Технология производства пластиковых окон ПВХ шаг за шагом
В этой статье расскажем обо всех этапах изготовления пластиковых окон.
Не секрет, что любое производство начинается с закупки материалов и комплектующих. К тому же нужны полуфабрикаты. Поэтому технология изготовления пластиковых окон, как и любая другая, начинается с входного контроля.
Для всех комплектующих имеются соответствующие ГОСТы. Так, уплотнители должны соответствовать ГОСТ 30778-2001, фурнитура – ГОСТ 30777-2001, а профили, используемые для сборки окон ГОСТу 30673-99.
Что касается хранения материала, то он должен складироваться в помещении в нормальных условиях. Необходимо избегать попадания прямых солнечных лучей и не хранить вблизи отопительных приборов. Температура в производственных цехах не должна быть ниже +18 градусов, иначе при низкой температуре обработка пвх профилей может не дать должного качества.
Этапы производства пластиковых окон
Весь процесс изготовления пластиковых окон можно разделить на 11 этапов.
1 этап. На этом этапе происходит резка армирующего профиля. Для этого используют пилы для резки стального армирования с установленными на них абразивными отрезными кругами. В качестве альтернативы могут быть установлены диски для резки металла. Армирующий профиль режут под прямым углом. Заусенцы после распила снимают на наждачном круге.
2 этап. На втором этапе режется ПВХ профиль. Его режут двухголовочными или одноголовочными усорезными пилами. Импосты нарезают под углом 90 градусов, учитывая запас на сторону до 6мм в зависимости от системы профиля. Сами профили створок и коробки нарезают под углом 45 градусов с учетом припуска до 3мм на сторону для сварки.
В процессе резки базовые поверхности профиля прижимают к вертикальному упору и поверхности стола. Для этого используются струбцины. Однако, нужно быть осторожными, чтобы избежать деформации профиля.
3 этап. После того как ПВХ профиль нарезан происходит фрезерование водоотводных окон в нижних профиля коробки оконного блока на фрезерном станке с концевой фрезой. Диаметр фрезы должен быть не более 5 мм. Так же это можно сделать вручную с помощью электродрели со специально заточенным сверлом диаметром 5 мм. Для водоотводных окон обычно не превышает 25 мм.
4 этап. На этом этапе происходит армирование профилей ПВХ. Армирующие профили обрезают по длине и вставляют в профиль ПВХ с помощью специального станка или вручную, используя ручную дрель.
5 этап. После армирования сверлятся отверстия и фрезеруются пазы для фурнитуры на копировально-фрезерном станке. Так же при наличии электроинструмента и специальных насадок и приспособлений это можно сделать вручную.
6 этап. Процесс фрезерования торцов импостов фасонными фрезами с дальнейшей их сборкой и установкой фитингов. Перед установкой на торцы импоста наносят силиконовый герметик.
7 этап. Профили свариваются на специальном сварочном станке. Температура сварного ножа порядка 250 градусов.
8 этап. На восьмом этапе устанавливаются импост и подставочный профиль. Все это делается вручную на сборочном столе с использованием шуруповерта или электродрели.
9 этап. После импоста и подставочного профиля устанавливаются уплотнительные профили. Установка в паз начинается с середины пазов верхних горизонтальных профилей створок и рам. Уплотнитель устанавливается единым неразрывным контуром без растяжения. Концы уплотнителя склеиваются встык циано-акрилатным секундным клеем.
10 этап. Навеска фурнитуры. Для поворотной створки ставится основной запор, петли, угловые переключатели, средние запоры и дополнительный средний петлевой зажим. Для рамы устанавливаются ответные детали запорного механизма и петли. Для наклонно-поворотной створки устанавливается нижняя петля на створку, основной запор и угловые переключатели. Если узкая створка, то на нее ставят средний запор на створку и ножницы. Если створка широкая, то нижний средний запор, средний запор на створку и ножницы. На ответную раму устанавливаются верхние и нижние петли, ответная планка наклонно-поворотного механизма и по периметру ответные планки запорного механизма.
11 этап. Заключительный этап включает в себя резку штапика и установку стеклопакета в профильную систему (максимально плотно!). Внимание! Резка штапика должна быть с направляющими. Во избежания провисания створка со стеклопакетом должна образовывать жесткую конструкцию. После того, как штапики установлены пластиковой киянкой производится осадка части створки. Выполняется предварительная регулировка фурнитуры на стенде, а затем на месте уже после монтажа окна.
Технология производства окон ПВХ, процесс изготовления пластиковых окон
Пластиковые окна уже давно не диковинка для наших соотечественников. Они становятся неотъемлемой частью жилых домов, офисов, зданий административного назначения. Едва ли найдется кто-то, кто никогда не видел их и ничего не слышал о таких изделиях. Вместе с тем есть немало тех, кто не знает, как и из каких материалов делают окна ПВХ и какие технологии используют.
Как как делают стеклопакеты и окна: технология производства
Окно состоит из следующих ключевых компонентов:
- стеклопакет;
- профиль;
- фурнитура.
В настоящее время не составит труда узнать, как делают стеклопакеты — видео процесса доступны не только для профессионалов, но и для всех пользователей Интернета.
Процесс состоит из этапов:
- Резка стекла по нужным размерам.
- Резка дистанционной рамки, на которой крепится стекло.
- Засыпание влагопоглотителя в дистанционную рейку.
- Сборка контура стеклопакета.
- Первичная герметизация — нанесение уплотнителей.
- Сборка стеклопакета (вставка стекол).
- Обжим.
Вторичная герметизация и заполнение инертным газом
Основа окна, к которой крепится стеклопакет, — профиль, который изготавливают из поливинилхлорида. При этом учитывают:
- устойчивость к температурным колебаниям,
- минимальные размеры переплета,
- способность выдерживать динамические и статические нагрузки и т.
д.
Оконный профиль
Как правило, компании приобретают готовый профиль, который используют при сборке окон. Если вас интересует, как делают профили для окон, видео, иллюстрирующее весь процесс, поможет вам вникнуть в детали.
Процедура изготовления профиля такова
На начальной стадии необходимо раскроить заготовки. При помощи мощной электрической пилы их разрезают под углом в 45 градусов. Так формируют основу окна — створки и рамы.
На следующем этапе происходит сварка. Оконную конструкцию фиксируют на специальном станке, нагревают до 250 градусов. Раскаленный профиль сжимают прессом на протяжении 20–30 секунд. Процедуру проделывают дважды — с обеих сторон. Когда прочность соединения достигнет нормы, можно перейти к удалению наплывов, которые образуются в процессе сварки. Все ненужные элементы зачищают при помощи углозачистной машины.
Следующий этап — создание импоста. Это своего рода «ребро жесткости», усиливающее сопротивляемость повышенным нагрузкам, ураганным ветрам и т. п. В нем просверливают отверстия для болтов и укрепляют их специальным герметиком. Такая технология обеспечивает максимальную прочность конструкции и минимизирует риски выпадения болтов. После завершения работ с импостом переходят к укладке резинового уплотнителя и установке фурнитуры — петли, запорные механизмы, блокираторы, цапфы, ручки и т. д.
Подкорректировав фурнитуру по заданным параметрам, можно переходить к креплению подоконника, а также к установке отлива (часть окна, которая выступает с его наружной стороны и отводит воду).
Вслед за этим необходимо соединить створки с оконным профилем
Стеклопакет крепится к профилю при помощи штапиков. Это своего рода фиксаторы, которые надежно удерживают стекло и не позволяют ему расшататься. Штапики и специальные колодки необходимо разместить по всему периметру оконной рамы. На заключительной стадии останется лишь поставить знаки качества, обернуть окна в пленку и подготовить их к транспортировке из цеха на склад, в точки продаж или непосредственно к конечному потребителю.
Опубликовано 05.03.2015
Читайте также:
ТЕХНОЛОГИЯ ПРОИЗВОДСТВА ОКОН И КОНСТРУКЦИЙ
Процесс производства пластиковых окон и конструкций достаточно сложен и технологичен. Завод оконных конструкций «ROMAX» — эталон уровня автоматизации производства не только в Поволжье, но и в России, что отмечается как российскими специалистами, так и ведущими зарубежными поставщиками комплектующих материалов к пластиковым изделиям. Производственные мощности завода «ROMAX» укомплектованы самыми современными автоматизированными линиями, которые сводят до минимума влияние человеческого фактора при производстве оконных конструкций.
Производство «ROMAX» — это
- 3 дня – срок изготовления стандартных конструкций даже в сезон
- 12-летний опыт работы с ПВХ-изделиями
- 300 единиц продукции за одну рабочую смену
- 4 000 кв.м. производственных площадей
Каждые 2,5 минуты с конвейера завода сходит одно готовое изделие, полностью соответствующее, а по многим параметрам превосходящее требования ГОСТа 30674-99 «Блоки оконные из поливинилхлоридных профилей».
Технологический процесс производства конструкций включает в себя несколько этапов.
I. ВХОДНОЙ КОНТРОЛЬ КОМПЛЕКТУЮЩИХ
Все комплектующие, попадая на завод «ROMAX», подвергаются тщательному контролю, при котором проверяется наличие сертификатов, паспортов и качество материалов, необходимых для изготовления конструкций. Система контроля качества комплектующих практически полностью исключает возможность поломки изделия в будущем при правильной его эксплуатации.
II. ИЗГОТОВЛЕНИЕ СТЕКЛОПАКЕТОВ
Стеклопакеты компании «ROMAX» изготавливаются на автоматизированной линии всемирно известной компании «LISEC» (Австрия). Автоматизация процесса раскроя стеклопакетов дает возможность соблюдать высочайшую точность размеров. В состав линии входит автоматическая станция разлома по осям X-Y-Z, с возможностью притупления кромки, мойки, автоматической сортировки нарезанного стекла и его подачи на дальнейшие технологические операции. Специальная моечная машина с особой тщательностью удаляет со стекла загрязнения любого рода.
Технические характеристики линии «LISEC»:
- Толщина стекла: 3 — 12 мм
- Минимальный размер нарезанного стекла: 350 х 350 мм
- Максимальный размер нарезанного стекла: 2400 х 1600 мм
На заводе «ROMAX» осуществляется переработка стекол со специальными возможностями: энергосберегающих, мультифункциональных, самоочищающихся и др. Работа со стеклами со спецпокрытиями возможна только на производствах с высокой культурой переработки, поскольку большинство покрытий требует деликатного отношения в процессе изготовления стеклопакетов. Полностью автоматизированная линия резки имеет возможность автоматического снятия мягкого низкоэмиссионного покрытия по периметру стекла. Стекла со спецпокрытиями маркируются наклейками для того, чтобы стеклопакет был установлен в конструкцию нужной стороной, поскольку от этого зависит эффективность работы данного покрытия. Также это является дополнительным способом защиты подлинности продукции завода. На этом же этапе осуществляется заполнение стеклопакета инертным газом аргоном, что способствует повышению теплофизических свойств будущего окна.
III. ОБРАБОТКА ПРОФИЛЯ
Обработка ПВХ-профиля на заводе осуществляется без участия человека на автоматических станках компании «SCHIRMER» (Германия). На модульных участках комплекса одновременно выполняются несколько операций:
- Распил ПВХ профилей
- Распил армирующего профиля и его соединение с профилем ПВХ
- Фрезерование торцов импостных профилей
- Сверление отверстий в створочных профилях под ручку
- Фрезерование сливных отверстий и отверстий под вентиляцию
- Обозначение координат расположения на профиле запорной фурнитуры
- Сортировка изготовленных деталей по конкретным заказам.
«SCHIRMER» управляется при помощи специально разработанной для завода «ROMAX» компьютерной программы. Производительность обрабатывающего центра – до 300 единиц продукции за одну рабочую смену.
Участок сварки-зачистки ПВХ-конструкций представлен тремя автоматическими сварочно-зачистительными линиями немецкой компании «ROTOX» (Германия). Уникальность данных агрегатов в том, что помимо одновременной сварки четырех углов периметра, здесь автоматически поддерживаются все технические параметры процесса, такие как температура поверхности нагревательных элементов, давление и время разогрева, давление и время стыковки, давление прижима, а также время охлаждения сварочных швов перед зачисткой. От соблюдения заданных производителем технических характеристик по сварке и зачистке зависит один из основных параметров окна — прочность сварных соединений. Участок сформирован из:
- Сварочных станков
- Зачистных агрегатов
- Передающих и накопительных станций
- Распределительных механизмов
- Участка сверления отверстий под петлевые группы
Агрегаты выполняют операции в соответствии с заданной компьютерной программой.
Линия установки фурнитуры состоит из трех независимых конвейерных линий компании «ROTOX», одна из которых створочная, а две другие – рамные. На участке осуществляется установка импостов, монтаж подставочного профиля, протяжка уплотнения (если требуется), монтаж запорной рамной фурнитуры. Линия установки створочной фурнитуры представлена тремя рабочими местами: на одном рубится в размер основной и средние запоры, на втором створка комплектуется необходимыми деталями, на третьем осуществляется их крепеж. На поточной конвейерной линии производится монтаж стеклопакетов в соответствующие изделия согласно предписываемым правилам раскрепления. Все рабочие места операторов, производящих механическую работу, оснащены мониторами и сканерами, с помощью которых, считывая нанесенный на конструкцию штрих-код, оператор получает команду на выполнение конкретной операции. Участок окончательной сборки представлен подвижным конвейером с тактовыми модулями, изменяющими потоки движения сборок.
Контрольный участок оборудован проверочным стендом, на котором осуществляется проверка функционирования фурнитуры. Представитель отдела технического контроля (ОТК) проверяет правильность сборки, работоспособность фурнитуры, отсутствие дефектов на ПВХ-профиле и стеклопакетах. Упаковка, в которой конструкции доставляются клиентам, снабжена стикером, свидетельствующим о том, что данное изделие прошло проверку в ОТК и полностью соответствует всем нормативам и стандартам качества, выработанным в оконной отрасли.
ГИБКА АРМИРОВАННОГО ПВХ-ПРОФИЛЯПолностью армированные арочные конструкции — визитная карточка и гордость завода «ROMAX». В 2012 году компания “ROMAX” ввела в эксплуатацию уникальное оборудование – станок для гибки алюминиевых и ПВХ профилей со стальным упрочнением производства ”TIM Machine” (Сербия), осуществляющий высокоточную гибку профилей минимального диаметра (от 370 мм.) при помощи лазера. Оборудование применяется для изготовления арочных конструкций, заполненных армированным профилем по всей длине изделия. Наличие армированного профиля в арочных конструкциях «ROMAX» существенно увеличивает их прочность и снижает вероятность повреждения при нагрузках. Армированные арочные конструкции не деформируются с течением времени и сохраняют свою жесткость при изменениях температурного режима.
Ламинация представляет собой процесс нанесения пленки на подготовленный белый или тонированный в массе ПВХ-профиль на специальном оборудовании. Плёнка приклеивается специальным клеем с помощью обжимных роликов, которые плотно прокатываются по всем поверхностям профиля, точно повторяя все его изгибы. При расплавлении клеевой слой образует с ламинационной пленкой единую структуру, обеспечивая максимально прочное соединение. Собственный ламинационный участок, организованный на заводе «ROMAX», позволяет быстро и качественно ламинировать оконные конструкции и аксессуары (подоконники, откосы). Широкая палитра ламинационной пленки немецкой компании Renolit позволит подобрать цвет окна в тон любого интерьера.
Похожие статьи
Вопрос: Подскажите, на какие параметры обращать внимание при выборе кухонного окна?
Ответ: Казалось бы, выбор кухонного окна- довольно простая задача. Но все же стоит подумать о том, что кухня- помещение с повышенной влажностью. При приготовлении пищи высока не только влажность, но и температура воздуха. Поэтому мой первый совет: заказать окно со всеми открывающими створками. В теплое время года будет возможность открыть створки, чтобы охладить и проветрить помещение. Также этот вариант существенно облегчает уход за окном- его легче мыть.
Миф 1. Пластиковые окна закупоривают проем и «не дышат»
Современные конструкции оборудованы качественной фурнитурой и уплотнительной резиной по периметру створки и рамы, исключающей проникновение сквозняка в помещение. Не привыкшему к такой герметичности пользователю первое время кажется, что в квартире стало душно. По сравнению со старыми деревянными рамами, которые «дышали» благодаря щелям и рассохшейся древесине, пластиковые окна действительно не пропускают воздух. Чтобы избежать духоты и обеспечить доступ свежего воздуха, необходимо не менее 2 раз в день проветривать комнату по 15 минут. Новые деревянные окна тоже не «дышат» естественным образом. Поверхность рамы обрабатывают специальными пропитками и лаками, через поры которых не проходит ветер. Изделия из дерева требуют ежедневного проветривания для комфортного микроклимата в помещении.
Миф 2. Окна из пластика неэкологичны
Распространено мнение, что пластиковые конструкции опасны для здоровья. Чаще всего покупатель реагирует на упоминание свинца в составе профиля ПВХ. Для жесткости, прочности, увеличения срока службы, красивого внешнего вида, надежной защиты от впитывания влаги в пластик добавляются различные стабилизаторы. Эти добавки могут быть на основе свинца или соединения кальция и цинка. Только в состав материала входит не сам свинец, а его соединение, что абсолютно не влияет на здоровье человека. Та же пищевая соль – это натрия хлорид. Если бы мы говорили о том, что соль состоит из хлора, стали бы мы употреблять ее в пищу? Но соединение разительно отличается от самого химического элемента. То же самое и с добавками в профиль. Безопасность пластика давно изучена и доказана. Из этого материала мы каждый день используем такие вещи как зубная щетка, очки, посуда. Детские бутылочки сделаны из пластика и даже в медицине без него не обойтись, те же сосуды для донорской крови выполнены из ПВХ.
Эффективное сохранение тепла и привлекательный вид окон все чаще становятся востребованными у жителей России. Производители предлагают изделия из ПВХ, стеклопластика, дерева и алюминия. Каждый вид окон имеет свои преимущества и недостатки. Сделать выбор окон необходимо с учетом типа помещения и особенностей климата. Однако и ценовые предпочтения играют определенную роль.
Технология изготовления пластиковых окон
20 Aug 2015 Время прочтения: 3 минуты
Производство пластикового окна начинается с выбора профиля. В отличие от деревянных окон, при изготовлении пластиковых окон используются не сплошные бруски, а полые многокамерные пластиковые профили, которые различаются конструктивно. Главное их отличие друг от друга это число воздушных камер. Таких камер в профилях может быть от двух до семи.
Производителям профили поставляются обыкновенно стандартной длины – 6 м, уложенными на палетах, и далее процесс изготовления окон осуществляется по следующей схеме.
Изготовление пластикового окна начинается с резки пластикового профиля.
Затем в профиль вставляется металлический усилитель, то есть производится его армирование, позволяющее упрочнить конструкцию и улучшить эксплуатационные качества окна.
На следующем этапе производства профили оконной рамы и створок свариваются между собой, образуя замкнутую раму или створку. Сварные швы обязательно тестируются на прочность и соответствие требованиям безопасности строительных стандартов.
Далее в раму и створки устанавливается уплотнитель, который помогает обеспечить одно из главных свойств пластикового окна — его герметичность.
На следующем этапе изготовления пластикового окна устанавливается оконная фурнитура, механизмы открывания и петли с запорами. Тут многое зависит от выбора клиента, помимо способа открывания створок (поворотный или поворотно-откидной), можно выбрать также дополнительные возможности окна. Это такие функции как микропроветривание, многоступенчатое проветривание, противовзломный запор, усиленный механизм запирания, усиленные петли.
После установки фурнитуры в окно вставляют стеклопакет, который удерживается в нем штапиками. Стеклопакеты могут быть обычными, одно- или двухкамерными, и с дополнительными возможностями, например, с повышенной теплоизоляцией, звукоизоляцией. Штапиками называются тонкие пластиковые профили, с помощью которых стеклопакет крепится в раме. Они вставляются в пазы профиля рамы со стороны помещения. Во время доставки и установки пластиковых окон стеклопакеты из рамы и створок вынимаются посредством извлечения как раз этих самых штапиков.
Вам будет это интересно
Технология производства окон ПВХ: как делают пластиковые окна
Компания «Орбита» является одним из лидеров по производству окон ПВХ в Республике Беларусь. На протяжении уже многих лет мы выпускаем изделия из поливинилхлорида, обладающие самыми высокими техническими характеристиками.
Качество наших оконных конструкций обеспечивается соблюдением всех технологических стандартов по ее производству. Для этого используется исключительно современное высокоточное профессиональное автоматическое оборудование для производства пластиковых окон. У нас установлены производственные линии от лучших мировых производителей оборудования для изготовления оконных систем, таких как FIMTEC, LISEC, URBAN, ROTOX, Haffner.
Производство окон ПВХ – сложный и многоступенчатый процесс, где качество конечного продукта контролируется и машинами, и человеком. Вся выполняемая работа на нашем предприятии максимально компьютеризирована и автоматизирована, что практически исключает влияние человеческого фактора. Также в производственном процессе участвуют только высококвалифицированные специалисты, что позволяет нам с уверенностью говорить о том, что мы производим действительно качественные окна.
Обзор технологии производства стеклопакетов.
Производство стеклопакетов в компании «Орбита» осуществляется на нескольких производственных зонах (участках).
- Участок заготовки, где проводится резка и мойка стекла, резка дистанционной рейки, заполнение влагопоглотителем внутреннего объема дистанционной рамки, сборка дистанционного контура, нанесение первичного слоя герметизации.
- Участок сборки, где между стекол наклеивается дистанционный контур и производится отжим стеклопакета для максимальной герметичности.
- Участок герметизации стеклопакета– на данном участке производства производится нанесение вторичного герметизирующего слоя на торец собранного стеклопакета.
- Участок контроля качества, где осуществляется визуальный контроль. После этого стеклопакеты сушатся в специальной пирамиде, конструкция которой обеспечивает свободную циркуляцию воздушных масс.
Более подробно о видах стеклопакетов Вы можете прочитать в разделе «Производство стеклопакетов».
Технология производства пластикового профиля.
Важным этапом производства оконных конструкций является изготовление пластикового профиля. Процесс изготовления пластикового профиля начинается с приготовления смеси. Используемые компоненты дозируются автоматически с помощью электронных весов. Это позволяет добиться предельной точности используемого состава. В состав смеси также включают различные модификаторы, стабилизаторы, красители и прочие добавки, отвечающие за надежность конечного продукта, его цвет, устойчивость к воздействию ультрафиолета и т. д.
Далее смесь загружают в бункер экструдера. Там смесь выдерживается определенное время, разогревается и выдавливается через фильеру.
При производстве пластиковых окон ПВХ компания «Орбита использует высококачественный пластиковый профиль Rehau.
Производство пластиковых окон: технологии производства.
Непосредственно технологический процесс производства пластиковых окон ПВХ (вне зависимости, используется ли однокамерный или многокамерный профиль) включает в себя последовательное выполнения ряда технологических операций, производимых на различных участках. Рассмотрим технологию производства пластиковых оконных конструкций подробнее.
Участок заготовки
На данном участке производятся следующие технологические операции:
- Нарезка оконного профиля по размерам, индивидуальным для каждого окна. Она происходит на пильном центре с ЧПУ с двумя управляемыми осями для автоматического раскроя ПВХ профиля, которая обеспечивает точное соответствие необходимым размерам.
- Нарезка армирующего профиля, необходимого для увеличения жесткости рамы окна. Армирующий профиль имеет длину на 10мм меньше, чем длина ПВХ-профиля.
- Далее заготовки поступают на обрабатывающий центр , который представляет собой СNС -обрабатывающий центр для полностью автоматизированного сверления и фрезерования по четырем осям. Производится изготовление водоотводящих и вентиляционных каналов, сверление под дюбели, фрезерование паза под замок и отверстия под цилиндр замка, сверление отверстий под ручку, маркировка запирающих деталей. Все требуемые виды обработки производятся на заготовке автоматически в соответствиии с заданными размерами, что полностью исключает влияние человеческого фактора.
- Установка и закрепление в заготовке ПВХ армирующего профиля согласно маркировке выполняется на автоматическом шуруповерте. Идентификация заготовок производится на основании считывания штрих-кода с этикеток на заготовках.
- Продувка сжатым воздухом заготовок профилей.
Мы предварительно проверяем все профили заготовок и защитные пленки на отсутствие повреждений, так как соблюдение всех норм при производстве пластиковых окон из ПВХ непосредственно влияет на качество готовой конструкции.
Участок сварки ПВХ профилей.
На данном участке происходит сварка профиля (створок и углов рамы), необходимая для создания конечной жесткой конструкции. Сварка ПВХ-профилей осуществляется при помощи роботизированных сварочных аппаратов. Мы используем 4-х головочный сварочный аппарат, который одновременно нагревает четыре среза профиля и сваривает их. На данном этапе производственной линии для соответствия технологическому процессу производства окон ПВХ строго соблюдаются следующие условия:
- температура сварного ножа должна составлять от 230°С до 250 °С;
- поверхность инструмента должна быть чистой, для этого каждый час тефлоновое покрытие ножа «на горячую» протирают бумажным или хлопковым полотенцем без использования растворителей;
- время на разогрев шва – 25-40 сек, на сварку – 25-40 сек.
Автоматизированная станция обработки сварочного шва гарантирует идеальное качество стыка профилей, что повышает надежность пластикового окна.
Участок зачистки углов
На данном участке происходит очистка стыков профиля от наплавов сварного шва. В компании «Орбита» при производстве окон ПВХ очистка сварного шва производится на специальном очистной станции. После зачистных работ и обязательного контроля качества изделия помещаются на стойки промежуточного хранения.
Участок установки импостов и уплотнительной резины
На данном этапе происходит присоединение горизонтальных и вертикальных импостов в соответствии со схемой производимой оконной системы. Для более точного прилегания импосты предварительно фрезеруются на фрезерном станке.
Уплотнение производится единым куском специальной резины, которая создает непрерывный уплотняющий контур. Осуществляется тщательный контроль, чтобы уплотнитель не растягивался. Стыки обрабатываются специальным клеем.
Участок установки фурнитуры
На данном участке производства пластикового окна осуществляется установка фурнитуры согласно бланку заказа. На станции установки фурнитуры не только монтируются ручки, петли и другие комплектующие, но также происходит соединение створки и рамы в единую конструкцию. После визуальной и функциональной проверки окно поступает на участок установки готовых стеклопакетов.
Участок установки стеклопакетов
Производство пластиковых окон завершается установкой стеклопакета в ПВХ-профиль. На специальном стенде производится окончательная регулировка створок. Стенд по установке стеклопакетов имитирует условия реального монтажа изделия в оконный проем. Далее стеклопакет закрепляется в пластиковом окне с помощью штапиков. Закрепление стеклопакета происходит согласно разработанной конструкторской документации. На этом этапе также проводится общий контроль качества изготовленной конструкции, после чего изделие отправляется на склад готовой продукции.
Преимущества производства окон в компании «Орбита»
Политика компании «Орбита» направлена на производство окон ПВХ исключительно высокого качества. Обращаясь к нам, вы можете быть уверенны в следующем:
- техническое оснащение (от электронной линейки и станков-штапикорезов до стендов для установки стеклопакетов) соответствует самым строгим требованиям и стандартам;
- огромные производственные площади и большая численность работников позволяют выполнить заказ любого объема предельно быстро;
- постоянное обучение новым технологиям и внедрение их в производство окон из профиля ПВХ позволяет выпускать продукцию европейского качества;
- жесткий контроль качества предотвращает попадание в продажу изделий даже с малейшим браком.
Окна ПВХ «Орбита» — совершенное изделие, качество и надежность которого обеспечивается точной работой машин и скрупулезным контролем со стороны человека.
Производство ПВХ профилей, пластиковых окон и дверей
Процесс производства пластиковых окон и конструкций достаточно сложен и технологичен. Завод оконных конструкций «ROMAX» — эталон уровня автоматизации производства не только в Поволжье, но и в России, что отмечается как российскими специалистами, так и ведущими зарубежными поставщиками комплектующих материалов к пластиковым изделиям. Производственные мощности завода «ROMAX» укомплектованы самыми современными автоматизированными линиями, которые сводят до минимума влияние человеческого фактора при производстве оконных конструкций. Новейшее оборудование позволило увеличить скорость изготовления пластиковых окон без ущерба качеству и вывело «ROMAX» на новый, высокотехнологичный уровень, невозможный при других способах организации производства. Сотрудниками компании «ROMAX» являются опытные специалисты, обученные всем тонкостям работы с производственным оборудованием. Работники завода регулярно повышают свою квалификацию, поскольку имеют дело с новинками оконной индустрии и сложнейшими технологическими процессами. Технология, применяемая при производстве продукции, полностью соответствует европейским стандартам, что позволяет изготавливать ПВХ-конструкции безупречного качества с расширенными функциональными возможностями.
Производство «ROMAX» — это
- 17-летний опыт работы с ПВХ-изделиями
- 300 единиц продукции за одну рабочую смену
- 1000 кв.м. ПВХ- конструкций в сутки
- 4 000 кв.м. производственных площадей
Каждые 2,5 минуты с конвейера завода сходит одно готовое изделие, полностью соответствующее, а по многим параметрам превосходящее требования ГОСТа 30674-99 «Блоки оконные из поливинилхлоридных профилей».
Технологический процесс производства конструкций включает в себя несколько этапов.
I. ВХОДНОЙ КОНТРОЛЬ КОМПЛЕКТУЮЩИХ
Все комплектующие, попадая на завод «ROMAX», подвергаются тщательному контролю, при котором проверяется наличие сертификатов, паспортов и качество материалов, необходимых для изготовления конструкций. Система контроля качества комплектующих практически полностью исключает возможность поломки изделия в будущем при правильной его эксплуатации.
II. ИЗГОТОВЛЕНИЕ СТЕКЛОПАКЕТОВ
- Фото Фото Фото
Стеклопакеты компании «ROMAX» изготавливаются на автоматизированной линии всемирно известной компании «LISEC» (Австрия). Автоматизация процесса раскроя стеклопакетов дает возможность соблюдать высочайшую точность размеров. В состав линии входит автоматическая станция разлома по осям X-Y-Z, с возможностью притупления кромки, мойки, автоматической сортировки нарезанного стекла и его подачи на дальнейшие технологические операции. Специальная моечная машина с особой тщательностью удаляет со стекла загрязнения любого рода.
Технические характеристики линии «LISEC»:
- Толщина стекла: 3 — 12 мм
- Минимальный размер нарезанного стекла: 350 х 350 мм
- Максимальный размер нарезанного стекла: 2400 х 1600 мм
На заводе «ROMAX» осуществляется переработка стекол со специальными возможностями: энергосберегающих, мультифункциональных, самоочищающихся и др. Работа со стеклами со спецпокрытиями возможна только на производствах с высокой культурой переработки, поскольку большинство покрытий требует деликатного отношения в процессе изготовления стеклопакетов. Полностью автоматизированная линия резки имеет возможность автоматического снятия мягкого низкоэмиссионного покрытия по периметру стекла. Стекла со спецпокрытиями маркируются наклейками для того, чтобы стеклопакет был установлен в конструкцию нужной стороной, поскольку от этого зависит эффективность работы данного покрытия. Также это является дополнительным способом защиты подлинности продукции завода. На этом же этапе осуществляется заполнение стеклопакета инертным газом аргоном, что способствует повышению теплофизических свойств будущего окна. В конструкции «ROMAX» по желанию заказчика могут быть установлены стекла-триплекс, бронированные стекла, стекла с декоративным переплетом. Герметизация стеклопакетов осуществляется с применением герметиков IGK.
III.
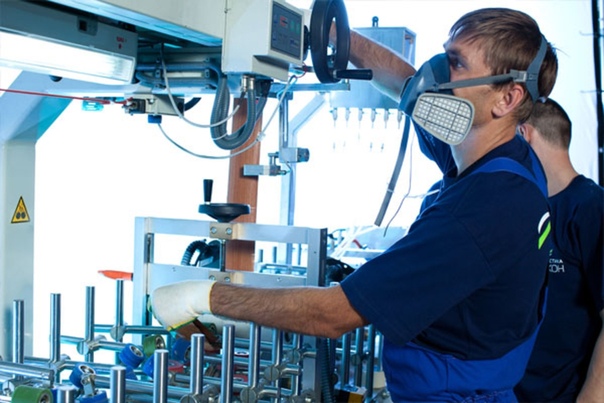
- Фото Фото Фото
Обработка ПВХ-профиля на заводе осуществляется без участия человека на автоматических станках компании «SCHIRMER» (Германия). На модульных участках комплекса одновременно выполняются несколько операций:
- Распил ПВХ профилей
- Распил армирующего профиля и его соединение с профилем ПВХ
- Фрезерование торцов импостных профилей
- Сверление отверстий в створочных профилях под ручку
- Фрезерование сливных отверстий и отверстий под вентиляцию
- Обозначение координат расположения на профиле запорной фурнитуры
- Сортировка изготовленных деталей по конкретным заказам.
«SCHIRMER» управляется при помощи специально разработанной для завода «ROMAX» компьютерной программы. Производительность обрабатывающего центра – до 300 единиц продукции за одну рабочую смену.
IV. СВАРКА И ЗАЧИСТКА
Участок сварки-зачистки ПВХ-конструкций представлен тремя автоматическими сварочно-зачистительными линиями немецкой компании «ROTOX» (Германия). Уникальность данных агрегатов в том, что помимо одновременной сварки четырех углов периметра, здесь автоматически поддерживаются все технические параметры процесса, такие как температура поверхности нагревательных элементов, давление и время разогрева, давление и время стыковки, давление прижима, а также время охлаждения сварочных швов перед зачисткой. От соблюдения заданных производителем технических характеристик по сварке и зачистке зависит один из основных параметров окна — прочность сварных соединений. Участок сформирован из:
- Сварочных станков
- Зачистных агрегатов
- Передающих и накопительных станций
- Распределительных механизмов
- Участка сверления отверстий под петлевые группы
Агрегаты выполняют операции в соответствии с заданной компьютерной программой.
V. УСТАНОВКА ИМПОСТОВ, ФУРНИТУРЫ И МОНТАЖ СТЕКЛОПАКЕТОВ. ОКОНЧАТЕЛЬНАЯ СБОРКА КОНСТРУКЦИЙ.
Линия установки фурнитуры состоит из трех независимых конвейерных линий компании «ROTOX», одна из которых створочная, а две другие – рамные. На участке осуществляется установка импостов, монтаж подставочного профиля, протяжка уплотнения (если требуется), монтаж запорной рамной фурнитуры. Линия установки створочной фурнитуры представлена тремя рабочими местами: на одном рубится в размер основной и средние запоры, на втором створка комплектуется необходимыми деталями, на третьем осуществляется их крепеж. На поточной конвейерной линии производится монтаж стеклопакетов в соответствующие изделия согласно предписываемым правилам раскрепления. Все рабочие места операторов, производящих механическую работу, оснащены мониторами и сканерами, с помощью которых, считывая нанесенный на конструкцию штрих-код, оператор получает команду на выполнение конкретной операции. Участок окончательной сборки представлен подвижным конвейером с тактовыми модулями, изменяющими потоки движения сборок.
VI. ВЫХОДНОЙ КОНТРОЛЬ КАЧЕСТВА ИЗДЕЛИЙ
Контрольный участок оборудован проверочным стендом, на котором осуществляется проверка функционирования фурнитуры. Представитель отдела технического контроля (ОТК) проверяет правильность сборки, работоспособность фурнитуры, отсутствие дефектов на ПВХ-профиле и стеклопакетах. Упаковка, в которой конструкции доставляются клиентам, снабжена стикером, свидетельствующим о том, что данное изделие прошло проверку в ОТК и полностью соответствует всем нормативам и стандартам качества, выработанным в оконной отрасли.
ГИБКА АРМИРОВАННОГО ПВХ-ПРОФИЛЯ
- Фото Фото Фото
Полностью армированные арочные конструкции — визитная карточка и гордость завода «ROMAX». В 2012 году компания “ROMAX” ввела в эксплуатацию уникальное оборудование – станок для гибки алюминиевых и ПВХ профилей со стальным упрочнением производства ”TIM Machine” (Сербия), осуществляющий высокоточную гибку профилей минимального диаметра (от 370 мм.) при помощи лазера. Оборудование применяется для изготовления арочных конструкций, заполненных армированным профилем по всей длине изделия. Наличие армированного профиля в арочных конструкциях «ROMAX» существенно увеличивает их прочность и снижает вероятность повреждения при нагрузках. Армированные арочные конструкции не деформируются с течением времени и сохраняют свою жесткость при изменениях температурного режима.
ЛАМИНАЦИЯ ПВХ-ПРОФИЛЯ
- Фото Фото Фото
Ламинация представляет собой процесс нанесения пленки на подготовленный белый или тонированный в массе ПВХ-профиль на специальном оборудовании. Плёнка приклеивается специальным клеем с помощью обжимных роликов, которые плотно прокатываются по всем поверхностям профиля, точно повторяя все его изгибы. При расплавлении клеевой слой образует с ламинационной пленкой единую структуру, обеспечивая максимально прочное соединение. Собственный ламинационный участок, организованный на заводе «ROMAX», позволяет быстро и качественно ламинировать оконные конструкции и аксессуары (подоконники, откосы). Широкая палитра ламинационной пленки немецкой компании Renolit позволит подобрать цвет окна в тон любого интерьера.
Оборудование для производства пластиковых окон: станок, линия, технология и процесс
Технологически процесс производства пластиковых окон не представляет собой особенной сложности и заключается в нарезке всех нужных составляющих, ликвидации лишних компонентов, подготовке вспомогательных деталей и их монтаже.
Основное требование при изготовлении окон – это точное следование технологии и качество. Технологический процесс проходит в несколько этапов, для каждого из которых необходимо собственное оснащение.
Намереваясь создать цех по производству пластиковых окон, нужно приобретать оборудование для изготовления пластиковых окон в полном комплекте. В противном случае не удастся производить конкурентоспособную продукцию.
Технологическое оснащение для изготовления пластиковых окон
Наиболее часто используется в данном производстве станок для резки профиля, который в каталогах еще называется пилой. Часть таких станков имеет дополнительное оснащение, повышающее его производительность.
Такие станки делятся по виду подачи пильного диска. Она бывает нижняя, лобовая и осуществляемая сверху. Вид подачи в комбинации с размером пильного диска обеспечивают максимально возможные величины распила, которые можно увидеть на графике реза. На ней стоит акцентировать свое внимание, если предполагается использование крупной профильной системы или одномоментный распил двух профилей.
Пилы могут иметь одну головку и две. В первом случае величины выставляется специалистом собственноручно посредством роликового конвейера с измерителем. В другом случае размер может выставляться таким же способом, но посредством дополнительных электронных комплектующих (табло и верньера) или целиком автоматически.
Хотите выгодный бизнес но с меньшими затратами средств? Тогда узнайте, какое оборудование для шиномонтажа потребуется и как осуществляется этот процесс.
Воспользовавшись ссылкой, Вы сможете узнать всё о технологии производства керамической плитки.
Сварочные станки
Производственный цикл сварки состоит из нескольких этапов:
- монтажа заготовок;
- нагрева свариваемых поверхностей;
- сжатия;
- остужения сварного шва.
Различие таких станков состоит в числе углов, которые свариваются в одно и тоже время. Их может быть от одного до четырех. Некоторые станки имеют изменяемый угол сварки, поэтому на них можно производить необычные конструкции. Выбор такого оборудования определяется масштабами предприятия.
Автоматические зачистные станки
Они удаляют наплав на наружных поверхностях и оберегают лицевой угол заготовки. Вместе с ними в комплект входит система автоматического включения производственного цикла в процессе установки заготовки.
Данное оборудование позволяет автоматически выбирать подходящую фрезу для створки или рамы. Если предполагается работать исключительно с одним профилем, можно делать это посредством станка на две фрезы. Его стоимость ниже, но он имеет незначительные перспективы, потому что на работе с единственным профилем почти никто не останавливается.
Лучше приобрести станок на четыре фрезы. Его стоимость выше, но на нем можно обрабатывать уже два профиля. Еще более перспективный станок на шесть фрез, так как он позволяет работать с несколькими профилями. Еще выше уровнем считается станок для зачистки с ЧПУ.
Он разительно отличается от других автоматов тем, что способен обрабатывать десятки профилей без специального оснащения, зачищает криволинейные наружные отрезки и фрезерует паз для монтирования уплотнителя.
Автоматы для фрезерования торца импоста
Они могут быть как механическими, так и автоматическими, а также иметь одну или две фрезы. Принцип выбора такого оборудования не отличается от выбора зачистных станков.
Станки для резки укрепляющих стекла реек
Штапик – это единственный компонент окна, при производстве которого не задаются размеры, потому что при нарезке других оконных деталей, их заготовки после сварки могут незначительно отклоняться от размеров, которые были заданы.
Это не будет существенным образом влиять на их эксплуатацию, в отличие от одинаковых реек, сделанных в соответствии с величиной, заданной по проекту и служащих для укрепления стекол в каркасе окна. В последнем случае при их монтаже вверху появляется чрезмерное напряжение, а внизу – щель.
Поэтому станки позволяют резать каждый конкретный штапик по существующим, а не заданным замерам. Это достигается тем, что оборудование оснащается специальным съемным измерительным элементом.
Качество работы стандартных станков и оборудования с ЧПУ практически не отличается.
Фрезерные станки для водосливных отверстий
Это оборудование отличается видом двигателей, которые могут быть простые или с частотным управлением, а также по числу операций, которые они могут выполнять. Если производство скромное, для него может подойти фрезерный станок с простыми двигателями, а если выпускаются большие объемы продукции, желательно, чтобы оборудование было с более сложными двигателями.
Станок с двумя фрезами дает возможность сделать отверстия для слива воды на внешней поверхности рамы. Если у прибора три фрезы, его возможности увеличиваются. Он позволяет сделать отверстия не только на лицевой поверхности, но и на нижней внутренней стороне.
Его лучше всего использовать при производстве специального подставочного профиля, подоконник к которому прилегает изнутри, а снаружи присоединяется металлический слив. Копировально-фрезерный станок Он используется для проделывания специальных пазов и отверстий, например, под личинку замка.
Функционирует по принципу регулирования передвижением задействованной фрезы посредством шаблона из стали с предварительно проделанными отверстиями необходимой формы. Бывают аналогичные станки с дополнительными функциями, например, высверливание отверстий под ручку окна или фрезерование каналов, которые отводят воду.
Есть автоматические станки, которые выполняют почти все эти функции одновременно. Такое оборудование существенно упрощает и ускоряет обработку.
Станок тройного сверления отверстий под оконную ручку
Этот станок для изготовления пластиковых окон требуется для проделывания отверстия не только в пластике, но и в армирующем усилителе, который сделан из стали. Станок тройного сверления имеет мощный двигатель и редуктор для того, чтобы можно было в одно и то же время вращать три сверла, меняя их диаметр — с мелкого на крупный, чтобы облегчить процесс сверления. Компрессор Выбирая компрессор, важно учесть, что основная масса производителей пластиковых окон используют поршневые компрессорные установки, так как они имеют множество плюсов по сравнению с винтовыми:
- эффективнее функционируют в повторно-кратковременном режиме;
- легче адаптируются к температурным изменениям;
- легко ремонтируются;
- имеют длительный срок эксплуатации;
- стоят сравнительно недорого.
Перед приобретением компрессора необходимо рассчитать совокупный объем потребления кислорода всей производственной линией и выяснить рабочее давление. Производительность системы должна быть на четверть выше общего объема потребляемого воздуха, причем ресивер нужно выбирать с таким расчетом, чтобы не вызвать резких колебаний давления.
Использование понижающего редуктора на выходе из ресивера даст возможность получить в системе постоянное давление.
Стенд остекления
Это устройство с широким спектром применения, которое представляет собой прочную стальную конструкцию с монтажным столом, предназначенным для установки на элементы окна фурнитуры, ролет и дополнительных профилей. Такой стол позволяет быстро и безопасно ставить их вертикально для дальнейшего транспортирования.
Какое дополнительное оборудование может понадобиться для производства пластиковых окон?
- ручной инструментарий;
- рабочие столы для монтажа
- мебель для складирования и тележки для перемещения по цеху сырья и продукции;
- стенд для стеклопакетов.
Правильно подобранное оборудование для изготовления ключей даст возможность открыть прибыльный бизнес очень быстро и с небольшими затратами. Узнайте как это сделать.
Перейдя по ссылке Вы сможете узнать, как производят тротуарную плитку и какие установки для этого применяются.
Каждый из нас пользуется туалетной бумагой. Но как же её получают? Узнаете здесь: http://buisiness-oborudovanie.com/dlya-bumazhnyx-izdelij/oborudovanie-dlya-proizvodstva-tualetnoj-bumagi/.
Автоматическая линия по производству пластиковых окон — это современное оборудование, которое дает возможность на автомате сваривать и зачищать сварные швы пластиковых окон. Оно позволяет предприятию обеспечить высокую производительность и имеет целый ряд преимуществ:
- высокое качество зачистки оконных углов;
- высокотехнологичное производство;
- короткое время изготовления;
- возможность спланировать изготовление пластиковых окон
- обслуживание линии одним специалистом;
- высокое качество готовой продукции.
Технология производства пластиковых окон
Пластиковые окна делаются из поливинилхлорида, признанного наиболее который признан наиболее подходящим для этой цели. Производственная технология изготовления пластикового окна у всех производителей примерно одинакова, но особенности могут немного отличатся. Однако процесс изготовления пластиковых окон имеет один алгоритм.
Материал, из которого делают пластиковые окна, делается из каменной соли и природного газа. Потом он гранулируется, обрабатывается и смешивается с необходимыми добавками. Расплавленный поливинилхлорид заливается в форму, высыхает и шлифуется. Так изготавливается оконный профиль.
Металлический профиль армирования режется перпендикулярно, в соответствии с техническим заданием. Необходимая длина заготовки рассчитывается посредством специализированного программного обеспечения.
На следующем этапе режутся заготовки ПВХ профиля. Профили импостов и дополнительных профилей режутся под прямым углом, профили рам и створок – под 45? с обеих сторон заготовки. Затем заготовки профиля и арматуру разрезают на необходимую длину, фрезеруют дренажные отверстия, пазы и отверстия под фурнитуру.
Заготовки импоста обрабатываются на специальном станке с обеих сторон фасонной фрезой, очертание фрезерования должно соответствовать конфигурации рамы. Для фиксации импоста в раме, внутрь импоста монтируются механические соединители.
Фасонная фреза, которой обрабатывается импост, входит в технологическое оснащение, которое предоставляет поставщик профиля. Так как в процессе сварки длина профиля становится короче, размер заготовки должен превышать «рабочую» величину оконной конструкции.
Качество нарезанных заготовок определят качество сварки. Потом отрезки профиля свариваются, и в окно монтируется запорная регулируемая фурнитура, и его остекляют. Затем конструкцию ставят я на специальный стенд, где осуществляется проверка на наличие брака и дефектов.
Желательно, чтобы при хранении пвх профиля, он не подвергался воздействию ультрафиолетового излучения и отопительных приборов. Если он содержится в холодное время года в помещении, которое не отапливается, перед тем, как начинать обработку его следует прогреть до температуры не менее 17 ?.
Как это сделать? Достаточно занести его в отапливаемое помещение примерно за 24 часа до того, как начнется обработка. Соответственно и температура в цехе должна быть выше 17?, в противном случае при резке и зачистке профиля могут появиться сколы.
Все производственное оборудование должно проходить плановое техническое обслуживание.
Модели оборудования, применяемые для изготовления пластиковых пвх окон
Одним из самых популярных производителей оснащения для выпуска окон — фирма «Yilmaz». Эта турецкая марка предлагает наиболее полный ассортимент станков для обработки профилей. Перечень выпускаемого оборудования настолько широк, что позволяет организовать как маленькое производственное помещения для изготовления нестандартных пластиковых окон, так и оснастить современное масштабное предприятие.
Например, модель «ACK-420″ — Пила для резки с нижней подачей диска. Она имеет пневматические прижимы, которые настраиваются. Они служат для точной фиксации профиля. Крупный диаметр пильного диска и упоры, которые можно передвигать, позволяют резать профиль больших размеров.
Оборудование “MURAT” турецкого производства не менее популярно на потребительском рынке. Оно отличается надежностью и легкостью в эксплуатации. Перечень производимого компанией оснащения довольно широк, что позволяет подобрать оптимальный набор станков для любого предприятия, выпускающего различные виды профилей.
Модель TA-141 — автоматическая пила с нижней подачей диска от данного производителя предназначена для резки ПВХ профилей и профилей из алюминия. Автомат имеет поворотную основу, позволяющую менять угол раскроя в широком диапазоне. Специальный регулятор подачи пильного диска позволяет минимизировать нагрузку на электрический двигатель.
Видео про изготовление пластиковых окон
Republished by Blog Post Promoter
Окно косметического процесса: ключ к надежному процессу без дополнительных настроек
Вы только что закончили формовку деталей из инструмента, подвешенного в прессе сегодня утром, и отправили первые снимки инспектору по качеству для проверки размеров. Что в первую очередь собирается сделать инспектор? Собирается ли она взять суппорт и сразу же приступить к измерению деталей, или она собирается сначала осмотреть детали на предмет каких-либо косметических дефектов? Если детали короткие или у них есть вспышка, нет никаких шансов убедить инспектора измерить детали.
Как насчет другого сценария: вы хотите вести машину в режиме круиз-контроля со скоростью 80 миль в час в течение 4 часов подряд. Если бы у вас был выбор между узкой извилистой дорогой на краю обрыва и прямой дорогой с широкой полосой движения, что бы вы выбрали? Ответ очевиден! Если вы выберете дорогу по краю обрыва, очень вероятно, что в какой-то момент вы упадете со скалы. Даже если вам удастся завершить это путешествие, это не значит, что вы добьетесь успеха в будущих путешествиях. Также важно: путешествие по утесу — это напряженный процесс.Вы должны постоянно следить за дорогой, не допускать отклонений от настроек. Вы никогда не сможете оторвать глаз от дороги и придется постоянно следить за поездкой.
Так же, как движение на машине со скоростью 80 миль в час по краю обрыва в течение 5 минут не гарантирует, что вы сможете сделать это в течение 4 часов и всех будущих поездок. Точно так же успешное формование 10 деталей и предположение, что вы сможете запустить 100000 деталей без проблем, также является мифом.
В области литья под давлением мы часто оказываемся в подобных ситуациях.Если детали короткие при давлении упаковки и удержания 3750 фунтов на квадратный дюйм (пластик) и косметически приемлемые при 4000 фунтов на квадратный дюйм, но мигают при 4500 фунтов на квадратный дюйм, окно для формования деталей с приемлемой косметикой очень мало. Окно, внутри которого могут быть отформованы косметически приемлемые детали, определяется как окно косметического процесса (CPW). В этом случае, если работа представляет собой недельный выпуск 100 000 деталей, очень высока вероятность формования коротких кадров или деталей со вспышкой. Частота проверки деталей должна быть выше.
К сожалению, «100% проверка» встречается чаще, чем мы думаем. Процессы с меньшими косметическими окнами требуют постоянного внимания инженеров-технологов, что эквивалентно вождению автомобиля со скоростью 80 миль в час по краю обрыва. Подобно тому, как вождение автомобиля со скоростью 80 миль в час по краю обрыва в течение 5 минут не гарантирует, что вы сможете сделать это в течение 4 часов, и все будущие поездки, точно так же успешное формование 10 деталей и предположение, что вы затем сможете запустить 100000 деталей без проблем, также миф. Мы должны понимать краткосрочные вариации и долгосрочные сдвиги. Процесс формования должен быть достаточно надежным, чтобы улавливать эти вариации и сдвиги.
На рис. 1 показаны детали одного и того же инструмента, отформованные при трех разных давлениях упаковки и удержания, в результате чего получаются детали, короткие с раковиной, приемлемые с косметической точки зрения или имеющие заусенец. Давления, упомянутые в этой статье, являются значениями пластического давления (а не гидравлического давления). Исследование окна процесса было проведено при температурах расплава 480 F и 520 F — высоких и низких, рекомендованных техническими данными для этого АБС.При 480 F детали, формованные под давлением ниже 4000 фунтов на квадратный дюйм, приводили к коротким замыканиям и раковинам, а детали, формованные под давлением более 10000 фунтов на квадратный дюйм, давали детали с заусенцев. Детали, отформованные под давлением от 4000 до 10000 фунтов на квадратный дюйм (включительно), давали детали без проседания, вспышки или коротких выстрелов. То же исследование было повторено при 520 F, и пределы давления оказались равными 3000 и 9000 фунтов на квадратный дюйм. Эти четыре точки данных образуют окно косметического процесса (CPW). Детали, отформованные в CPW, косметически приемлемы (рис. 2). Мы не учитываем размеры при проведении этого исследования.
Если вернуться к аналогии с выбором дороги для движения и взглянуть на CPW, становится ясно, что при выборе условий формования будет центр окна. В этом случае это приводит к температуре расплава 500 F и давлению 6500 фунтов на квадратный дюйм. Установка процесса в этих условиях и наличие широкого технологического окна гарантирует, что формованные детали всегда будут косметически приемлемыми. Любые естественные вариации и сдвиги в этих настройках будут смягчены и не потребуют настройки инженером-технологом. Широкое окно процесса — ключ к надежности процесса.
Только после того, как это исследование будет выполнено, формовщик должен посмотреть на размеры детали. Размеры деталей являются функцией усадки, которая основана на соотношении давление-объем-температура (PVT) для данного пластика.Усадка здесь связана с объемом, и поэтому данный объем зависит от давления и температуры. Таким образом, давление упаковки и удержания, а также температура плавления и / или пресс-формы являются основными факторами, влияющими на размеры детали. Есть несколько других факторов, влияющих на размеры, которые будут обсуждены в следующей статье. Для оценки размеров используется метод планирования экспериментов (DOE). Во время выполнения DOE детали формуются по четырем углам, а размеры наносятся в виде контурных диаграмм внутри вписанного прямоугольного окна.
На рис. 3 диаметр колеса, рассматриваемого для исследования CPW, показан на основе результатов DOE. Номинальное значение составляет 1,685 дюйма с допуском 0,006 дюйма на нижней стороне и 0,009 дюйма на верхней стороне. Внешний блок — это CPW, а внутренний блок, нарисованный на основе зеленых контуров, — это окно размерного процесса (DPW).Сплошная зеленая линия — это номинальное значение, и щелчок в любом месте линии даст комбинацию настроек давления упаковки и удержания и температуры плавления для производства деталей с номинальным значением. Для DPW минимальные и максимальные значения давления составляют 4250 и 7250 фунтов на квадратный дюйм и 480 F и 520 F для температуры. Центр окна составляет 5750 фунтов на квадратный дюйм и 500 F. Формовка в центре окна снова дает нам надежный процесс, поскольку по обе стороны от этого параметра есть много места для любых изменений и сдвигов.
Теперь рассмотрим ту же форму, но с гипотетически маленьким окном косметического процесса. Используемые температуры и низкое давление 4000 фунтов на квадратный дюйм остаются такими же, но форма начинает вспыхивать при 5000 фунтов на квадратный дюйм (рис. 4). Поскольку DPW является подмножеством CPW, DPW теперь очень мал с точки зрения давления (рис. 5). Центр будет составлять 4500 фунтов на квадратный дюйм, и мы могли бы формовать приемлемые детали в течение короткого времени, но в течение недели — из-за естественных изменений в машине, материале, окружающей среде (включая персонал) — весьма вероятно, что детали могут быть формованные, короткие, не соответствующие спецификации на нижней стороне или имеющие вспышку.Если детали приемлемы с косметической точки зрения, но имеют размеры ниже нижнего предела спецификации, увеличение давления может вызвать вспышку. Мы снова едем на машине по краю обрыва, и теперь требуется 100% осмотр.
Таким образом, приведенное выше обсуждение требует широкого DPW для надежного процесса.Поскольку DPW является подмножеством CPW, CPW также должен быть широким. Естественное изменение будет смягчено в процессе производства. Со временем компоненты пресс-формы изнашиваются, ворота изнашиваются, вентиляционные отверстия начинают раздавливаться, партии материалов будут меняться, а качество деталей может измениться. Результаты, полученные от DOE, позволят вам принимать решения на основе данных об изменении процесса и при этом формовать детали в соответствии со спецификациями.
Рис. 5. Узкое окно технологического процесса является результатом узкого окна косметического процесса.
Таким образом, именно область CPW является критическим первым шагом к достижению надежного процесса, нулевого дефекта, сокращенного контроля и отсутствия настройки процесса.
ОБ АВТОРЕ: Сухас Кулкарни — президент компании Fimmtech Inc., специализирующейся на услугах и обучении, связанных с литьем пластмасс под давлением. Он получил степень магистра в области пластической инженерии в Массачусетском университете в Лоуэлле, а также степень бакалавра в области полимерной инженерии в Университете Пуны, Индия.Он имеет 27-летний опыт работы в качестве инженера-технолога и является автором книги Robust Process Development and Scientific Molding, , опубликованной Hanser Publications, теперь во втором издании. Он также работает штатным преподавателем в Университете Массачусетса-Лоуэлл. Контакты: [email protected] ; fimmtech.com .
Руководство по производственным процессам для пластмасс
Ротационное формование (также называемое ротационным формованием) — это процесс, который включает нагрев полой формы, заполненной порошкообразным термопластом и вращающейся вокруг двух осей для производства в основном больших полых объектов. Также доступны процессы центробежного формования термореактивных пластиков, но они менее распространены.
- Зарядка: Порошок пластика загружается в полость формы, а затем устанавливаются остальные части формы, закрывая полость для нагрева.
- Нагрев: Форму нагревают до тех пор, пока пластиковый порошок не расплавится и не прилипнет к стенкам формы, при этом форма вращается вдоль двух перпендикулярных осей, чтобы обеспечить однородное пластиковое покрытие.
- Охлаждение: Форма медленно охлаждается, в то время как форма остается в движении, чтобы гарантировать, что оболочка детали не провиснет или не разрушится до полного затвердевания.
- Удаление детали: Деталь отделяется от формы, любые высечки удаляются.
Ротационное формование требует менее дорогостоящего инструмента, чем другие методы формования, поскольку в процессе для заполнения формы используется центробежная сила, а не давление. Формы могут быть изготовлены, обработаны на станке с ЧПУ, отлиты или сформированы из эпоксидной смолы или алюминия с меньшими затратами и намного быстрее, чем инструменты для других процессов формования, особенно для крупных деталей.
Ротационное формование позволяет получать детали с почти одинаковой толщиной стенок.После того, как инструменты и процесс настроены, стоимость детали очень низкая по сравнению с размером детали. Также в форму можно добавлять готовые детали, такие как металлическая резьба, внутренние трубы и конструкции.
Эти факторы делают ротационное формование идеальным для мелкосерийного производства или в качестве альтернативы выдувному формованию для небольших объемов. Типичные изделия, изготовленные методом роторного формования, включают резервуары, буи, большие контейнеры, игрушки, шлемы и корпуса каноэ.
Ротомолдинг имеет некоторые конструктивные ограничения, а готовая продукция имеет более низкие допуски.Поскольку вся пресс-форма должна быть нагрета и охлаждена, процесс также имеет длительное время цикла и является довольно трудоемким, что ограничивает его эффективность для приложений с большими объемами.
Наиболее распространенным материалом для ротационного формования является полиэтилен (ПЭ), который используется в 80% случаев, в основном потому, что ПЭ можно легко измельчить в порошок при комнатной температуре.
Обычно ротационные пластмассы включают:
- Полиэтилен
- Полипропилен
- Поливинилхлорид
- Нейлон
- Поликарбонат
Для достижения стабильного качества формованных деталей с хорошей эстетикой и размерами разработан эксперимент, который представляет собой систематическое исследование влияния переменных на качество часть должна быть проведена.Они традиционно используются при литье под давлением для определения параметров процесса для достижения устойчивости производственного цикла. Это дает огромные преимущества. Всегда желательно большое окно процесса, чтобы уменьшить вероятность дефекта.![]() • Исследование реологии или вязкости: Вязкость остается довольно постоянной при более высоких скоростях впрыска. Изменения скорости впрыска не должны сильно влиять на вязкость, обеспечивая равномерное наполнение. • Весы для полостей: Сбалансированное заполнение между полостями обеспечивает одинаковое количество материала, упакованного в полости, что обеспечивает однородность между полостями. • Исследование падения давления: Исследование падения давления проводится для того, чтобы убедиться, что винт имеет достаточное давление для движения с заданной скоростью. ![]() • Исследование окна процесса: Исследование окна процесса выполняется для определения границ, между которыми можно отливать эстетически приемлемые детали. Обычно двумя переменными являются давление выдержки и температура плавления или формы.Центральное давление является наиболее желательным для компенсации естественных колебаний удерживающего давления • Исследование уплотнения затвора: По мере того, как пластик заполняет форму через затвор, скорость уменьшается, расплав остывает, и в конечном итоге затвор замерзает. Давление на винт необходимо прикладывать до тех пор, пока шибер не замерзнет, чтобы поддерживать давление в полости и постоянство веса детали. Время выдержки, при котором вес детали постоянен, выбирается в качестве установленного времени выдержки, опять же, чтобы гарантировать постоянство. ![]() • Исследование времени охлаждения: Исследование времени охлаждения выполняется, чтобы определить, насколько быстро деталь может быть отформована без деформации или каких-либо других проблем. Поскольку детали доступны, можно построить график важных размеров в зависимости от времени охлаждения. Как правило, для аморфных полимеров исследование должно проводиться при выдерживании давления при различных температурах расплава, тогда как исследование выдерживания давления при различных температурах формы следует проводить для кристаллических полимеров.Надежный процесс — это процесс, который задается в центре этого окна, что гарантирует, что естественное изменение процесса по-прежнему приведет к приемлемым частям. Приведенная выше техника обеспечивает эстетическое восприятие детали. Центр окна был бы идеальным процессом, если бы детали, отформованные в этих условиях, имели номинальные размеры и если бы верхний предел спецификации (USL) и нижний предел спецификации (LSL) содержались внутри этого окна. ![]() Затем следует изучить влияние обоих параметров обработки на размеры детали.Для проведения такого исследования может быть использована методика планирования экспериментов (DOE). Выходные данные DOE включают в себя контурные графики размеров, линии, которые описывают условия процесса для достижения определенного размера. Исследования DOE должны проводиться в четырех углах технологического окна, где детали эстетически приемлемы. Эту концепцию можно расширить и включить в DPW возможности процесса. Пределы контроля могут быть установлены в зависимости от процесса и размеров.Это называется окном процесса управления (CPW), которое учитывает все естественные отклонения и предоставляет рабочие окна. Наложение нескольких размеров на это окно делает фактическое рабочее окно еще меньше. Пределы сигналов тревоги — это границы, которые устанавливаются на выходе процесса формования, тогда как допуски — это те, которые устанавливаются в настройках процесса. Эту концепцию можно применить и к другим выходным данным, таким как давление в полости, что является окончательным и наиболее эффективным способом измерения качества детали. ![]() • От кадра к кадру • Полость к полости • Операция переходит в другую серию Формованные детали во всех этих вариантах должны быть одинакового качества. Пять наиболее важных параметров, определяющих качество литых деталей: • Дизайн детали • Материал • Станок • Форма • Процесс • Качество детали Процесс формования — один из пяти факторов, влияющих на качество литых деталей. ![]() Широкие технологические окна дают возможность успешно выполнять операции формования. Некоторые утверждают, что окно становится все меньше и меньше по мере увеличения количества размеров и полостей. К сожалению, это реальность, хотя это была скрытая правда.Это основная причина, по которой у большинства компаний есть только один утвержденный технологический лист. Пределы сигналов тревоги и допуски обычно устанавливаются на основе прошлого опыта формования. Вместо этого они должны быть установлены на основе проведенных экспериментов и полученных на их основе результатов. Понимание чувствительности качества детали к этим факторам дает представление об установке допусков параметров процесса во время формования. Благодаря множеству размеров и множеству полостей окна становятся все меньше и меньше. ![]() (из статьи Сухаса Кулкарни, PlasticsToday) |
КАК СОЗДАЮТСЯ СОВРЕМЕННЫЕ ОКНА ИЗ ПВХ — ИСТОРИЯ И ТЕХНОЛОГИЯ
В наши дни все мы привыкли иметь окна из ПВХ в своих домах и думаем о них как о неотъемлемой части любого домашнего дизайна, а не как о техническом достижении.Несколько десятилетий назад было довольно сложно представить, что полимер винилхлорида так быстро изменит нашу жизнь и обеспечит новый уровень комфорта. Давайте взглянем на недавнюю историю окон UPVC , чтобы увидеть, как этот красивый и удобный продукт стал доступным для домовладельцев.
Первое открытие ПВХ
Не так давно мы привыкли к традиционным окнам с деревянными каркасами и с ними довольно удобно.Но человечество всегда стремилось найти лучшие материалы, которые сделают нашу жизнь проще и предложат такие преимущества, которые не могут предложить натуральные продукты.
ПВХ был одним из материалов, открытие которого стало случайным, и ему пришлось пройти долгий и трудный путь, прежде чем он смог получить широкое распространение в промышленном производстве.
Первое случайное открытие ПВХ датируется 19 -м гг., 1838 и 1872 гг. — эксперименты французских и немецких ученых привели к открытию газообразного винилхлорида, что сопровождалось появлением ПВХ в твердом белом состоянии. .На тот момент никому не удавалось довести этот материал до коммерческого уровня по той причине, что с ним было очень сложно работать.
В начале -х годов века полимеризация винилхлорида под действием солнечного света была запатентована немецким изобретателем.
По-настоящему успешные эксперименты с ПВХ прошли в США вскоре после того, как американский инженер-химик Уолдо Семон сумел синтезировать полимер с целью заменить натуральный каучук. Его метод пластификации ПВХ путем смешивания его с различными добавками был запатентован и позволил нам получить гибкий материал, который легко обрабатывать и использовать в коммерческих целях.
Применение ПВХ
Первое коммерческое применение ПВХ после его изобретения Уолдо Семоном началось с его использования в качестве водостойкого покрытия ткани.
Пять компаний начали массовое производство ПВХ к середине -го века, а в последующие десятилетия нашли еще более инновационное применение в различных отраслях промышленности.
Прочность ПВХ также увеличилась, что привело к его применению в строительной отрасли.
ПВХ становился незаменимым и неотъемлемым продуктом строительства со всеми его полезными свойствами, такими как устойчивость к свету, коррозии, химическим веществам и даже экстремальным температурам.
В настоящее время ПВХ занимает третье место по объему производства среди других видов пластика в мире. Многие отрасли промышленности, включая здравоохранение, транспорт, текстильную и швейную, строительную и т. Д., Полагаются на этот выдающийся полимер, который, помимо превосходной прочности, также имеет низкую стоимость.
ПВХ в оконном производстве
Одним из самых популярных видов применения ПВХ в строительстве являются пластиковые окна или окна из ПВХ. «U» означает, что он не пластифицирован, т.е. не размягчается химическими пластификаторами.
Являясь смесью хлора, углерода и водорода, НПВХ в чистом виде не очень подходит для оконных профилей, поэтому в него добавляют некоторые стабилизаторы, и тогда ПВХ становится идеальным для оконного применения.
Если вы установили окна из ПВХ, вам не нужно беспокоиться о погодных условиях, гниении, вздутии или выцветании на них.
Срок службы окон из ПВХ считается около 25 лет, после чего материал может быть переработан при высоких температурах.
Как производятся окна из ПВХ
Современные окна из ПВХ от Northview Windows & Doors изготавливаются с использованием новейших технологий. инновационная технология URBAN machinery — одно из лучших в мире оборудования для производства виниловых окон.
Производство окна из ПВХ начинается с помещения расплавленного ПВХ в прецизионную матрицу для формирования профиля.Каждый профиль имеет свои конструктивные особенности.
Профили из ПВХ затем разрезаются на секции определенного размера, которые соединяются друг с другом посредством сварки плавлением, образуя форму окна. Каждый профиль снабжен металлическими вставками для дополнительной прочности и устойчивости. Затем сварные углы профилей из ПВХ очищаются машинами для очистки углов, и профили собираются в окна.
Именно так на оконных фабриках производятся красивые пластиковые окна нестандартной формы .Каждое окно из ПВХ изготавливается в соответствии с размерами, определенными установщиком, что гарантирует идеальную подгонку для любой установки. Для вашего удобства окна из ПВХ изготавливаются в широком диапазоне стилей, таких как оконные створки , одинарные или двойные окна, навесные окна и т. Д. Кроме того, оконные профили из ПВХ бывают разных цветов, чтобы вы могли создать еще более привлекательный и индивидуальный облик вашего дома.
Если у Вас возникли вопросы о том, как изготавливаются окна из ПВХ и как они работают, обращайтесь к нашим специалистам.
Наши возможности для оконных и дверных компонентов
Rodon использует инновационные процессы автоматизации, чтобы предлагать превосходные решения для окон и дверей. С 2010 года наши техники используют 3D-дизайн, изготовление инструментов, литье пластмасс под давлением и робототехнику для создания наиболее экономичных компонентов на рынке. Помимо индивидуальных решений, компания Rodon также предлагает высококачественные стандартные оконные детали. Изготовление изделий из нейлона, полипропилена, целкона, винила и подобных материалов обеспечивает высокую устойчивость к погодным условиям и термостойкость.
Пластиковые детали для окон и дверей, отлитые под давлением
Использование пластиковых деталей, изготовленных методом литья под давлением, в окнах и дверях дает несколько уникальных преимуществ:
- Изменение конструкции существующих деталей в соответствии с текущими спецификациями сводит к минимуму вложения и упрощает сборку.
- Заменители смолы для металлических компонентов обеспечивают высокий уровень надежности при меньших затратах.
- Компоненты на основе пластика и смол уменьшают коррозию и ржавчину в сложных условиях.
Литье пластмасс под давлением позволяет производить детали большего объема по более низкой цене. Это также снижает расходы на техническое обслуживание и ремонт при определенных операциях.
Универсальные пластиковые компоненты могут заменять различные части дверей и окон, например:
- Заглушки отверстий
- Крышки плачут
- Вентиляционные ограничители
- Стандартные и нестандартные зажимы и соединители для брусьев muntin
- створчатые ручки
- Накладки на экран
- Фиксатор наклона
- Оконные ролики в сборе
Производители, сборщики и установщики окон и дверей могут улучшить свою продукцию с помощью пластиковых деталей, отлитых под давлением, при одновременном снижении своих общих затрат.
Пример использования Rodon
Rodon имеет почти десятилетний документально подтвержденный успех в настройке деталей для оконной и дверной промышленности.
Редизайн оснастки для крупного производителя
Крупный производитель обратился к Родону за помощью в замене части собственного производственного процесса. Инструменты, которые использовались для производства деталей для окон жилых домов, больше не позволяли производить высококачественные компоненты. Из-за возраста и состояния ремонт или замена оборудования не представлялись возможным решением.Производитель обратился к нам, чтобы помочь найти экономичную альтернативу.
Инженеры Rodon разработали индивидуальный редизайн, который обеспечивает высокое соответствие при меньших затратах. Благодаря использованию многогнездных пресс-форм модернизированный инструмент обрабатывает дроби размером от 0,03 до 20 граммов. Энергоэффективные прессы от 46 до 233 тонн снижают затраты на производство пластмассовых деталей, изготовленных литьем под давлением. С помощью нового инструмента производитель может производить компоненты диаметром от 0,375 до 4 дюймов.Они также могут выбирать между текстурированной и глянцевой отделкой, чтобы соответствовать их предпочтительной эстетике.
Решения для литья пластмасс под давлением от Rodon
Пластиковые смолы — это надежный, экономичный и устойчивый к коррозии вариант оконных и дверных компонентов, традиционно изготавливаемых из металла. Используя пластмассовые детали, отлитые под давлением, производители могут создавать детали по индивидуальному заказу с меньшими общими затратами. Эти детали также поддерживают эффективный процесс сборки, что положительно влияет на прибыль и сроки поставки.
Rodon производит стандартные и индивидуальные детали для окон и дверей. Наш собственный процесс изготовления пресс-форм поддерживает крупносерийное производство, долгосрочное использование и превосходную технологичность. В настоящее время пластиковые детали, изготовленные методом литья под давлением, получают 99,8% одобрения клиентов.
Сотрудничайте с Rodon для повышения эффективности производства окон и дверей. Посмотрите наш каталог компонентов, чтобы узнать больше об окнах и дверях
Ценный ПВХ из пластиковых окон
Оконный профиль со вставленными резиновыми уплотнениями и коэкструдированными уплотнительными кромками из пластифицированного ПВХ.Срок службы достигает не менее 40 лет, что означает меньшее использование ресурсов и меньшую нагрузку на выбросы CO2. Теоретически цикл использования окон и восстановления может быть повторен семь раз без отрицательного воздействия на сырье или качество обработки.
Здесь перерабатываются не только излишки производственного материала и обрезки профилей, образующиеся при производстве окон, но и старые окна, изношенные двери, ламели для рольставен и т. Д.
По данным Rewindo.de Association, совместно созданная производителями окон из ПВХ с целью поощрения переработки окон из ПВХ, уровень вторичной переработки старых окон составляет 89 процентов, что соответствует 101 000 тонн рекуперированного гранулята из ПВХ. Из них 73 645 тонн приходится на отходы производства и 27 328 тонн на переработку старых окон.
Конструкция окон ПВХ
Оконные профили ПВХ производятся из особо качественного ПВХ. Долговечный высококачественный пластик с оптимальными эксплуатационными характеристиками получается благодаря использованию таких добавок, как УФ-стабилизаторы, пигменты, наполнители и т. Д.Преимущество таких ПВХ-компаундов — их универсальная возможность вторичной переработки. Это означает, что обрезки профиля и, конечно же, старые окна можно перерабатывать любое количество раз и, в идеале, снова найти применение в новых окнах.
Стальные профили, встроенные в профили из ПВХ, стабилизируют целые окна. Эта «механическая» система действует как решение, позволяющее надежно открывать, закрывать, наклонять и поворачивать окна. Уплотнительные кромки, уложенные в профиль или совместно выдавленные на профиль, служат для уплотнения крыльев и рам, а также стекол (Фото 1).
Помимо резины и пластифицированного ПВХ, для уплотнения современных окон используются и другие пластмассы. Особенно в случае раздвижных окон в полипропилене используются так называемые уплотнительные щетки. Также все чаще встречаются маленькие колеса и детали из нейлона. Силиконовые герметики для герметизации швов также можно найти в старых окнах, а также в различных других пластмассах, которые используются для сборки и регулировки окон при их установке в зданиях.
Оконные профили с сердцевиной из вторсырья
Новые высокотехнологичные профили возникают из переработанных пластиковых окон, поскольку чистый вторичный ПВХ также используется для сердцевины профилей, а внешний покровный слой состоит из первичного ПВХ.Это экономит ресурсы и сохраняет окружающую среду.
Оконные профили с сердцевиной из вторичного сырья являются практическим доказательством использования экономики замкнутого цикла. Они лишь частично отличаются от профилей из первичного материала по цвету, но на 100% имеют одинаковое качество, то есть такие ПВХ-профили легко соответствуют высоким стандартам качества, предъявляемым к пластиковым окнам, в том числе по тепло- и звукоизоляции.
Влияние посторонних материалов
Чтобы иметь возможность повторно обрабатывать ПВХ из оконных профилей, обрезков профилей или старых окон, необходимо полностью удалить все материалы, не состоящие из ПВХ, перед обработкой.
Влияние посторонних материалов, таких как дерево, металл, стекло и т. Д., На гранулят ПВХ очевидно. Это приводит к повреждению экструдеров, инструментов и конечного продукта. Хотя эти материалы в большинстве случаев можно легко отделить с помощью установленных технологий разделения (магнитная сепарация, сепарация на вибростоле и т. Д.), Разделение уплотнений из пластифицированного ПВХ и особенно резиновых уплотнений не так просто.
Пластифицированный ПВХ легко смешивается с жестким ПВХ.Однако тогда возникает проблема, заключающаяся в том, что цвет гранулята значительно изменяется после экструзии. Конечный продукт становится все более серым и, следовательно, более непривлекательным, особенно при использовании удерживающих лент для остекления, т. е. с большой долей цветных (черных) профилей.
Еще более проблематично, если резиновые уплотнительные материалы присутствуют в переточке. Материал резинового уплотнения не плавится в экструдерах и не сцепляется с ПВХ. Когда профиль экструдируется из такого гранулята, который содержит загрязнения резиной, на поверхности появляются «пупырышки», а каналы профиля закрываются в экструзионном инструменте и т. Д.
В частности, в новых конструкциях окон, в которых для повышения устойчивости используются многокамерные профили, и особенно из-за более высокой теплоизоляции, используемые здесь перемычки камер имеют толщину всего несколько десятых миллиметра, так что уже один небольшой кусок резины который «застревает» в инструменте для такого профиля, может привести к образованию нескольких метров профиля отходов, прежде чем такое повреждение будет обнаружено.
Каучук можно до некоторой степени отделить фильтрацией расплава в экструдере, но только если уровень каучука не слишком высок. Это также относится, конечно, к другим загрязнителям, таким как дерево и металл, или другим пластмассам с более высокими температурами плавления, чем у ПВХ.
Решения для отделения посторонних материалов
Сортировка вручную
Сортировка вручную востребована, в частности, для «вытягивания» резиновых уплотнений из профилей и обрезков профилей. Это очень трудоемкое мероприятие, прежде всего потому, что резиновые уплотнители в современных оконных профилях плотно вставляются в выемки профиля, практически без люфта.Несмотря на использование плоскогубцев или других инструментов, один сортировщик не может отсортировать более 60-100 кг пломб в час из таких профилей.
Коэкструдированные уплотнения — это уплотнения, которые невозможно отделить чисто механическими средствами. Очевидно, что есть компании, которые просто отпиливают эти пластифицированные уплотнительные кромки из ПВХ и получают жесткий ПВХ без загрязнения пластифицированным ПВХ, но затраты на это не оправданы при выплате ставок заработной платы в «Центральной Европе».
Затраты на сортировку, возникающие только для отделения резины при таком способе переработки окон, составляют до 200.00 евро за тонну — особенно высокий фактор затрат при переработке. По этой причине стремятся достичь экономии за счет полностью автоматизированных рабочих процессов отделения посторонних материалов.
Процессы автоматической сортировки
Отделение металлов
Черные металлы можно легко отделить с помощью магнитов на ленточных конвейерах или магнитных верхних роликах. Даже самая мелкая железная пыль размером до 25 мкм не проблема для магнитов с высокими характеристиками.
Конечно цветные металлы в виде алюминиевых деталей и оконной фурнитуры и др.могут быть эффективно отделены с помощью вихретоковых сепараторов. Однако отделение мелких частиц алюминия или нержавеющей стали от измельченного материала проблематично. Электростатические сепараторы коронного разряда KWS от Hamos GmbH предлагают здесь решение. На этом оборудовании практически вся металлическая фракция отделяется сухим способом. Легко отделяются даже металлические частицы размером <500 мкм. Здесь работает высокопроизводительное оборудование с несколькими ступенями, с производительностью от 500 до 2500 кг / ч, низким энергопотреблением и практически полностью автоматически без участия обслуживающего персонала (Фото 2).
Кроме того, другие токопроводящие загрязнения, например, древесина при обработке старых окон одинаково хорошо отделяется от потока ПВХ с помощью коронного сепаратора Hamos KWS.
Решения для отделения нашей резины
При отделении резины от жесткого ПВХ задача состоит в том, чтобы отделить нежелательный посторонний материал (резину) от хорошего материала. При этом необходимо учитывать, что оба материала должны иметь одинаковый удельный вес, а в некоторых случаях даже один и тот же цвет, учитывая, что белые резиновые прокладки или цветные прокладки в настоящее время все чаще используются в цветных профилях. Процессы механического разделения здесь в значительной степени не учитываются, поскольку они не могут гарантировать требуемую чистоту и необходимую производительность, даже когда оборудование работает с высокой производительностью.
Решением является разделение оборудования Hamos EKS с помощью электростатической технологии. Для отделения «резины» и «пластифицированного ПВХ» от жесткого ПВХ используется различное поведение электростатического заряда двух непроводящих материалов. Эти два непроводящих материала — резина и ПВХ — интенсивно контактируют друг с другом в специальном зарядном оборудовании.Путем передачи заряда между материалами ПВХ приобретает отрицательный заряд, а резина — положительный. Два типа материалов в этой заряженной смеси продуктов затем могут быть отделены друг от друга с помощью блока разделения, интегрированного в оборудование EKS. Для этого на электродную систему подается высокое напряжение.
Специальное расположение электродов гарантирует, что другие пластмассы, дерево и другие загрязнения будут отделены вместе с резиной и пластифицированным ПВХ.
На практике возможно, например, полностью отделить загрязнение из смеси, состоящей из 90% жесткого ПВХ и 10% резины / пластифицированного ПВХ. Таким образом, всего за один проход достигается чистота ПВХ более 99,5%. Пропускная способность мин. При использовании стандартного оборудования Hamos EKS возможна 1000 кг / ч. Два или более оборудования устанавливаются параллельно для более высокой производительности.
Оптическая сортировка
Качество вторичного сырья можно еще больше повысить с помощью оборудования для оптической сортировки Hamos SEA.Затем программируется оптоэлектронное оборудование для сортировки по цвету таким образом, чтобы «белый» измельченный материал выпадал из конвейера, а «цветные» материалы (к которым также относятся частицы резины) выдуваются коротким импульсным потоком воздуха. Помимо цветного резинового уплотнителя, также отделяется цветной жесткий ПВХ. Благодаря тому, что материалы одновременно контролируются оптически с двух сторон, детали из ПВХ, которые с одной стороны украшены декоративной пленкой, также могут быть легко отделены.
После оптической сортировки, с одной стороны, потоки высококонцентрированных отходов приводят к максимальному выходу ПВХ, так как потери ПВХ минимальны.
Чистота белого материала почти соответствует чистоте первичного материала, поэтому этот продукт можно легко использовать при производстве новых окон.
Эффективность
Жесткий ПВХ является ценным сырьем из-за высокого содержания в нем добавок и пигментов. По этой причине, а также, естественно, из-за отличной способности к повторному использованию, измельчение окон из ПВХ очень востребовано как вторичный материал.
Если эта переточка из ПВХ будет снова использована в производстве оконных профилей, она не должна содержать резины и других загрязнений, поскольку в противном случае повторное использование просто невозможно.
Благодаря высокой производительности электростатического и оптоэлектронного сортировочного оборудования, получается почти 100% чистый измельченный ПВХ с минимальными затратами на разделение. Процессы разделения требуют мало энергии, работают практически полностью автоматически и поэтому особенно эффективны.
Пример клиента
Чтобы еще больше расширить свою деятельность по переработке и внести важный вклад в охрану окружающей среды, компания REHAU, специализирующаяся на полимерах, расширила свой польский завод в Среме, установив современную линию переработки с производительностью около 10 000 тонн в год. . Основной особенностью является сортировочная линия Hamos, которая разделяет сырье на отдельные фракции и обеспечивает высочайшее качество для дальнейшей обработки.
«Мы очень довольны стандартом, достигнутым компанией Hamos GmbH».
Йорг Ипфлинг, руководитель проекта «Оконные решения по переработке отходов» в Rehau, говорит: «Мы очень довольны стандартом, достигнутым компанией hamos GmbH.Ранее было невозможно полностью автоматически отсортировать ПВХ из обрезков профилей и излишков производственного материала в соответствии с этим высоким стандартом качества и чистоты. Эта разработка помогла нам полностью замкнуть материальный цикл. Так родился новый стандарт мирового уровня ».
Г-н Бодо Штройбель, директор завода Dekura Bad Schmiedeberg, говорит: «После 17 лет работы наш опыт работы с предприятием по переработке окон Hamos WRS очень положительный. Завод помог нам достичь наших целей, гарантируя высочайшее качество, требуемое для ПВХ, и тем самым увеличивая общую производительность нашего процесса.
Введение системы Hamos стало незаменимым и «замыкает наш цикл переработки».
Надежная обработка, часть 1: эстетика, размеры и контроль pro
Надежный процесс — это Святой Грааль литья под давлением — он позволяет снова и снова создавать хорошие детали. Достижение этого — тоже процесс. Эта статья, состоящая из двух частей, описывает процесс от начала до конца. —Сухас Кулкарни
Квалификация пресс-формы и детали включает шесть этапов: исследование вязкости, испытание на падение давления, определение баланса полости, исследование окна процесса, исследование уплотнения затвора и исследование времени охлаждения. Четвертый пункт, исследование окна процесса, предоставляет информацию о пределах выбранных параметров процесса, между которыми могут быть отлиты приемлемые детали. Как правило, окно должно быть разработано с учетом зависимости давления выдержки от температуры расплава для аморфных материалов и зависимости давления выдержки от температуры формы для кристаллических материалов (рисунок 1).
Рис. 1. Разработка технологического окна для аморфных и кристаллических материалов. Рисунок 2.График размерного контура наложен на окно процесса и окно процесса измерения. Рисунок 3. Окно размерного процесса и окно процесса управления. Рисунок 4. Окно процесса управления и окно составного процесса. Рисунок 7.Установка окон допусков процесса с помощью программного обеспечения Nautilus для DOE. |
В этих пределах (или внутри этого четырехугольника) литые детали не имеют косметических дефектов. Например, удерживание давления над верхней линией может привести к вспышке, а под нижней линией — к проседанию или короткому замыканию. Всегда желательно большое технологическое окно, чтобы уменьшить вероятность дефектов. Литая деталь с короткими замыканиями и засветкой является примером «окна без технологического процесса».«Надежный процесс — это процесс, который задается в центре этого окна, что гарантирует, что естественное изменение процесса по-прежнему будет давать приемлемые детали.
Описанная выше техника обеспечивает эстетическое восприятие детали. Центр окна был бы идеальным процессом, если бы детали, отформованные в этих условиях, имели номинальные размеры и если бы верхний предел спецификации (USL) и нижний предел спецификации (LSL) содержались внутри этого окна. Следовательно, мы должны изучить влияние обоих параметров обработки на размеры детали.Для проведения такого исследования может быть использована методика планирования экспериментов (DOE). Выходные данные DOE включают в себя контурные графики размеров, линии, которые описывают условия процесса для достижения определенного размера. На рис. 2 показан контурный график. Исследования DOE должны проводиться в четырех углах технологического окна, где детали эстетически приемлемы. (Более подробную информацию о DOE можно найти в Части 2 этой статьи.)
Из графика очевидно, что части с приемлемыми размерами теперь находятся в пределах окна, которое меньше, чем ранее разработанное окно, и является его подмножеством.Предыдущее окно называется окном эстетического процесса (APW), а окно подмножества выше называется окном размерного процесса (DPW). Рисунок 2 включает верхний и нижний пределы спецификации и показывает DPW, сгенерированный из этих пределов.
Теперь мы можем пойти дальше этой концепции и включить в DPW возможности обработки. Пределы контроля могут быть установлены в зависимости от процесса и размеров. Это называется окном процесса управления (CPW), которое учитывает все естественные отклонения и предоставляет рабочие окна.Рисунок 3 включает верхний и нижний контрольные пределы и показывает CPW, полученный из этих пределов.
Наложение нескольких измерений на это окно делает фактическое рабочее окно еще меньше, и в результате получается окно составного процесса (CoPW), показанное на рисунке 4.
Все эти концепции, определенные в поле внизу этой страницы, были применяется к детали, которая была проверена на длину и диаметр. Результаты показаны на рисунках 5 и 6.
Установка пределов и допусков сигналов тревоги
Пределы и допуски сигналов тревоги часто путают друг с другом.Пределы сигналов тревоги — это границы, которые устанавливаются на выходе процесса формования, тогда как допуски — это те, которые устанавливаются в настройках процесса. Например, на рис. 7 при времени охлаждения 13 секунд (и допуске 0,5 секунды) приемлемые детали могут быть отформованы под давлением от 915 до 1200 фунтов на квадратный дюйм. Это должны быть рабочие допуски производственного персонала. Предположим, что величина амортизации при 915 фунтах на квадратный дюйм составляет 0,23 дюйма, а при 1200 фунтах на квадратный дюйм — 0,18 дюйма. Затем должны быть установлены пределы срабатывания сигнализации для значений амортизации с минимальным значением 0.18 и высотой 0,23 дюйма. Эту концепцию можно применить и к другим выходным данным, таким как давление в полости, что является окончательным и наиболее эффективным способом измерения качества детали.
Наложение различных окон, созданных в процессе квалификации пресс-формы, отображает рабочие области процесса литья. Хотя аттестация пресс-форм с использованием технологических исследований и DOE является обычным делом, метод корреляции данных, полученных с помощью этих двух методов, отсутствует. Каждый из этих двух методов обеспечивает важные данные, но их сочетание дает очень четкое понимание возможностей пресс-формы и процесса формования.
Широкие технологические окна дают возможность успешно выполнять операции формования. Некоторые утверждают, что окно становится все меньше и меньше по мере увеличения количества размеров и полостей. К сожалению, это реальность, хотя это была скрытая правда. Это основная причина, по которой у большинства компаний есть только один утвержденный технологический лист. Пределы сигналов тревоги и допуски обычно устанавливаются на основе прошлого опыта формования. Вместо этого они должны быть установлены на основе проведенных экспериментов и полученных на их основе результатов.Понимание чувствительности качества детали к этим факторам дает представление об установке допусков параметров процесса во время формования.
Наличие нескольких размеров и множественных полостей делает окна все меньше и меньше. Это также является аргументом в пользу хорошей формы и деталей с практически определенными допусками. Важное значение приобретают принципы и практики параллельной разработки. Надежный процесс требует меньшего вмешательства человека. Частота проверки может быть уменьшена.Таким образом, заблаговременное планирование и дисциплинированный подход к разработке процессов необходимы для обеспечения эффективности производственного цикла и прибыльности производства.
Сухас Кулкарни ([email protected]) — президент Fimmtech, консалтинговой фирмы, специализирующейся на услугах, связанных с литьем под давлением. Он разработал специальное программное обеспечение под названием Nautilus, которое помогает выполнять полный цикл разработки процессов, основанный на принципах научного литья и дизайна экспериментов. Посетите Сухаса в NPE на стенде S9024.
Прочтите Часть 2, «Научное моделирование и планирование экспериментов: что первично».
Определения Окно эстетического процесса (APW): Границы, в пределах которых может быть отформована эстетически или косметически приемлемая деталь. Размеры не имеют значения. |