивы к нагреванию, чем углеродные волокна. Они также обладают пьезоэлектрическими качествами, что означает, что они могут генерировать электричество при приложении к ним физического давления, например, при скручивании или растяжении.
Полимеры также могут использоваться в качестве армирующего материала в композитах. Например, кевлар, первоначально разработанный для замены стали в радиальных шинах, но наиболее известный благодаря использованию в пуленепробиваемых жилетах и шлемах, представляет собой чрезвычайно прочное полимерное волокно, придающее прочности композитному материалу.Он используется в качестве арматуры в композитных изделиях, которые требуют легкой и надежной конструкции (например, структурные части корпуса самолета). Еще более прочным, чем кевлар, является вещество, состоящее из комбинации графена и углеродных нанотрубок.
Выбор производственного процесса
Для изготовления объекта из композитного материала обычно используется какая-либо форма. Армирующий материал сначала помещается в форму, а затем полужидкий матричный материал распыляется или закачивается для формирования объекта.Можно приложить давление, чтобы вытеснить пузырьки воздуха, а затем форму нагревают, чтобы матрица затвердела.
Процесс формования часто выполняется вручную, но автоматическая обработка становится все более распространенной. Один из этих методов называется пултрузия (термин, образованный от слов «вытягивание» и «экструзия»). Этот процесс идеально подходит для производства прямых изделий с постоянным поперечным сечением, например мостовых балок.
Во многих тонких структурах сложной формы, таких как изогнутые панели, композитная структура создается путем наложения листов тканого армирующего волокна, пропитанного пластиковым матричным материалом, поверх базовой формы соответствующей формы.Когда панель будет достигнута подходящей толщины, матричный материал отверждается.
Сэндвич-композиты
Многие новые типы композитов создаются не с помощью матрицы и метода армирования, а путем укладки нескольких слоев материала. Структура многих композитов (например, тех, которые используются в панелях крыла и корпуса самолетов) состоит из пластиковых сот, зажатых между двумя обшивками из композитного материала, армированного углеродным волокном.
Эти многослойные композитные материалы сочетают в себе высокую прочность и, в частности, жесткость на изгиб и малый вес. Другие методы включают в себя простую укладку нескольких чередующихся слоев разных веществ (например, графена и металла) для создания композита.
Зачем использовать композиты?
Самым большим преимуществом композитных материалов является прочность и жесткость в сочетании с легкостью.Выбирая подходящую комбинацию армирования и материала матрицы, производители могут создавать свойства, которые точно соответствуют требованиям для конкретной конструкции для конкретной цели.
- Композиты в Австралии
Австралия, как и все развитые страны, проявляет большой интерес к композитным материалам, которые многие люди считают «материалами будущего».
Основная задача — снизить затраты, чтобы композитные материалы можно было использовать в продуктах и приложениях, которые в настоящее время не оправдывают затрат.В то же время исследователи хотят улучшить характеристики композитов, например сделать их более устойчивыми к ударам.
Одна из новых технологий включает «текстильные композиты». Вместо того, чтобы укладывать армирующие волокна по отдельности, что является медленным и дорогостоящим процессом, их можно связать или сплести вместе, чтобы получить своего рода ткань. Он может быть даже трехмерным, а не плоским. Пространства между текстильными волокнами и вокруг них затем заполняются матричным материалом (например, смолой) для изготовления продукта.
Этот процесс довольно легко может быть выполнен машинами, а не вручную, что делает его быстрее и дешевле. Соединение всех волокон вместе также означает, что композит с меньшей вероятностью будет поврежден при ударе.
По мере того, как стоимость снижается, другие применения композитов начинают выглядеть привлекательными.
При изготовлении корпусов и надстроек лодок из композитов используется их устойчивость к коррозии. У минных охотников ВМС Австралии композитный корпус, поскольку магнитный эффект стального корпуса может помешать обнаружению мин.
Также в разработке находятся вагоны для поездов, трамваев и других средств передвижения, сделанные из композитных материалов, а не из стали или алюминия. Здесь привлекательность заключается в легкости композитов, поскольку в этом случае автомобили потребляют меньше энергии. По той же причине в будущем мы увидим все больше и больше композитов в автомобилях.
Современная авиация, как военная, так и гражданская, является ярким примером. Без композитов было бы гораздо менее эффективно. Фактически, требования, предъявляемые этой отраслью к легким и прочным материалам, были основной движущей силой развития композитов.Сейчас обычным явлением являются крылья и хвостовое оперение, гребные винты и лопасти несущего винта, сделанные из современных композитных материалов, а также большая часть внутренней конструкции и деталей. Каркасы некоторых небольших самолетов полностью сделаны из композитных материалов, как и крыло, хвостовое оперение и панели корпуса больших коммерческих самолетов.
Размышляя о самолетах, стоит помнить, что композиты с меньшей вероятностью, чем металлы (например, алюминий), полностью разрушатся под действием нагрузки. Небольшая трещина в куске металла может очень быстро распространиться с очень серьезными последствиями (особенно в случае самолета).Волокна в композите блокируют расширение любой небольшой трещины и распределяют напряжение вокруг нее.
Правильные композиты также хорошо выдерживают нагрев и коррозию. Это делает их идеальными для использования в продуктах, работающих в экстремальных условиях, таких как лодки, оборудование для обработки химикатов и космические корабли. В целом композитные материалы очень прочные.
Еще одно преимущество композитных материалов состоит в том, что они обеспечивают гибкость конструкции. Из композитов можно придавать сложные формы, что является отличным преимуществом при производстве чего-то вроде доски для серфинга или корпуса лодки.
Кроме того, в настоящее время большая работа направлена на разработку композитных материалов, изготовленных из отходов, таких как сельскохозяйственные отходы, строительные материалы или пластиковые контейнеры для напитков.
Обратной стороной композитов обычно является их стоимость. Хотя при использовании композитов производственные процессы часто бывают более эффективными, сырье стоит дорого. Композиты никогда полностью не заменят традиционные материалы, такие как сталь, но во многих случаях это именно то, что нам нужно.И без сомнения, по мере развития технологии будут найдены новые применения. Мы еще не видели всего, на что способны композиты.
Современная авиация была основным двигателем развития композитов. Источник изображения: Пол Нелхэмс / Flickr.Автоматическая резка композитной арматуры экономит время и материал, повышает качество
Несмотря на стремительный технологический прогресс в производстве деталей из композитов, многие производители композитов до сих пор режут армирующие материалы вручную.В то время как использование автоматизированной резки материалов растет, многие производители могут извлечь выгоду из принятия этой эффективной и рентабельной технологии.
Автоматическая резка уже стала стандартом для аэрокосмической и морской промышленности. Почему? Потому что новейшие технологии могут значительно сократить отходы материалов, устранить ненужный труд и улучшить качество. Это также увеличит пропускную способность. Если вы еще не используете автоматическую резку, сейчас самое время пересмотреть свои процессы резки и посмотреть, что эта технология может сделать для вашего бизнеса.
Eastman Machine Company (Буффало, штат Нью-Йорк) работает в тандеме с промышленными инженерами над проектированием, производством и настройкой станков для резки композитных материалов, подходящих для широкого круга отраслей, использующих стекловолокно, углеродное волокно и арамид в сухих формах и формах препрега. Эта американская компания находится в семейном владении и управляется на протяжении пяти поколений и занимается производством режущего оборудования более 130 лет. Таким образом, они хорошо разбираются в том, что автоматическая резка может сделать для изготовителя композитов и как лучше всего ее применять.Подробнее о преимуществах автоматизированной резки от Eastman и о том, как она применяется в известной судостроительной компании Maverick Boat Group.
Преимущества автоматической резки
Есть четыре основные причины для внедрения автоматизированной резки: сокращение трудозатрат, улучшенное использование материала, повышенное качество и гораздо лучшая эффективность и гибкость.
В этом коротком видео показано, как конвейерная система резки работает с обычными армирующими материалами для морской промышленности.
Снижение трудозатрат — Машинная резка намного быстрее и точнее, чем ручная резка, даже на станке со статическим столом, где оператор вручную позиционирует обрабатываемый материал. Конвейерные системы автоматически загружают и распределяют материал. Эти системы требуют минимального труда для эксплуатации и могут переключаться с одной работы на другую за несколько минут.
Благодаря сочетанию неизменно точной производительности раскроя и программного обеспечения для раскроя, которое позволяет создавать выкройки наиболее эффективным способом, автоматическая раскройка может значительно улучшить использование материала.Здесь показано программное обеспечение для оперативного управления cutPRO от Eastman.
Улучшенное использование материала — Благодаря своей точности и повторяемости автоматические резаки сокращают количество ошибок и отходов, характерных для ручной резки. Кроме того, доступно простое в использовании программное обеспечение для раскроя, которое автоматически распределяет формы шаблона в наиболее экономичном для материала размере в зависимости от размера разрезаемого материала. В совокупности эти факторы могут сократить отходы материала на целых 25% .
Качество — Автоматические резаки чрезвычайно точны, что обеспечивает более стабильное качество конечного формованного продукта. Это приобретает первостепенное значение по мере увеличения сложности деталей.
Эффективность ведет к гибкости — Высокая скорость автоматической резки увеличивает производительность, а резка может происходить намного ближе к времени простоя или даже одновременно в некоторых случаях. Это обеспечивает большую гибкость планирования. Это также может уменьшить порчу материалов, которые требуют охлаждения и имеют ограниченный срок хранения при комнатной температуре.
Компьютерное управление машиной обеспечивает быструю и точную резку и позволяет быстро переключаться с одного задания на другое.
Некоторые из этих факторов трудно предсказать или измерить при анализе рентабельности инвестиций в автоматизированную резку. Компания Eastman предлагает бесплатные оценки тестовой резки с использованием ваших материалов и шаблонов и / или файлов для резки, чтобы определить скорость машины, эффективность использования материала и рекомендуемую конфигурацию до вложения средств. Эта дополнительная услуга с подробными отзывами и дополнительными видеоматериалами рекомендуемого процесса сыграет важную роль в ваших расчетах рентабельности инвестиций.
Располагая этой информацией, производитель может теперь оценить некоторые реальные цифры ценностного предложения более автоматизированной резки по сравнению с существующими процессами и с высокой уверенностью в том, что обещанные результаты ваших инвестиций реальны.
Автоматизация резки в Maverick Boat Group
Maverick производит 30 моделей, от 16-дюймовых лодок до 35-дюймовых моделей с центральной консолью
.Maverick Boat Group — известный производитель, расположенный в Форт-Пирс, Флорида.У них есть четыре линии, продаваемые под торговыми марками Cobia, Pathfinder, Maverick и Hewes. В общей сложности Maverick производит 30 моделей на двух заводах, начиная от 16-футовых лодок и заканчивая моделями с центральной консолью 35 футов, предназначенными для использования в открытом море. В дополнение к традиционному наложению композита в открытых формах, Maverick использует технологию VARIS (система вакуумной инфузии смолы) почти на всех своих крупных изделиях и предпринимает попытки использовать Light RTM для мелких деталей.
Джереми Тессье (Jeremy Tessier), руководитель инженерного проекта / инженер по ламинированию, наблюдает за операцией резки в Maverick.Обладая более чем 25-летним опытом строительства лодок, последние 7 лет в Maverick, он хорошо разбирается в технологии резки. Он говорит, что эффективность резки и универсальность критически важны для бережливого производства Maverick. Они строят лодки в среднем менее чем за 8 дней и не полагаются на большой запас деталей или материалов для ускорения процесса сборки. Обычно они режут и комплектуют армирующие материалы незадолго до начала процесса формования, и резка должна быть быстрой и надежной.В основном они режут стекло E, но также используют углеродное волокно и кевлар в некоторых продуктах, а иногда и материалы сердцевины толщиной ¼ дюйма. Maverick начал со станка для резки со статическим столом еще в 2007 году. Пять лет назад они инвестировали в более автоматизированное решение — конвейерную систему резки Eastman Eagle C125 и купили еще одну, когда открыли новый завод в прошлом году.
В станках Eastman используется многоосевая портальная система с компьютерным управлением, которая перемещает режущую головку над столом со скоростью до 60 дюймов в секунду.Стол состоит из конвейерной системы, также находящейся под управлением компьютера, которая может непрерывно подавать материал, чтобы обеспечить непрерывную резку множества деталей и больших кусков любой длины. Формы раскроя сохраняются в цифровом виде в системе управления станком, которая определяет траекторию резака и конвейерную подачу каждой детали.
Maverick использует технологию VARIS (система вакуумной инфузии смолы) почти на всех своих крупных изделиях и предпринимает попытки использовать Light RTM для мелких деталей. Фото: Maverick Boat Group.Для некоторых компаний самой сложной частью перехода к такой автоматизации резки является изучение CAD и преобразование своих старых бумажных шаблонов в цифровые файлы. Maverick продвинулся дальше в САПР, когда перешел на более сложные машины, но Тессье говорит, что им действительно пришлось повысить свои навыки, чтобы делать такие вещи, как создание 3D-модели контурного корпуса или борта лодки, а затем ее выравнивание, чтобы получить 2D-шаблоны, которые нужно вырезать для армирования.
Теперь вся резка выполняется на станках Eastman без ручной резки.Это большая приверженность автоматизации, но Тессье говорит, что преимущества того стоят. Для Maverick наиболее важными преимуществами являются скорость резки и экономия материала. Что касается скорости, Maverick работает точно в срок, когда это возможно, чтобы поддерживать низкие запасы материалов и незавершенного производства. Возможность резать и комплектовать арматуру незадолго до формования является важным компонентом реализации этой стратегии. Более того, Тессье говорит, что график сборки Maverick может меняться ежедневно, а возможность сокращения времени сокращения дает им гибкость в выполнении этих изменений без ущерба для качества или эффективности.«Если вы хотите перенести другую модель в график на следующий день, вы можете переключиться на другой набор моделей подкрепления одним нажатием кнопки», — говорит он.
Maverick уделяет пристальное внимание всем расходам на материалы, и на арматурные материалы приходится большая часть из них. Тессье говорит, что по его опыту экономия материала при автоматической резке составляет около 25 процентов, что является большим числом, если сложить ее в течение года. Они также используют программное обеспечение для управленческой отчетности, которое генерирует система резки, чтобы точно знать, сколько материала используется и утилизируется для данного продукта, чтобы помочь с запасами и управлением затратами.
Поскольку детали Maverick очень большие, для них не так важна точность раскроя, как возможность быстро и многократно вырезать очень большие узоры. Они обычно вырезают выкройки размером до 72 на 60 дюймов, но могут доходить до сотен дюймов в длину, например, для усиления днища корпуса или деталей, которые охватывают весь борт лодки.
Более пристальный взгляд на автоматизированную технологию резки
Стандартная инструментальная головкаEastman включает в себя две разные инструментальные станции, включая использование поворотных лезвий, ножа для перфорации, перфоратора и маркера.
Хотя производитель масштаба Maverick, безусловно, выигрывает от автоматизированной резки, подходит ли это всем? По мнению Eastman, к лучшим кейсам относятся магазины, работающие в таких условиях:
- Два или более сотрудников занимаются раскройкой вручную
- Многочисленные материалы и типы узоров
- Узкие места в раскройном
- Высокий процент брака из-за человеческой ошибки или плохого ручного раскроя
Что касается того, какое оборудование искать, если вы режете много стекловолокна, например, Maverick, есть определенные возможности режущей системы, которые приведут к лучшей и более надежной работе.
10-стороннее лезвиеEastman предназначено для легкого разрезания современных тканей, таких как прошитое стекловолокно, при максимальной универсальности и адаптируемости.
Инструмент — Инструмент означает режущий блок на станке, который включает в себя головку инструмента и сменные режущие лезвия или другие инструменты. Maverick использует инструментальную головку Eastman Heavy Duty, которая приводится в действие собственным бесщеточным серводвигателем и независимо регулируемой подачей воздуха. Он имеет два режущих шпинделя, каждый с соединением шпинделя, изолирующим вращение инструмента.Это позволяет в головке инструмента включать два разных шпинделя с вращающимися лезвиями, ножами с перетаскиванием, перфорационными инструментами и маркером. Универсальная инструментальная головка увеличивает гибкость производства и сводит к минимуму время простоя, связанного с изменением конфигурации инструмента.
Есть множество ножей на выбор. Eastman рекомендует резать стекловолокно круглым или 10-гранным лезвием. Воздействие на лезвие и давление будут варьироваться в зависимости от переплетения, плотности и толщины материала.
Конвейерные системыобеспечивают непрерывную подачу и отрезку деталей любой длины.
Конвейерные системы — Конвейерная система Eagle с непрерывной подачей исключает необходимость ручного распределения и укладки материала. Вакуумная система захватывает материал через перфорированную уретановую режущую ленту. Это режущая поверхность для системы, а также то, что продвигает материал вперед. Оператору нужно только запустить материал на столе и включить вакуум; оттуда система сама распределяет материал. Материал непрерывно перемещается во время резки, и оператор удаляет обрезанные части, когда они уходят с другого конца.По сути, это «экономичный» вариант непрерывной резки и производства деталей прямо из рулонного материала. Куски стекловолокна с одинарным или низким слоем любой длины можно разрезать на высокой скорости в течение нескольких часов для получения больших объемов продукции.
Система струйной маркировки JetPRO®.
Печать по требованию — Возможность автоматической маркировки или печати на отрезанной детали очень полезна для идентификации деталей, что важно для надежной комплектации. Компания Eastman подходит к этому двумя способами с помощью портальных устройств.EasiMark® — это система маркировки аэрографом, доступная в перманентных и смываемых чернилах. Струйная система JetPRO® — это капельный принтер по требованию (DOD), который позволяет печатать символы на полной скорости с использованием цвета чернил и формул, доступных для большинства поверхностей.
Больше автоматизации для больших объемов и специальных требований
Дополнительная автоматизация может быть легко оправдана для сред с большим объемом. Производительность конвейерной машины для резки может составлять примерно от полутонны стекловолокна в час с однослойным материалом — включая загрузку материала, маркировку и сбор отрезанных деталей — до 1.8 тонн на четырехслойной. Это много материала, который нужно загружать и выгружать вручную. Когда машины работают на пределе своих возможностей в течение продолжительных периодов времени или в обстоятельствах, когда большой размер разрезаемых деталей представляет проблемы с эффективностью или качеством, доступно периферийное оборудование, которое требует еще больше трудозатрат в процессе резки.
Системы подачи с приводом автоматически регулируют и поддерживают постоянное натяжение для любого типа материала.
Системы подачи — Системы подачи с приводом автоматически регулируют и поддерживают постоянное натяжение для любого типа материала.Опциональный фотоэлектрический блок управления кромкой обеспечивает точное выравнивание каждого слоя. Доступный в различных конфигурациях для разной ширины и веса, этот тип механизированной системы подачи непрерывно подает материал на длину маркера или до тех пор, пока рулон не будет израсходован.
Намотчики — Узлы намотки работают синхронно с конвейерной режущей системой, скатывая длинные отрезанные детали. Отходы продолжают двигаться по системе или сбрасываться в сборный бункер. Намотчики особенно полезны, когда отрезанные детали, такие как длинные секции лопастей турбины, превышают длину стола, и операторам становится сложно собирать их вручную из-за высокой скорости резки. На этой анимации показаны некоторые виды автоматизации, доступные для конвейерных режущих машин Eastman.
Важность надежности
Как только производитель композитов интегрирует автоматическую резку в свои рабочие процессы, надежность оборудования становится первостепенной. С таким производительным и незапланированным простоем оборудование может быть чрезвычайно дорогостоящим и разрушительным. Наличие оборудования, которое может работать непрерывно без поломок, имеет решающее значение.
Eastman гордится надежностью своего оборудования и качеством обслуживания клиентов, и Тессиер из Maverick соглашается.Оборудование Eastman рассчитано на надежную работу в суровых условиях или в среде с высоким содержанием твердых частиц. Все оборудование производится в штаб-квартире Eastman в Буффало, штат Нью-Йорк, где также ведется склад запасных частей. Квалифицированные специалисты по обслуживанию доступны круглосуточно и без выходных.
Хотя внедрение более высоких форм автоматизации может быть проблемой, если вы режете или тратите впустую много материала, пришло время по-новому взглянуть на технологию автоматизированной резки. Автоматизация снизит ваши затраты на рабочую силу, улучшит использование материала и приведет к неизменно более высокому качеству резки.Это вариант, который нельзя игнорировать.
Для получения дополнительной информации о режущих системах Eastman перейдите сюда.
Как производить детали из углеродного волокна
Композитные материалы, такие как пластмассы, армированные углеродным волокном, являются универсальными и эффективными материалами, стимулирующими инновации на различных рынках от аэрокосмической до здравоохранения. Они превосходят традиционные материалы, такие как сталь, алюминий, дерево или пластик, и позволяют изготавливать высокопроизводительные легкие изделия.
В этом руководстве вы узнаете основы производства деталей из углеродного волокна, включая различные методы и способы использования 3D-печати для снижения затрат и экономии времени.
Информационный документЗагрузите этот информационный документ с рекомендациями по проектированию композитных форм и пошаговыми инструкциями по методам препрега и ручного ламинирования для создания деталей из углеродного волокна.
Загрузить информационный документКомпозитный материал — это комбинация двух или более компонентов, характеристики которых отличаются от этих отдельных компонентов сами по себе.Инженерные свойства обычно улучшаются, такие как добавленная прочность, эффективность или долговечность. Композиты состоят из армирования — волокна или частицы — удерживаемого вместе матрицей (полимером, металлом или керамикой).
Армированные волокном полимеры (FRP) доминируют на рынке и способствуют росту новых применений в различных отраслях промышленности. Среди них углеродное волокно — широко используемый композит, в частности, для самолетов, гоночных автомобилей и велосипедов, поскольку он более чем в три раза прочнее и жестче, чем алюминий, но на 40% легче.Он состоит из армированного углеродного волокна, соединенного с эпоксидной смолой.
Волокна могут быть сплетены однонаправленно и стратегически выровнены для создания прочности по отношению к вектору. Перекрестно переплетенные волокна можно использовать для создания прочности в нескольких векторах, и они также отвечают за фирменный стеганый вид композитных деталей. Обычно детали производятся с их комбинацией. Доступно несколько типов волокон, в том числе:
Стекловолокно | Углеродное волокно | Арамидное волокно (кевлар) |
---|---|---|
Самое популярное волокно Легкое, умеренное растяжение и прочность на сжатие Низкая стоимость и простота для работы с | Самое высокое соотношение прочности и жесткости к весу в отрасли (предел прочности на растяжение, сжатие и изгиб) Дороже, чем другие волокна | Более высокая стойкость к ударам и истиранию, чем у углеродного волокна Низкая прочность на сжатие Трудно резать или обрабатывать |
Смола используется для удержания этих волокон вместе и создания жесткого композита.Хотя можно использовать сотни типов смол, вот самые популярные из них:
Смола | Плюсы | Минусы | Отверждение |
---|---|---|---|
Эпоксидная смола | Максимальная прочность Самая длинная полка срок службы | Самый дорогой Чувствителен к соотношению компонентов смеси и колебаниям температуры | Использует специальный отвердитель (двухкомпонентная система) Некоторые эпоксидные смолы требуют тепла |
Полиэстер | Простой в использовании (самый популярный) Устойчивый к ультрафиолетовому излучению Самая низкая стоимость | Низкая прочность и коррозионная стойкость | Отверждается с катализатором (MEKP) |
Сложный виниловый эфир | Сочетает в себе характеристики эпоксидной смолы и стоимость полиэфира Лучшая устойчивость к коррозии, температуре и удлинению | Прочность ниже, чем у эпоксидной смолы и стоимость выше, чем у полиэстера Ограниченный срок хранения | Отверждается с катализатором (МЕКП) 9 0272 |
Производство армированных волокном полимеров, таких как детали из углеродного волокна, является умелым и трудоемким процессом, используемым как в единичном, так и в серийном производстве.Время цикла составляет от одного часа до 150 часов в зависимости от размера и сложности детали. Как правило, при производстве стеклопластика непрерывные прямые волокна соединяются в матрице с образованием отдельных слоев, которые накладываются слой за слоем на конечную деталь.
Свойства композита определяются как материалами, так и процессом ламинирования: способ включения волокон сильно влияет на характеристики детали. Термореактивным смолам придают форму вместе с арматурой в инструменте или форме и отверждают, чтобы получить прочный продукт.Доступны различные методы ламинирования, которые можно разделить на три основных типа:
При мокрой укладке волокно разрезается и укладывается в форму, затем смола наносится с помощью кисти, валика или пистолета-распылителя. Этот метод требует наибольшего количества навыков для создания высококачественных деталей, но это также наименее затратный рабочий процесс с минимальными требованиями для начала изготовления деталей из углеродного волокна своими руками. Если вы новичок в производстве деталей из углеродного волокна и еще не оборудовали его, мы рекомендуем начать с ручного ламинирования мокрым слоем.
Посмотрите видео, чтобы увидеть, как работает процесс мокрой укладки при ламинировании деталей из углеродного волокна.
При ламинировании препрега смола вводится в волокно впереди. Предварительно пропитанные листы хранят в холоде, чтобы предотвратить отверждение. Затем слои затвердевают в форме под действием тепла и давления в автоклаве. Это более точный и повторяемый процесс, поскольку количество смолы регулируется, но это также самый дорогой метод, который обычно используется в высокопроизводительных приложениях.
При формовании RTM сухое волокно вставляется в форму, состоящую из двух частей. Форма закрывается зажимом перед тем, как под высоким давлением нагнетать смолу в полость. Обычно он автоматизирован и используется для крупносерийного производства.
Поскольку качество пресс-формы напрямую влияет на качество готовой детали, изготовление инструмента является критическим аспектом производства FRP. Большинство форм изготавливаются из воска, пены, дерева, пластика или металла с помощью обработки с ЧПУ или вручную. Хотя ручные методы очень трудозатратны, обработка на станках с ЧПУ по-прежнему является сложным и трудоемким рабочим процессом — особенно для сложных геометрических форм — а аутсорсинг обычно требует больших затрат и длительного периода времени.Оба варианта требуют квалифицированных рабочих и предлагают небольшую гибкость при изменении дизайна и корректировки пресс-формы.
Аддитивное производство предлагает решение для быстрого изготовления пресс-форм и моделей с низкими затратами. Использование полимерной оснастки в производственных процессах постоянно растет. Замена металлических инструментов пластиковыми деталями, напечатанными собственными силами, — это мощное и экономичное средство сокращения времени производства при одновременном расширении гибкости дизайна. Инженеры уже работают с деталями из полимерной смолы, напечатанными на 3D-принтере, для изготовления приспособлений и приспособлений для поддержки таких методов, как намотка нити или автоматическая укладка волокна.Аналогичным образом, мелкосерийные печатные формы и матрицы используются при литье под давлением, термоформовании или формовании листового металла для доставки партий небольшого объема.
Для 3D-печати с настольных компьютеров требуется ограниченное количество оборудования, что упрощает рабочий процесс. Профессиональные настольные принтеры, такие как Form 3, доступны по цене, просты в установке и могут быстро масштабироваться в соответствии со спросом. Изготовление больших инструментов и форм также возможно с помощью широкоформатных 3D-принтеров, таких как Form 3L.
Стереолитография (SLA) Технология 3D-печати позволяет создавать детали с очень гладкой поверхностью, что очень важно для пресс-формы.Он позволяет создавать сложные геометрические формы с высокой точностью. Кроме того, библиотека смол Formlabs содержит технические материалы с механическими и термическими свойствами, которые хорошо сочетаются с производством форм и моделей.
3D-печатные формы для производства деталей из углеродного волокна могут снизить затраты и сократить время выполнения заказа.
Для мелкосерийного производства инженеры могут напрямую распечатать пресс-форму с небольшими затратами и в течение нескольких часов без необходимости вырезать ее вручную или иметь дело с оборудованием с ЧПУ; Программное обеспечение CAM, наладка станка, оснастка, инструмент и удаление стружки.Значительно сокращаются трудозатраты и сроки изготовления пресс-форм, что позволяет быстро изменять дизайн и настраивать детали. Они могут создавать сложные формы с мелкими деталями, которые было бы трудно изготовить традиционными методами.
Команда Formula Student Берлинского технического университета (FaSTTUBe) изготовила десяток деталей из углеродного волокна для гоночных автомобилей. Инженеры в команде вручную наносят ламинат на форму, непосредственно напечатанную с помощью смолы Formlabs Tough 1500. Эта смола характеризуется модулем упругости при растяжении, равным 1.5 ГПа и удлинение при разрыве 51%. Он не только прочный и поддерживающий во время укладки, но и достаточно гибкий, чтобы отделить деталь от формы после отверждения.
Испытательный стенд FaSTTUBe с установкой производства деталей из углеродного волокна.
Хотя этот метод не связан с интенсивными условиями отверждения, другие процессы ламинирования часто требуют более высоких давлений и температур. Компания DeltaWing Manufacturing использует высокотемпературную смолу для создания компонентов воздушного потока посредством процесса препрега.Смола High Temp Resin имеет температуру теплового отклонения (HDT) 238 ° C при 0,45 МПа и способна выдерживать тепло и давление автоклава. Компания DeltaWing Manufacturing напрямую печатает пресс-формы для производства серии из 10 деталей по индивидуальному заказу.
Воздуховод крыла из углеродного волокна рядом с двухкомпонентной формой, напечатанной высокотемпературной смолой, произведенной DeltaWing Manufacturing.
Полимерные формы, напечатанные на 3D-принтере, являются отличным инструментом для оптимизации мелкосерийного производства. Однако их срок службы сокращен по сравнению с традиционными формами, что делает их непригодными для массовых серий.
Для увеличения производства DeltaWing Manufacturing печатает модели пресс-форм с помощью высокотемпературной смолы, а затем заливает их в смолу. Печать рисунка также является мощной альтернативой для процессов ламинирования, требующих интенсивных условий отверждения, которые не подходят для форм, напечатанных на 3D-принтере. Производители могут печатать индивидуальные выкройки по запросу и при этом исключить один шаг из своей техники изготовления форм — изготовление выкройки.
Производство армированных волокном полимеров — увлекательный, но сложный и трудоемкий процесс.Использование 3D-печатных форм и шаблонов позволяет предприятиям упростить рабочий процесс, расширить гибкость и возможности проектирования, а также сократить расходы и время выполнения заказа.
На основе тематических исследований с TU Berlin и DeltaWing Manufacturing в нашем техническом документе представлены три рабочих процесса для использования 3D-печати в производстве композитов с быстрым изготовлением пресс-форм и шаблонов.
Армирование — композитные материалы | CompositesLab
Многие материалы могут армировать полимеры.Некоторые материалы, такие как целлюлоза в древесине, являются продуктами природного происхождения. Однако большая часть коммерческого подкрепления создается руками человека. Существует множество имеющихся в продаже форм армирования, отвечающих проектным требованиям пользователя. Возможность адаптировать архитектуру волокна позволяет оптимизировать производительность продукта, что приводит к снижению веса и затрат.
Хотя многие виды волокон используются в качестве армирующих в многослойных композитных материалах, стекловолокна составляют более 90 процентов волокон, используемых в армированных пластмассах, поскольку их производство недорогое и они имеют относительно хорошие характеристики прочности к весу.
- Стекловолокно: На основе алюмооксидно-известково-боросиликатной композиции волокна, произведенные из стекла «E» или «E-CR», считаются преобладающими армирующими элементами для композитов с полимерной матрицей из-за их высоких электроизоляционных свойств, низкой восприимчивости к влажность и высокие механические свойства. Стекло E-CR дополнительно отличается от стекла E своей превосходной стойкостью к коррозии. Другие коммерческие композиции включают стекло S с более высокой прочностью, термостойкостью и модулем, H-стекло с более высоким модулем и стекло AR (стойкое к щелочам) с превосходной коррозионной стойкостью.Стекло, как правило, является хорошим ударопрочным волокном, но весит больше, чем углерод или арамид. Стекловолокно имеет отличные механические характеристики, в некоторых формах оно прочнее стали. Более низкий модуль упругости требует специальной обработки, когда жесткость имеет решающее значение. Стекловолокно прозрачно для радиочастотного излучения и используется в радиолокационных антеннах.
- Углеродные волокна: Углеродные волокна изготавливаются из органических прекурсоров, включая PAN (полиакрилонитрил), вискозу и смолы, причем последние два обычно используются для низкомодульных волокон.Термины «углеродные» и «графитовые» волокна обычно используются взаимозаменяемо, хотя графит технически относится к волокнам, которые содержат более 99 процентов углерода по сравнению с 93-95 процентами для углеродных волокон на основе ПАН. Углеродное волокно обеспечивает самую высокую прочность и жесткость из всех армирующих волокон. Высокотемпературные характеристики особенно хороши для углеродных волокон. Основным недостатком волокон на основе ПАН является их высокая относительная стоимость, которая является результатом стоимости основного материала и энергоемкого производственного процесса.Композиты из углеродного волокна более хрупкие, чем стекло или арамид. Углеродные волокна могут вызвать гальваническую коррозию при использовании рядом с металлами. Для предотвращения этого используется барьерный материал, такой как стекло и смола.
- Арамидные волокна (полиарамиды): Наиболее распространенным синтетическим волокном является арамид. Арамидное волокно — это ароматический полиимид, который представляет собой искусственное органическое волокно для армирования композитов. Арамидные волокна обладают хорошими механическими свойствами при низкой плотности с дополнительным преимуществом прочности или устойчивости к повреждениям / ударам.Они характеризуются достаточно высокой прочностью на разрыв, средним модулем упругости и очень низкой плотностью по сравнению со стеклом и углеродом. Арамидные волокна являются изоляторами электричества и тепла и повышают ударопрочность композитов. Они устойчивы к воздействию органических растворителей, горюче-смазочных материалов. Композиты из арамида не так хороши по прочности на сжатие, как композиты из стекла или углерода. Сухие арамидные волокна прочны и используются в качестве тросов или канатов и часто используются в баллистических приложениях.Кевлар®, пожалуй, самый известный пример арамидного волокна. Арамид является преобладающим заменителем органического армирующего волокна для стальных лент в шинах.
- Новые волокна: Полиэфирные и нейлоновые термопластические волокна недавно были представлены как в качестве первичного армирования, так и в гибридной конфигурации со стекловолокном. К привлекательным характеристикам можно отнести низкую плотность, разумную стоимость и хорошую устойчивость к ударам и усталости. Хотя полиэфирные волокна обладают довольно высокой прочностью, их жесткость значительно ниже, чем у стекла.Более специализированные арматуры для высокопрочных и высокотемпературных применений включают металлы и оксиды металлов, такие как те, которые используются в самолетах или аэрокосмической отрасли.
Независимо от материала, усиление доступно в различных формах, чтобы удовлетворить широкий спектр процессов и требований к конечному продукту. Материалы, поставляемые в качестве армирующего материала, включают ровинг, измельченное волокно, рубленые пряди, непрерывный, рубленый или термоформованный мат. Армирующие материалы могут быть спроектированы с уникальной архитектурой волокон и иметь предварительную форму (форму) в зависимости от требований к продукту и производственного процесса.
- Многоконечные и односторонние ровинги: Ровинги используются в основном в термореактивных компаундах, но могут использоваться и в термопластах. Многоконцевые ровницы состоят из множества отдельных прядей или пучков нитей, которые затем нарезаются и случайным образом осаждаются в матрице смолы. В таких процессах, как формование листов (SMC), преформа и напыление, используется многосторонний ровинг. Многоконечные ровницы также могут использоваться в некоторых приложениях для намотки волокон и пултрузии. Односторонний ровинг состоит из множества отдельных нитей, намотанных в одну прядь.Продукт обычно используется в процессах, в которых используется однонаправленное армирование, например, намотка нитей или пултрузия.
- Маты и вуали: Армирующие маты и вуали из нетканого материала обычно описываются по весу на единицу площади. Например, коврик из рубленых прядей весом 2 унции будет весить 2 унции на квадратный ярд. Тип армирования, дисперсия волокон и количество связующего, которое используется для скрепления мата или вуали, определяют различия между матовыми изделиями. В некоторых процессах, таких как ручная укладка, необходимо, чтобы связующее растворилось.В других процессах, особенно при компрессионном формовании и пултрузии, связующее должно выдерживать гидравлические силы и растворяющее действие матричной смолы во время формования. Следовательно, с точки зрения связующего, производятся две основные категории матов или вуалей, которые известны как растворимые и нерастворимые связующие.
- Тканые, прошитые, плетеные и трехмерные ткани: Существует множество типов тканей, которые можно использовать для усиления смол в композитах. Многонаправленное армирование производится путем плетения, вязания, сшивания или плетения непрерывных волокон в ткань из крученой и крученой пряжи.Ткани можно изготавливать с использованием практически любого армирующего волокна. Чаще всего используются ткани из стекловолокна, карбона или арамида. Ткани обладают ориентированной прочностью и высокими усиливающими нагрузками, которые часто встречаются в высокопроизводительных приложениях. Ткани позволяют точно разместить армирование. Это невозможно сделать с измельченными волокнами или рублеными прядями и возможно только с непрерывными прядями с использованием относительно дорогостоящего оборудования для укладки волокон. Из-за непрерывной природы волокон в большинстве тканей отношение прочности к весу намного выше, чем у вариантов с разрезанным или рубленым волокном.Сшитые ткани позволяют настраивать ориентацию волокон в структуре ткани. Это может быть большим преимуществом при проектировании устойчивости к сдвигу или кручению.
- Однонаправленное: Однонаправленное армирование включает ленты, жгуты, однонаправленный жгутовый лист и ровинг (которые представляют собой совокупности волокон или прядей). Волокна в этой форме все выровнены параллельно в одном направлении и не изогнуты, что обеспечивает высочайшие механические свойства. Композиты, использующие однонаправленные ленты или листы, обладают высокой прочностью в направлении волокна.Однонаправленные листы тонкие, и для большинства структурных приложений требуется несколько слоев. Типичные области применения однонаправленного армирования включают высоконагруженные композитные материалы, такие как компоненты самолетов или гоночные лодки.
- Препрег: Препрег — это готовый материал, состоящий из армирующей формы и полимерной матрицы. Для изготовления препрега используется пропускание армирующих волокон или форм, таких как ткани, через ванну со смолой. Смола пропитывается (пропитывается) волокном, а затем нагревается, чтобы продвинуть реакцию отверждения до различных стадий отверждения.Доступны термореактивные или термопластичные препреги, которые можно хранить в холодильнике или при комнатной температуре в зависимости от составляющих материалов. Препреги можно наносить вручную или механически в различных направлениях в зависимости от требований конструкции.
- Размолотые: Молотые волокна — это рубленые волокна с очень короткой длиной волокна (обычно менее 1/8 дюйма). Эти продукты часто используются в термореактивных замазках, отливках или синтаксических пенах для предотвращения растрескивания затвердевшего состава из-за усадки смолы.
Что такое композитный материал? (Полное руководство)
Композитный материал — это комбинация двух материалов с разными физическими и химическими свойствами. Когда они объединяются, они создают материал, который специализируется на выполнении определенной работы, например, чтобы стать прочнее, легче или устойчивым к электричеству. Они также могут улучшить прочность и жесткость. Причина их использования по сравнению с традиционными материалами заключается в том, что они улучшают свойства основных материалов и применимы во многих ситуациях.
Если у вас есть вопросы или вам нужна помощь, напишите нам, чтобы получить консультацию специалиста:
Нажмите здесь, чтобы увидеть наши последние подкасты по технической инженерии на YouTube .Содержание
Люди использовали композиты тысячи лет. В 3400 г. до н.э. г. первые искусственные композиты были созданы месопотамцами в Ираке. Древнее общество склеивало деревянные полоски друг на друга под разными углами для создания фанеры.После этого, примерно в 2181 г. до н.э., г. до н.э. египтяне начали делать посмертные маски из льняной ткани или папируса, пропитанного гипсом. Позже оба этих общества начали укреплять свои материалы соломой, чтобы укрепить глиняные кирпичи, глиняную посуду и лодки.
В 1200 годах нашей эры монголы начали создавать составные луки, которые были невероятно эффективными в то время. Они были сделаны из дерева, бамбука, кости, сухожилий крупного рогатого скота, рога и шелка, скрепленных сосновой смолой.
После промышленной революции синтетические смолы начали принимать твердую форму с помощью полимеризации.В 1900-х годах эти новые знания о химических веществах привели к созданию различных пластмасс, таких как полиэстер, фенол и винил. Затем начали разрабатываться синтетические материалы, бакелит был создан химиком Лео Бэкеландом. Тот факт, что он не проводил электричество и был термостойким, означал, что он мог широко использоваться во многих отраслях промышленности.
1930-е годы были невероятно важным временем для развития композитов. Стекловолокно было представлено компанией Owens Corning, которая также положила начало производству первых армированных волокном полимеров (FRP).Смолы, разработанные в ту эпоху, используются по сей день, а в 1936 были запатентованы ненасыщенные полиэфирные смолы. Два года спустя стали доступны системы смол с более высокими эксплуатационными характеристиками.
Первое углеродное волокно было запатентовано в 1961 и затем стало коммерчески доступным. Затем, в середине 90-х , композиты начали становиться все более распространенными для производственных процессов и строительства из-за их относительно дешевой стоимости по сравнению с материалами, которые использовались ранее.
Композитные материалы на Boeing 787 Dreamliner в середине 2000-х годов подтвердили их использование для высокопрочных приложений.
Некоторые распространенные композитные материалы включают:
- Композит с керамической матрицей: Керамика, выложенная в керамической матрице. Это лучше, чем обычная керамика, поскольку она устойчива к тепловым ударам и разрушению
- Композит с металлической матрицей : Металл, растекающийся по матрице
- Железобетон : Бетон, усиленный материалом с высокой прочностью на разрыв, таким как стальные арматурные стержни
- Бетон, армированный стекловолокном : Бетон, залитый в структуру из стекловолокна с высоким содержанием диоксида циркония
- Прозрачный бетон : Бетон, покрывающий оптические волокна
- Конструкционная древесина : Обработанная древесина в сочетании с другими дешевыми материалами.Одним из примеров может быть ДСП. В этом композите также можно найти специальный материал, такой как шпон.
- Фанера : древесина, полученная путем склеивания множества тонких слоев древесины вместе под разными углами
- Искусственный бамбук : Полоски бамбукового волокна, склеенные вместе, чтобы образовать доску. Это полезный композит, потому что он имеет более высокую прочность на сжатие, растяжение и изгиб, чем древесина .
- Паркет : Квадрат, состоящий из множества деревянных частей, часто собранных из твердой древесины.Продается как декоративный элемент .
- Древесно-пластиковый композит : пластик, отлитый из древесного волокна или муки
- Цементное древесное волокно : Минерализованные деревянные детали, отлитые в цемент. Этот композит имеет изоляционные и акустические свойства
- Стекловолокно : Стекловолокно в сочетании с относительно недорогим и гибким пластиком
- Полимер, армированный углеродным волокном : Набор из углеродного волокна в пластике с высоким отношением прочности к весу
- Сэндвич-панель : различные композиты, уложенные друг на друга
- Составные соты : Набор шестиугольников из композитных материалов, образующих сотовую структуру.
- Папье-маше : Бумага с клеевым переплетом. Они найдены в ремеслах
- Бумага с пластиковым покрытием : Бумага с пластиковым покрытием для повышения прочности. Пример того, где это используется, — в игральных картах .
- Синтаксическая пена : Легкие материалы, получаемые при заполнении металлов, керамики или пластика микрошариками. Эти баллоны изготавливаются из стекла, углерода или пластика
Что такое композиты и для чего они используются?
Формы армирующих материаловВ зависимости от способа изготовления и желаемых характеристик композитной детали армирующий материал может быть переработан в различные формы.Вообще говоря, обработанные арматурные материалы можно разделить на две основные подкатегории:
- Непрерывные волокна
Эта форма армирования имеет волокна полной длины, расположенные в определенной ориентации по отношению к соседним волокнам. Непрерывные волокна имеют чрезвычайно большое отношение длины волокна к диаметру и, как правило, демонстрируют отличные характеристики прочности и жесткости. - Прерывистые волокна
Эти волокна обрабатываются с произвольной ориентацией и часто имеют меньшее отношение длины волокна к диаметру.Эти волокна либо разрезаются на небольшие пряди во время производства, либо перерабатываются в листы с волокнами, распределенными случайным образом и перекрывающими друг друга.
Непрерывные волокна обычно используются, когда требуются прочность и жесткость. В процессе проектирования дизайнеры используют ориентацию волокон для усиления деталей в том направлении, в котором они нагружаются. Когда прочность и жесткость не важны, часто используются изделия из прерывистых волокон, которые обычно обеспечивают преимущества в скорости производства.
Продукция из непрерывного волокна Буксир / лента
Эта форма содержит намотанные пучки отдельных нитей. Количество волокон в пучке обычно является основным определяющим признаком, который отличает жгуты друг от друга. Эта форма обычно используется в процессах намотки волокон для изготовления цилиндрических конструкций. Буксиры также используются для локального усиления или ремонта. В некоторых методах производства (ламинирование распылением) жгуты нарезаются на небольшие отрезки волокон и опрыскиваются смесью смолы.
Ткани
Эти ткани обрабатываются путем взятия отдельных жгутов и ткутся в двух направлениях, таким образом получаются пряди, перпендикулярные друг другу (пряди под углом 0 ° и пряди под углом 90 °). Двумя наиболее распространенными стилями тканого материала являются:
Обычное переплетение: В этом расположении каждая нить под углом 0 ° попеременно проходит над каждой стойкой под углом 90 ° и под ней. Это расположение повторяется по всей ширине и длине тканого полотна. Это обеспечивает симметричный рисунок и однородные свойства материала в направлениях 0 ° и 90 °.Это переплетение легче производить, чем большинство других переплетений, но оно приводит к большому объему «извитости» ткани (геометрическое уменьшение длины тканого полотна по сравнению со сплошной прядью из-за кривизны волокна при расположении сверху и снизу). Поскольку волокна обеспечивают наибольшую прочность, когда они выровнены с нагрузкой, такое расположение снижает механические свойства материала по сравнению с другими переплетениями. Обычное переплетение обладает хорошей стабильностью и упрощает обращение с ним, но его труднее обтягивать вокруг сложной кривизны.
Саржевое переплетение: В этой компоновке каждая стойка 0 ° попеременно проходит над и под двумя стойками 90 ° в повторяющемся узоре по ширине и длине ткани. Этот тип переплетения дает меньше «извитости» ткани, и саржевые переплетения обычно имеют улучшенные механические свойства по сравнению с полотняным переплетением. Компоновка имеет пониженную устойчивость, и с ней труднее обращаться. Их легче обернуть вокруг изгибов, но необходимо осторожно обращаться с ними, чтобы не допустить появления зазоров и пористости в производственном процессе.
Нетканые материалы
Эти ткани обрабатываются путем взятия отдельных жгутов и создания структуры с помощью нейлоновых стежков или с помощью мягкого клея. И затем организованы в однонаправленном (0 °) или двунаправленном (0 ° и 90 °) расположении.
Волокнистый мат
Эта обработанная форма обычно содержит рубленые волокна армирующего материала, взвешенного в связующем.Количество нарезанной нити, длина нитей и тип связующего будут определять свойства и методы производства, подходящие для конкретного мата. С этими материалами легко работать, и они сокращают время, необходимое для производства ламината. Маты также могут быть изготовлены из непрерывных волокон, при этом волокна распределены случайным образом.
Вуаль — это особый тип волокнистого мата, который содержит тонкие волокна и обычно используется на поверхности ламината, чтобы уменьшить отпечаток волокна и улучшить качество поверхности.
Материал матрицыМатричный материал удерживает и связывает армирующий материал и затвердевает, определяя форму конечной детали. По сравнению с армирующим материалом матричный материал относительно слаб и не имеет жесткости. В сценарии нагружения матричный материал удерживает волокна на месте и передает нагрузку между волокнами и слоями. Матричный материал в производстве композитных деталей обычно имеет полимерную основу и затвердевает из жидкого состояния в присутствии отвердителя, воздуха или тепла.
Материалы с полимерной матрицей можно разделить на две основные категории: термореактивные и термопластические.
Термореактивные полимеры наиболее популярны в современных композитных деталях. Эти полимеры начинаются в жидком состоянии и отверждаются, образуя трехмерную молекулярную сеть. Этот процесс называется сшиванием, и он дает твердое вещество стабильной формы, которое имеет то преимущество, что оно устойчиво к нагреванию и химическим веществам. Кроме того, трехмерная сеть молекулярных связей придает этим формам полимеров хорошие механические прочностные свойства.Большинство полиэфиров, сложных виниловых эфиров и эпоксидных смол, используемых в промышленности, представляют собой термореактивные полимеры.
Термопластичные полимеры обычно нагревают до температуры выше 500 ° C и формуют в форму детали. Преимущество этих полимеров в том, что они быстрее производятся, поскольку процесс отверждения состоит только из охлаждения. Эти полимеры не обладают термостойкостью и плавятся до вязкой жидкости при воздействии высокой температуры. Некоторые полиэфирные смолы представляют собой термопластичные полимеры.
В настоящее время основными матричными материалами, используемыми в промышленности, являются полиэфиры, сложные виниловые эфиры и эпоксидные смолы.Система смолы выбирается в зависимости от области применения и требуемых свойств конечной детали. Наполнители и добавки часто могут быть добавлены к большинству систем смол и получить такие характеристики, как огнестойкость.
Полиэфирные смолы
Полиэфирные смолы являются наиболее широко используемой системой смол. Эти смолы представляют собой примерно половину сложноэфирных полимеров, смешанных с мономерами стирола. В молекулярной структуре стирол обеспечивает сшивание за счет связывания между соседними полиэфирными цепями в определенных реакционных участках вдоль цепи.Для типичных полиэфирных смол требуется катализатор для начала процесса сшивания стиролом. Этот процесс называется полимеризацией. Полиэфирные смолы имеют хорошую цену и быстрое время отверждения по сравнению с другими системами смол. Эта система смол хорошо работает в присутствии воды и может быть адаптирована для обеспечения химической стойкости. Полиэфирные смолы обладают приемлемыми адгезионными и механическими свойствами по сравнению с другими системами смол.
Винилэфирные смолы
Системы винилэфирных смол имеют ту же структуру основной цепи, что и системы полиэфирных смол, но имеют большинство реактивных центров на концах основной полимерной цепи.Кроме того, винилэфирные смолы имеют меньшее количество сложноэфирных групп, что делает их более водостойкими. Смолы на основе сложного винилового эфира обладают улучшенными способностями к ингибированию трещин по сравнению со смолами на основе сложного полиэфира из-за расположения поперечных связей. Поскольку сшивание происходит только на концах параллельных цепей, системы винилэфирных смол способны поглощать больше энергии до того, как в результате удара начнут образовываться трещины. Кроме того, винилэфирные смолы обладают улучшенной адгезией, механической жесткостью и прочностью по сравнению со смолами на основе сложного полиэфира.
Эпоксидные смолы
Эпоксидные смолы похожи на системы винилэфирных смол в том, что на концах основной полимерной цепи существуют реакционные центры.Основное различие между этими системами смол заключается в отсутствии сложноэфирных групп в основной цепи. Вместо этого на реакционных участках обнаруживаются эпоксидные группы. Эпоксидные смолы также отличаются тем, что для них требуется отвердитель, который представляет собой аминогруппу, которая смешивается со смолой для ее отверждения. Соотношение отвердителя и смолы важно, так как любой избыток любого компонента останется неотвержденным. Эпоксидные системы обладают превосходной адгезией, механической жесткостью и прочностью. Кроме того, из-за отсутствия сложноэфирных групп эпоксидная система очень хорошо работает в морских условиях и устойчива ко многим промышленным химическим веществам.
Тип смолы | Типичный модуль упругости при растяжении (ГПа) | Типичный предел прочности на разрыв (МПа) |
---|---|---|
Полиэфирные смолы | 3,45 | 55 |
Винилэфирные смолы | 3,59 | 80 |
Эпоксидные смолы | 10,5 | 85 |
Гелевые покрытия часто используются в сочетании с системами полиэфирных и винилэфирных смол и представляют собой термореактивный пластик.Они служат в качестве защитного и эстетичного финишного покрытия, которое защищает матрицу и армирующий материал от ультрафиолетового излучения и химического разложения. Их также можно тонировать и красить, чтобы воспроизвести любой цвет, и они имеют значительное преимущество перед краской как с точки зрения труда, так и с точки зрения затрат на отделку композитной детали. Кроме того, в случае повреждения верхнего покрытия гелькоуты можно восстановить и восстановить гораздо быстрее и с меньшими затратами, чем окрашенные поверхности.
Гель-покрытие наносится толстым (10-20 мм) слоем непосредственно на подготовленную поверхность формы перед ламинированием.Желаемая толщина обычно достигается до 2 или 3 слоев с достаточным промежутком времени между нанесениями. Остальная часть процесса ламинирования остается неизменной, а общая отделка детали после выпуска значительно улучшается.
Материал сердечникаОсновной материал часто приклеивается между «оболочками» из армированного пластика. Сердечники обычно используются для увеличения толщины деталей с небольшими потерями в весе или стоимости. Добавление сердечника значительно улучшает жесткость на изгиб (изгиб) и прочность детали.
Когда материал нагружается при изгибе, верхняя поверхность материала сжимается, а нижняя поверхность растягивается. Чем дальше друг от друга расположены верхняя и нижняя поверхности изгибаемой детали, тем больше жесткость и прочность детали. В этой форме нагрузки материал сердечника испытывает так называемую сдвигающую нагрузку, поскольку верх и низ материала тянутся в противоположных направлениях.
Основные материалы варьируются в широком диапазоне в зависимости от области применения, метода ламинирования и условий окружающей среды.
Пенопласт
Сердцевины из ПВХ (поливинилхлорида) представляют собой химически / влагостойкий пенопласт с закрытыми порами, который обеспечивает хорошую прочность на сдвиг и адгезионные свойства. Эти сердечники представляют собой жесткий термореактивный материал, но их можно легко термоформовать с помощью тепла и давления. Они производятся различной толщины и плотности и совместимы с большинством систем смол и методов ламинирования.
SAN Foam
Сердечники из пенопласта SAN (стиролакрилонитрил) представляют собой легкую вспененную сердцевину с закрытыми порами, которая обеспечивает превосходную химическую стойкость.Они часто используются в производстве с очень высокими требованиями, где требуется высокая температура или высокое давление. SAN обладает уникальным свойством быть термопластом и может легко формоваться при нагревании.
Ячеистые сердечники
Ячеистые сердечники могут быть изготовлены из различных материалов, но обычно их изготавливают из алюминия или бумаги на основе кевлара, известной как Номекс. Ячейки расположены в виде сот, что обеспечивает хороший компромисс между прочностью и весом. Эти стержни можно легко согнуть и придать им сложную форму.При ручном ламинировании и ламинировании с применением смолы этот тип сердцевины может быть пропитан смолой.
Деревянные стержни
Деревянные стержни обладают очень хорошей прочностью на сжатие и сдвигом за счет веса. Обычно используется древесина бальзы с торцевым покрытием. Этот тип сердечника часто используется в сценариях локального нагружения, где ожидаются высокие сжимающие напряжения. Кроме того, этот сердечник часто используется в местах с разрывом, например в отверстиях для болтов и других локальных концентраторах напряжений.Сердечники из бальзы, обработанные герметиками, могут использоваться во влажных средах и могут использоваться с большинством систем смол и методов производства.
Тканевые сердечники
Тканевые сердечники и маты обычно намного тоньше, чем другие материалы сердечников. Их обычно называют «объемными» материалами, в отличие от сердцевины, и они увеличивают толщину ламината. В основном они представляют собой тканые листы из полиэстера с закрытыми ячейками, поэтому они не впитывают смолу в процессе ламинирования.Эти сердечники гибкие и соответствуют изгибам и изгибам детали. Тканевые сердечники обычно имеют очень низкую плотность и не используются там, где требуется высокая прочность сердечника на сдвиг.
Методы производства композитных деталей были адаптированы для соответствия требованиям детали и материала. Практически все методы изготовления требуют наличия пресс-формы для обозначения формы составной детали.
Формы (или инструменты) конструируются вокруг конечной детали, которая должна быть произведена, выбранного метода изготовления и требуемой точности готовой детали.В композитной промышленности есть два основных обозначения инструментов… а именно твердые и мягкие инструменты.
Твердые инструменты изготавливаются из керамики, металлов и древесины высокой плотности. Они требуют больших начальных вложений как в материале, так и в стоимости обработки. Эти типы инструментов обычно используются многократно, и материал выбирается в зависимости от прочности, необходимой для формы. Кроме того, материал выбирается в зависимости от способа изготовления (т.е. для детали, отверждаемой при температуре, для одновременного теплового расширения должен использоваться правильный инструментальный материал).Эти типы инструментов также могут лучше выдерживать допуски на размеры.
Мягкие инструменты изготавливаются из пенопласта, композитов или других обрабатываемых материалов, которые будут изнашиваться и ухудшаться по мере производства большего количества деталей. Эти инструменты имеют более низкую стоимость и не так хорошо подходят для соблюдения строгих допусков по размерам.
Подготовка инструмента важна для окончательной обработки детали. Новые инструменты готовятся к использованию путем предварительной полировки поверхности до желаемого показателя шероховатости. Шероховатость поверхности инструмента напрямую влияет на шероховатость поверхности, которая будет отпечатана на детали.Затем на поверхность наносится межфазное покрытие, которое заполняет очень мелкие ямки и царапины. Затем на поверхность инструмента наносится разделительный агент, который позволяет удалить деталь после полного отверждения. Межфазный слой обеспечивает хорошую поверхность для прилипания антиадгезионного средства. Традиционно разделительные агенты были расходным материалом, и их нужно было наносить после снятия каждой детали с инструмента. В последнее время используются полуперманентные разделительные агенты, срок службы которых может составлять до 20 частей, и их можно оставить на поверхности формы, когда потребуется новое покрытие.
По мере роста разнообразия деталей и областей применения постоянно появляются новые методы производства композитных деталей. В целом, большинство методов производства можно разделить на следующие категории:
Открытая форма / ручное ламинирование
Это основная форма ламинирования. Слои армирующего материала и сердечника укладываются друг на друга в заданной последовательности и слой за слоем смачиваются системой смолы поверх подготовленной формы. Готовый ламинат затем отверждается в соответствии с требованиями к системе смолы.Этому процессу отверждения может способствовать использование тепла.
Этот метод обычно используется для изготовления единичных деталей по индивидуальному заказу и небольших производственных партий. Для ручного ламинирования не требуется сложного оборудования, инструментов или расходных материалов. Этот процесс приводит к некоторому изменению качества и прочности деталей из-за несоответствия в распределении смолы и захвата воздушных пустот между слоями. Ручное ламинирование также трудно эффективно наращивать в объеме производства, поскольку это трудоемкий процесс.Эффективность этого процесса можно повысить, используя систему распыления смолы и предварительно нарезав армирующий материал перед ламинированием.
Ламинирование распылением
В этой форме ламинирования используется пневматический пистолет-распылитель, который измельчает нити армирующего материала и смеси смолы непосредственно на поверхность формы. Этот метод обычно начинается с нанесения гелевого покрытия на поверхность формы. Затем смесь смолы, катализатора и рубленого армирующего материала распыляют поверх формы и уплотняют с помощью валика.Можно нанести сердцевину и последующие слои для придания дополнительной жесткости. Обычно ламинат затем отверждают при комнатной температуре или в печи, в зависимости от требований к смоле. Затем деталь удаляется, и форму можно подготовить для следующего производственного цикла.
Этот метод сокращает время, необходимое для завершения ламинирования. Кроме того, он подходит для больших деталей, так как этот метод обеспечивает большую зону покрытия. В методах ламинирования распылением используются прерывистые волокна, что значительно снижает прочность детали.Кроме того, из-за несоответствий при распылении бывает трудно поддерживать допуски. Эта форма производства также вызывает опасения по поводу здоровья и окружающей среды, поскольку в атмосферу выбрасывается большое количество стирола.
Мокрый мешочек
Подобно ламинированию вручную, этот процесс требует, чтобы армирующие слои смачивались полимерной системой слой за слоем поверх подготовленной формы. Перед отверждением смолы расходный разделительный слой, абсорбирующий смолу материал и пленку для вакуумного мешка помещают поверх последнего слоя армирующего материала.Затем пленка для вакуумного мешка прикрепляется к концам формы с помощью герметичной мастичной ленты. Затем используется вакуум, чтобы втягивать воздух между поверхностью формы и пленкой вакуумного мешка, создавая таким образом давление и удаляя воздушные пустоты, захваченные между слоями армирующего материала. Расположение вакуумного порта и использование «сапуна» в стратегически важных местах важно для обеспечения равного давления вакуума по всей детали.
Этот процесс значительно улучшает межслойные связи, что приводит к большей структурной целостности.Для этого метода ламинирования необходимо выбрать полимерную систему с подходящим временем отверждения, чтобы слои могли быть тщательно намочены и упакованы в мешки перед отверждением. Системы смол могут быть разработаны таким образом, чтобы обеспечивать различное время отверждения.
Инфузия смолы
При ламинировании методом инфузии смолы сухие слои армирующего материала и сердцевины размещаются в правильной последовательности поверх подготовленной поверхности формы. Форма также стратегически оснащена линией подачи смолы и линией вакуумной вытяжки.Затем ламинат покрывают пористым отделяемым слоем и текучей средой, которая обеспечивает течение смолы во время процесса настаивания. Затем устанавливается герметичный вакуумный мешок, который герметизирует деталь и линии подачи и прорисовки. Затем воздух удаляется из линии вытяжки, а смола с катализатором впрыскивается с противоположного конца детали. Подача смолы и давление вакуума тщательно контролируются во время этого процесса, чтобы гарантировать, что вся деталь равномерно смачивается смолой и имеет эквивалентное давление вакуума по всей детали.После того, как введено нужное количество смолы, линия подачи герметизируется, и ламинату дают возможность затвердеть в условиях регулируемого вакуума и температуры.
Этот метод позволяет изготавливать более крупные и сложные детали по сравнению с методами ламинирования вручную и мокрой упаковки. Кроме того, качество и консистенция деталей улучшаются, поскольку однородность смолы и цикл отверждения между деталями более точно регулируются. Этот метод подходит как для малых, так и для крупных производственных партий и все чаще автоматизируется.У этого метода есть много вариантов, таких как литье смолы с переносом (RTM), вакуумное литье смолы (VARTM) и литье под давлением смолы (RIM), которые имеют схожие процессы, но отличаются тем, как и когда смола вводится и распределяется. Все чаще в полностью автоматизированных установках используется подходящая технология изготовления охватываемой и охватывающей формы, что позволяет сократить трудозатраты и расходные материалы, такие как пленка для вакуумной упаковки в мешки.
Автоклавное отверждение
Автоклавное отверждение чаще всего используется с предварительно пропитанным (препрег) армирующим материалом, когда требуются детали очень высокого качества.Эта форма материала имеет пленку из некатализированной смолы, которая наносится производителем на одну или обе стороны армирующего материала. Этот материал всегда хранится в среде с контролируемым микроклиматом, так как смола катализируется теплом. Эти материалы имеют установленный срок хранения.
В процессе ламинирования препрег и сердцевинный материал помещают поверх подготовленной поверхности формы в заданной последовательности и ориентации. На поверхности препрега присутствует небольшая липкость, позволяющая ему удерживать свое место на поверхности формы без образования пустот и зазоров.Мелкие контуры и узкие углы ламинируются с помощью теплового пистолета, чтобы препрег полностью покрыл поверхность формы. Поскольку материал препрега имеет идеальное количество смолы для количества армирующего материала, любые зазоры или пустоты останутся незаполненными в готовой детали, что делает начальный процесс неотвержденного ламинирования ограничивающим фактором для конечного качества деталей. Между материалом препрега и сердцевиной часто используется пленочный клей, чтобы обеспечить качественное соединение.При отверждении в автоклаве ламинат и форма снабжены вакуумным мешком, который всасывает воздух во время процесса отверждения. Форма и вся деталь помещаются внутри автоклава, который контролирует давление и температуру окружающей среды. Автоклав имеет преимущество создания условий выше 1 атмосферы (14,7 фунта на квадратный дюйм) во время процесса отверждения, что позволяет приложить большее усилие к поверхности детали, таким образом уменьшая пустоты и улучшая межслойные связи. Это увеличенное усилие обычно требуется только для деталей очень высокого качества и почти исключительно используется в аэрокосмической и автомобильной промышленности.
В цикле отверждения в автоклаве температура повышается до промежуточной температуры, вызывая падение вязкости пропитанной смолы, позволяя ей течь и смачивать волокна армирующего материала. Затем температуру повышают до конечной температуры отверждения, при которой смола начинает катализировать и образовывать химические связи. Этот процесс тщательно контролируется с помощью термопар, чтобы гарантировать, что все области детали соответствуют правильным температурным условиям для полного отверждения.
Автоклавные процессы требуют дорогостоящего препрега с ограниченным сроком хранения. Кроме того, закупка оборудования для производственного цикла автоклавов связана с большими капитальными затратами. Как правило, детали также тратят более 8 часов на то, чтобы пройти полный цикл отверждения в автоклаве, что снижает производительность и использование автоклава и формы.
Отверждение в печи
Подобно отверждению в автоклаве, отверждение в печи можно использовать для изготовления деталей из предварительно пропитанного армирующего материала.Отверждение в печи обычно используется, когда не требуется дополнительная сила атмосферы высокого давления. Это резко снижает первоначальные капитальные затраты на производство деталей из препрега. Отверждение в печи также часто используется со стандартными системами смол в определенных областях применения, где требуются особые свойства окончательно отвержденной детали.
Композитные детали часто обрезаются и обрабатываются до желаемых характеристик после окончательного отверждения. Подобно металлам и другим материалам, композиты можно резать, обрезать, шлифовать и обрабатывать.
При небольших объемах производства обычно используются ручная обрезка, шлифовка и чистовая обработка. Эти методы плохо масштабируются и чрезвычайно трудозатратны. Они также вызывают проблемы со здоровьем из-за воздействия мелких твердых частиц.
Композитные детали часто уменьшаются до точных размеров за счет использования прецизионных автоматических инструментов для обрезки деталей, которые способны удалять материал с концов и производить чистые отверстия. Готовая деталь не содержит случайных волокон или отложений смолы.Композитные детали также могут быть уменьшены до окончательных размеров с использованием методов производства листового металла, таких как струя воды, которая оставляет после себя чистые гладкие края.
Когда требуются очень точные посадки и допуски, композитные детали можно обрабатывать с использованием традиционных методов обработки. Обычно насадки компрессионного типа используются для сохранения структуры и распределения армирующего материала в полимерной матрице. Для сверления отверстий используется сверло орбитального типа для предотвращения расслоения и повышения точности размеров по всей глубине отверстия.
Легкий вес тяжеловесов
*Выберите страну / regionUnited StatesCanadaAfghanistanAlbaniaAlgeriaAmerican SamoaAndorraAngolaAnguillaAntarcticaAntigua и BarbudaArgentinaArmeniaArubaAustraliaAustriaAzerbaijanBahamasBahrainBangladeshBarbadosBelarusBelgiumBelizeBeninBermudaBhutanBoliviaBosnia и HerzegovinaBotswanaBouvet IslandBrazilBritish Индийский океан TerritoryBrunei DarussalamBulgariaBurkina FasoBurundiCambodiaCameroonCape VerdeCayman IslandsCentral африканских RepublicChadChileChinaChristmas IslandCocos (Килинг) IslandsColombiaComorosCongoCongo, Демократическая Республика ofCook IslandsCosta RicaCote D’IvoireCroatiaCubaCyprusCzech RepublicDenmarkDjiboutiDominicaDominican RepublicEast TimorEcuadorEgyptEl SalvadorEquatorial GuineaEritreaEstoniaEthiopiaFalkland Острова (Мальвинские) Фарерские острова ФиджиФинляндияФинляндияМорская Республика МакедонияФранцияФранцузская ГвианаФранцузская ПолинезияФранцузские Южные территорииГабонГамбияГрузияГерманияГанаГибралтарГрецияГренландияГренадаГваделупаГуамГу atemalaGuineaGuinea-BissauGuyanaHaitiHeard и McDonald IslandsHoly Престол (Ватикан) HondurasHong KongHungaryIcelandIndiaIndonesiaIran (Исламская Республика) IraqIrelandIsraelItalyJamaicaJapanJordanKazakstanKenyaKiribatiKorea, Корейские Народно-Демократической RepKorea, Республика ofKuwaitKyrgyzstanLao Народный Демократической RepLatviaLebanonLesothoLiberiaLibyan Arab JamahiriyaLiechtensteinLithuaniaLuxembourgMacauMadagascarMalawiMalaysiaMaldivesMaliMaltaMarshall IslandsMartiniqueMauritaniaMauritiusMayotteMexicoMicronesia, Федеративные StatesMoldova, Республика ofMonacoMongoliaMontserratMoroccoMozambiqueMyanmarNamibiaNauruNepalNetherlandsNetherlands AntillesNew CaledoniaNew ZealandNicaraguaNigerNigeriaNiueNorfolk IslandNorthern Mariana IslandsNorwayOmanPakistanPalauPanamaPapua Нового GuineaParaguayPeruPhilippinesPitcairnPolandPortugalPuerto RicoQatarReunionRomaniaRussian FederationRwandaSaint HelenaSaint Китс и НевисСент-ЛюсияСент-Пьер и МикелонСамоаСан-МариноСао-Томе и ПринсипиСаудовская АравияСенегал SeychellesSierra LeoneSingaporeSlovakiaSloveniaSolomon IslandsSomaliaSouth AfricaSpainSri LankaSth Georgia & Sth Sandwich Институт социальных Винсент и GrenadinesSudanSurinameSvalbard и Ян MayenSwazilandSwedenSwitzerlandSyrian Arab RepublicTaiwan, провинция ChinaTajikistanTanzania, Объединенная Республика ofThailandTogoTokelauTongaTrinidad и TobagoTunisiaTurkeyTurkmenistanTurks и Кайкос IslandsTuvaluUgandaUkraineUnited Арабские EmiratesUnited KingdomUruguayUS Малые отдаленные IslandsUzbekistanVanuatuVenezuelaVietnamVirgin острова (Британские) Виргинские острова (U.