Как делают цемент: технология производства цемента
Любое строительство или ремонтные работы невозможны без использования универсального строительного материала – цемента разных видов и марок. Мы настолько привыкли к этому продукту, что даже не задумываемся над проблемой, а как делают цемент. Можно ли его можно изготовить в домашних условиях и не переплачивать?
СодержаниеСвернуть
Сразу ответим на вопрос – можно ли сделать цемент своими руками? Имея необходимое оборудование и исходные материалы – получить цемент в домашних условиях можно. На данный момент времени в Российской Федерации большим спросом пользуются мини-заводы по производству цемента, мощностью порядка 120 000 тонн цемента в год. Производить же цемент для единичной стройки экономически невыгодно. Проще и дешевле купить этот необходимый строительный материал на заводе или в магазине.
Состав цемента
Цемент получается при длительном дроблении клинкера и гипса. Клинкер — продукт равномерного обжига до спекания однородной сырьевой смеси, состоящей из известняка и глины определённого состава, обеспечивающего преобладание силикатов кальция.
При измельчении клинкера вводят добавки: гипс СaSO4·2H2O для регулирования сроков схватывания, до 15 % активных минеральных добавок (пиритные огарки, колошниковую пыль, бокситы, пески) для улучшения некоторых свойств и снижения стоимости цемента.
Производство цемента на заводах
На данный момент времени производителями цемента используются три технологии производства связующего:
- Мокрый способ.
- Сухой способ.
- Комбинированный метод.
Стоит заметить что «сухую» технологию используют зарубежные производители цемента: Египет, Турция и Китай. «Мокрая» же технология традиционно используется отечественными цементными заводами.
циклы производства цементаСухой способ
Здесь нет необходимости использовать воду. Исходный материал (глину и известняк) дробят на специальном оборудовании. Сушат и перемалывают в мелкодисперсную муку, смешивают пневматическим способом и подают на обжиг.
Образовавшийся в результате обжига цементный клинкер измельчается до соответствующей степени фракции, фасуется в упаковку и отправляется на склад готовой продукции. Данный способ позволяет снизить затраты на производство, однако отличается «капризностью» к однородности исходных материалов и является экологически опасным вариантом.
Мокрый способ
Неоспоримые достоинства данного метода заключается в возможности точного подбора состава исходного сырья при высокой неоднородности исходных компонентов: порода, вид породы и пр. Исходный материал (шлам) представляет собой жидкую субстанцию, содержащую до сорока процентов влаги.
Перед тем как сделать цемент, состав шлама корректируется в специальных технологических бассейнах. После выдержки сырья в бассейне, производится отжиг в специальных вращающихся печах и последующее измельчение.
Мокрый способ требует большего расхода тепловой энергии расходуемой на высушивание исходного сырья. Это существенно увеличивает себестоимость производства цемента, однако качество конечной продукции не страдает от возможной неоднородности клинкера, как при мокром варианте.
Комбинированные способы
Данная технология опирается на мокрый вид получения связующего. Промежуточную субстанцию обезвоживают по специальной технологии. Клинкер гранулируют с добавлением воды, после чего производят отжиг и последующее измельчение до той или иной марки цемента.
В числе достоинств комбинированного способа производства цемента: высокий выход «годного», возможность использования отходов металлургической промышленности.
Как делают белый цемент
Технология производства белого цемента незначительно отличается от технологии производства обычного «серого» материала. Как и обычный «серый» материал, белый цемент выпускают сухим и мокрым способом. Основное отличие технологии – обжиг исходного сырья при высокой температуре и резкое охлаждение в воде.
Клинкер белого цемента характеризуется как «маложелезистый» и содержит в своем составе: минеральные добавки, известняк, гипс, соли и другие компоненты. В качестве исходного сырья для клинкера используются карбонатная и глинистая порода (известняк, каолиновая глина, отходы обогащения, кварцевый песок).
В Российской Федерации белый цемент производится только на одном предприятии – ООО «Холсим (Рус) СМ» (до 2012 года ОАО «Щуровский цемент»). Большинство белого цемента поставляется на рынок России из-за рубежа следующими компаниями: «Холсим» (Словакия), «Cimsa иAdana» (Турция), «AalborgWhite»(Дания) и «AalborgWhite» (Египет).
Основное достоинство белого цемента его уникальная характеристика – белоснежность, а основной недостаток в разы большая стоимость по сравнению с обычным «серым» материалом.
Заключение
Теперь вы знаете, как делают цемент на заводе в общем случае. Информацию как правильно делать цемент во всех подробностях, цифрах, схемах, таблицах и других тонкостях смотрите в специальной литературе.
Производство цемента в России
Высокие темпы роста строительства в России всё больше подчёркивают важность и необходимость развития такой отрасли промышленности, как промышленность строительных материалов.
Среди различных строительных материалов цемент занимает главенствующие позиции как наиболее распространённый вяжущий материал для изготовления изделий и конструкций высочайшей прочности (бетон, железобетон, асбестоцементные изделия). Основные потребители – строительные компании, которые создают спрос на цементном рынке и являются движущей силой в производстве и создании новых видов цемента.
На сегодняшний день выпускают портландцемент, шлакопортландцемент и глиноземистый цемент, которые отличаются составом и специальными добавками.
Основу цемента составляют следующие сырьевые материалы: известняк, глина, мергель (разновидность камня), мел, гипс, а также вода, которые в процессе производства при дроблении и смешивании образуют сырьевую смесь.
Различают два способа приготовления такой смеси – сухой и мокрый.
Сухой способ является наиболее экономным, поэтому активно применяется во многих странах. Здесь не требуется вода. Вся сырьевая масса смешивается и обжигается в специальных клинкерных печах.
Мокрый способ не потерял свою актуальность, особенно на российских предприятиях. В производстве цементной смеси используется вода, которая на конечном этапе выпаривается в печи.
Российский рынок цемента представлен примерно 30 крупнейшими производителями, среди которых наиболее заметными являются холдинг «Евроцемент груп» и ОАО «Группа ЛСР», распространившие свою деятельность в разных регионах России. Не менее известными также являются следующие Российские цементные заводы: это ОАО «Искитимцемент», ОАО «Новотроицкий цементный завод», Сланцевский цементный завод «Цесла», холдинг «Сибирский цемент», Серебряковский цементный завод и другие предприятия, расположенные в основных потребительских и сырьевых районах страны.
Цементные заводы России — полный список производителей
История производства цемента в России начинается с заявки на патентование нового вяжущего вещества Егором Челиевым в 1825 году. Хотя, практические работы с применением цементных смесей велись в 1813 году при восстановлении Москвы на работах по укреплению берегов Москва-реки и строительстве Кремля. Но волею судеб автором портландцемента считается англичанин Дж. Аспдин (Joseph Aspdin), запатентовавший технологию в 1824 году. Начиная с 1836 года, Россия постоянно наращивала производство цемента, которое к 1913 году достигло 1,78 млн. тонн в год. Большинство предприятий располагалось на юге России, где месторождения известняка или мергеля выходят на поверхность (как говорят ученые — южнее границы последнего ледникового периода).
Виды продукции
Все виды продукции являются производными от портландцемента. Минеральные добавки и вид основного сырья придают цементу различные свойства.
- Белый цемент — основа для отделочных смесей, цветного цемента марки ЦЦ. Применяется для строительства архитектурных объектов без последующей отделки.
- Быстротвердеющий цемент — применяется в строительстве быстровозводимых и заливных строений.
- Водонепроницаемый безусадочный цемент — применяется в строительстве для формирования гидроизоляции и заделки швов гидросооружений.
- Гидрофобный цемент — присадки снижают водопоглощающие свойства, что увеличивает срок хранения.
- Глиноземистый цемент — добавки глинозема (аллюминат и бокситы) увеличивают скорость отверждения с выделением большого количества тепла. Актуально для зимнего строительства. При добавлении гипса получается расширяющийся цемент марки РЦ.
- Напрягающий цемент — применяется для изготовления железобетонных изделий.
- Пуццолановый цемент — добавление тонкоизмельчённого активного кремнезёма увеличивает время схватывания и понижает тепловыделение. Актуально при возведении объектов с большими сечениями и объемами.
- Сульфатостойкий цемент — характеризуется жесткими ограничениями по содержанию трёхкальциевого алюмината и трёхкальциевого силиката. Применяется при возведении сооружений циклически контактирующих с водой.
В отдельную группу выделяются шлаковые цементы, которые изготавливаются из отходов металлургического производства или золы от сжигания сланцев и бурого угля. Применяется в производстве шлакоблоков.
Технология производства
Принцип производства цемента не претерпел кардинальных изменений с момента его изобретения. Основные процессы:
- Добыча известняка или мергеля открытым способом.
- Измельчение.
- Приготовление смеси.
- Обжиг.
- Выдержка. Выдержка производится в течение 1…2-х недель для завершения химических процессов.
- Помол, упаковка в мешки или закладка в силосы для хранения.
Различают два способа — сухой и мокрый. При использовании мокрого способа перемешивание происходит с добавлением воды, которую затем выпаривают. К достоинствам этого способа можно отнести равномерность смеси по составу и размеру фракций. Недостаток — большой расход энергии на выпаривание воды перед обжигом (энергозатраты составляют 20…25% стоимости).
Производится в клинкерной (вращающейся) печи с факельной горелкой. Печи для мокрой смеси вдвое длиннее и больше по диаметру, чем печи для сухой смеси. Температурный режим: верхняя загрузочная зона — 70…200 °С, зона декарбонизации — 700…1100 °С, зона спекания 1300…1450 °С, зона охлаждения — 1300…900 °С, с переходом в холодильник для быстрого охлаждения гранул.
Сухой способ приготовления смеси получил развитие с появлением устройств экспресс-анализа состава смеси и технологий с автоматизацией процесса смешивания, что снизило энергетические затраты в 2…3 раза и увеличило съем продукции с одного квадратного метра производственной площади. На выходе получаются клинкерные гранулы.
Положение в отрасли
Пик развития производства цемента приходится на 1965…1972 годы. СССР занимал первое место в мире, производя 100…140 млн. тонн в год (мощности предприятий РСФСР — 89…95 млн. тонн). В 90-е годы было выведено из производства более половины предприятий общей мощностью 17.
Ведущие компании:
- Евроцемент Груп (13 крупнейших заводов по всей территории России).
- Холдинг Holcim Group.
- Группа компаний ЛСР.
- Консорциум United Cement Group.
- Холдинг Сибирский цемент.
- ХайдельбергЦемент Рус.
- Компания Lafarge.
Темпы ежегодного прироста за период 2009…2012 годы составлял 4,5 %, а в 2013 — 7,8% (объем 66,4 млн. тонн). В настоящее время 90% цемента производится по затратному «мокрому» способу.
Перспективы отрасли
В целом перспективы рынка цемента имеют основания для оптимизма. Потребность в цементе удовлетворяется промышленностью на 90%, а Правительство планирует строительство большого количества объектов (чемпионат мира по футболу, газопровод Южный поток, космодром Восточный, особый экономический статус Дальнего Востока и др.). Главным сдерживающим фактором развития отрасли является отставание в применении технологии сухого приготовления смеси.
Производство цемента в России в 2020 году снизится на 4%, а ожидалось вообще -10%
Таковы предварительные оценки объединения «Союз производителей цемента» (СОЮЗЦЕМЕНТ
Фото: www. rmr-servis.ru
«Реакция рынка строительных материалов на пандемию и ее долгосрочные последствия стали главным вызовом для цементной отрасли в 2020 году», — говорится в обзорно-аналитическом материале, опубликованном на сайте СОЮЗЦЕМЕНТА.
В нем приводятся ключевые цифры, характеризующие развитие ситуации в данном сегменте рынка в текущем году:
Фото: www.istservis.ru
• по итогам I квартала этого года рост потребления цемента вырос на 6,4% относительно I квартала 2019 года;
• в апреле этот показатель сократился на 17,9% относительно апреля 2019 года;
• по итогам II квартала потребление цемента показало снижение на 11,7% по отношению к прошлому году.
Как ранее информировал портал ЕРЗ.РФ, производство цемента, по данным Росстата, за десять месяцев этого года снизилось на 3,9% относительно аналогичного периода 2019 года.
Фото: www.twitter.com
Производство и потребление в России такого основного строительного материала, как им является цемент, значительно снизилось в этом году, признает исполнительный директор СОЮЗЦЕМЕНТА Дмитрий Сапронов (на фото).
Однако при этом он отмечает, что катастрофических последствий для отрасли удалось избежать благодаря мерам комплексной государственной поддержки экономики, запущенным по инициативе Президента России Владимира Путина.
Особенно эффективно в этом отношении проявила себя, по мнению Сапронова, госпрограмма льготной ипотеки для новостроек.
Фото: www.in-news.ru
«Программа льготных ипотечных кредитов по ставке 6,5% годовых на покупку жилья в новостройках, которая стартовала в апреле, позволила не только поддержать граждан, решивших улучшить свои жилищные условия, но также и строительный сектор, производство стройматериалов, логистические компании, а также рынок труда», — подчеркнул глава СОЮЗЦЕМЕНТА.
По его словам эта программа, оживив жилищное строительство за счет резко возросшего спроса, позволила сохранить загрузку мощностей, в результате чего производящие цемент предприятия продолжили отчисление налогов и иных выплат в бюджеты всех уровней.
Фото: www.yandex.ru
В итоге, несмотря на крайне негативные весенние прогнозы (тогда казалось вероятным падение объемов производства цемента по итогам 2020 года более чем на 10%), сегодня СОЮЗЦЕМЕНТ предварительно оценивает этот показатель лишь в минус 4%.
При этом в разной степени пострадали все федеральные округа страны — от -1% в Приволжском до -6% в Центральном и -8% в Южном, уточнил Сапронов.
Фото: www.prokcssmedia.blob.core.windows.net
Специалист также признал, что помимо негативных эффектов пандемии цементная подотрасль переживает непростой период уже в течение ряда лет. Так, с 2015-го по 2018 год потребление цемента снизилось более чем на четверть, и лишь в 2019 году был отмечен рост.
Текущий год стал очередным тяжелым испытанием для данного сегмента стройиндустрии: в целом по стране задействована лишь половина существующих производственных мощностей, сетует глава СОЮЗЦЕМЕНТА.
Фото: www.publishernews.ru
Другие публикации по теме:
Бетон и цемент — в минусе, техника — в плюсе
Стройиндустрия-2020: кирпича, песка и лифтов стало больше
Марат Хуснуллин: В случае необоснованного завышения цен на стройматериалы необходимо обращаться в ФАС
Эксперты ВШЭ: Отрасль ждет череда банкротств, сокращение численности занятых и портфеля заказов, снижение производительности труда и продаж, рост цен на стройматериалы
Владимир Путин: Поручаю проработать вопрос о преференциях стройке от государства как одной из отраслей, наиболее пострадавших от коронавируса
Технологии производство цемента — сухой и мокрый способы
Цемент пользуется огромной популярностью в строительстве. Его применяют как самостоятельно, так в качестве компонента многих строительных составов (к примеру, в производстве железобетона и бетона). Изготовление цемента – дорогостоящий и энергоемкий процесс. Заводы размещают в непосредственной близости к месту добычи сырья, из которого в дальнейшем будет создаваться продукт.
Производство цемента включат 2 этапа:
- получение клинкера,
- измельчение клинкера и введение добавок.
На получение клинкера приходится приблизительно 70% себестоимости стройматериала.
Начинается все с добычи сырьевых материалов. Как правило, добыча известняка осуществляется путем сноса части горы, после которого открывается слой желто-зеленого известняка. Глубина залегания известнякового слоя – приблизительно 10 м, толщина – в среднем 0,7 м. После того, как сырье доставлено на завод, производится обжиг в специальной печи при температуре +1450°С, в результате которого получают клинкер.
На второй стадии производства цемента осуществляют дробление клинкера, гипсового камня, сушка добавок. Затем производится помол клинкера вместе с добавками и гипсом. Гипс добавляют в размере 5% от общей массы, добавки вводят в зависимости от типа смеси.
Однако, учитывая тот факт, что технические и физические характеристики сырьевого материала могут отличаться, для каждого типы сырья предусмотрен свой способ подготовки.
Способы производства цемента:
- мокрый,
- сухой,
- комбинированный.
Изготовление цемента мокрым способом
Мокрый способ предусматривает изготовление цемента с применением карбонатного компонента (мела) и силикатного компонента (глины). Также используются железосодержащие добавки (пиритные огарки, конверторный шлам и пр.). Влажность мела не должна быть более 29%, а влажность глины – не выше 20%. Называется этот способ производства цемента тому, потому что измельчение сырья осуществляется в воде, на выходе образуется шихта в виде суспензии на водной основе. Влажность шихты – 30-50%. Далее производится обжиг шлама в печи, в результате которого выделяется углекислота. Образовавшиеся шарики-клинкеры перемалывают в тонкий порошок под названием цемент.
Производство цемента сухим способом
Данный способ по праву считается наиболее экономически выгодным. Особенность его в том, что на всех стадиях используются материалы только в сухом состоянии. Выбор схемы производства цемента определяется химическими и физическими характеристиками сырья. Наиболее востребованным признано изготовление материалов во вращающихся печах, в котором используются глина и известняк.
После того, как глина и известняк прошли измельчение в дробилке, их сушат до требуемого состояния (влажность — не более 1%). Просушка и измельчение производиться в сепараторной машине, после чего смесь отправляется в циклонные теплообменники, где находится не боле 30 секунд. Далее идет стадия, на которой производиться обжиг сырья с дальнейшим перемещением в холодильник. Затем клинкер направляется на склад, где происходит его перемалывание и фасовка. Подготовка гипса и добавок, а также хранение и транспортировка цемента идентичны тем, которые производятся при мокром способе.
Комбинированный вариант производства цемента
Шлам получают «мокрым» способом, после чего смесь обезвоживается в специальных фильтрах до того момента, пока уровень влажности не достигнет 16-18%. Далее сырье отправляют на обжиг. Второй вариант комбинированного способа производства цемента предусматривает сухое изготовление сырьевой массы, в которую затем вводят 10-14% воды и гранулируют. Размер гранул не должен превышать 15 мм. Далее производится обжиг.
Для каждого способа производства используют свое оборудование и определенную последовательность операций.
Современные производства ориентируют деятельность на получение материала сухим методом. Его по праву считают будущим цементной промышленности.
Обзор цементной промышленности — FIRA.RU
Цементная промышленность является одной из старейших в России, первый завод по производству портландцемента был построен еще в 1839 году. В настоящее время цемент и изготовляемые из него бетон и железобетон являются основными строительными материалами, которые используются в самых разнообразных областях строительства. При этом цемент остается относительно простым, универсальным и дешевым материалом, для изготовления которого требуются довольно доступное сырье — известняк, мергель, глины, мел, гипс, а также вода.
В настоящее время существуют следующие основные способы производства цемента: мокрый, сухой, комбинированный, а также их вариации. Преимуществом сухого метода производства по сравнению с мокрым является более высокий съем клинкера с 1 кв. метра печного агрегата, а также более низкий расход топлива. Так, производство портландцементного клинкера сухим способом требует в два раза меньше расхода топлива, чем мокрым. Глобальными тенденциями в производственном процессе цементных заводов являются отказ от мокрого способа производства и постепенный переход на сухой.
Основными факторами размещения предприятий цементной промышленности являются потребительский и сырьевой. Первый выражается в концентрации производства вблизи потенциальных потребителей — крупнейших городов и промышленных центров. Второй обусловлен наличием доступной и недорогой сырьевой базы.
На сегодняшний день в России насчитывается 58 цементных заводов с суммарной производственной мощностью порядка 106 млн. тонн цемента в год (Для получения детального анализа отрасли производств цемента, можно обратиться к сотрудикам — fira.ru). Производителей цемента на российском рынке условно можно разделить на три группы: российские холдинги, объединяющие несколько заводов; российские заводы, не входящие в состав промышленных групп; зарубежные холдинги, осуществляющие свою деятельность на территории России.
К крупнейшим российским холдингам относятся «Евроцемент груп», «Сибирский цемент»; ведущие зарубежные производители представлены на российском рынке компаниями LafargeHolcim, Heidelberg. Российские заводы, не входящие в состав промышленных групп, выпускают, как правило, небольшие объемы цементной продукции.
Крупнейшим производителем цемента в России является АО «Евроцемент Груп», которое представляет собой международный вертикально интегрированный промышленный холдинг по производству строительных материалов и объединяет 19 цементных заводов, 16 из которых расположены в России, остальные — в Украине и Узбекистане. Суммарная производственная мощность российских цементных заводов, входящих в состав АО «Евроцемент груп», составляет свыше 50 млн. тонн цемента в год. Также в состав холдинга входят заводы по производству бетона, ЖБИ, холдинг располагает богатейшей сырьевой базой — запасы нерудных материалов составляют более 5,5 млрд. тонн. По данным союза производителей цемента, на долю заводов АО «Евроцемент Груп» пришлось около 30% произведенного в 2016 году цемента.
Производство цемента, цемент с доставкой по Москве и Московской области
Без цемента, пожалуй, нельзя себе представить никакого строительства. Данный материал активно применяется и продолжает пользоваться успехом на протяжении вот уже более двухсот лет. Однако наиболее серьёзные научные открытия, ставшие основой для создания новейших видов цемента, а также улучшения свойств уже существующих, относятся только к последним десятилетиям.
Процесс изготовления цемента основывается на добыче специального цементного сырья, в дроблении, а также тщательном его измельчении. Далее готовится однородная сырьевая смесь нужного состава и обжигается до спекания. При размоле получаемого клинкера вместе с небольшой частью гипса и прочими добавками в мелкозернистый порошок получается цемент. Сырьевая смесь получается путём как совместного, так и раздельного размельчения двух или даже более компонентов и следующего за этим тщательного смешения, процессов гомогенизации, усреднения, а также коррекции до заданных составов в сухом состоянии, иногда в воде. Исходя из того, как готовится сырьевая смесь, можно выделить два главных способа изготовления такого вида цемента, как портландцемент, — мокрый и сухой.
Сухой способ. Мелкодроблёный сырьевой материал высушивается и тонко измельчается. Получаемая сырьевая мука в ходе коррекции и усреднения до заданных химических норм основательно обжигается в специальных вращающихся или же шахтных печах.
Мокрый способ. Твёрдый сырьевой материал — известняк и глинистые сланцы — в ходе дробления тонко измельчается в присутствии воды. Затем образуется сметанообразная масса, так называемый шлам. А вот мягкий сырьевой материал, такой как мел и глина, после процесса дробления подаётся в «болтушку», где, перемешиваясь с водой, формирует однородный шлам. Так, меловые и глиняные шламы в случае надобности тонко измельчаются на мельницах и отправляются в бассейны, где происходит коррекция и усреднение до заданных химических норм состава. После этого готовый шлам идёт на обжиг в печи. Стоит заметить, что отечественные цементные заводы отдают предпочтение мокрому способу производства цемента.
Какими же свойствами обладает цемент?
При добавлении цементного порошка в воду он формирует очень пластичное тесто, постепенно уплотняющееся, теряя свою пластичность. Данный процесс первоначального уплотнения принято называть схватыванием. Далее схватившееся цементное тесто уверенно увеличивает свою прочность и плотность. Цемент твердеет, образуя при этом надёжное «камневидное тело».
Как известно, при затвердевании цемент выделяет небольшое количество тепла. Выделение тепла цементом зависит от минерального состава цементного порошка.
Цемент также обладает морозостойкостью и невосприимчивостью к коррозии. Важно знать, что морозостойкость, а также коррозиеустойчивость цемента заметно уменьшается с увеличением пористости образующегося «камневидного тела».
Если вы хотите отстроить дом из кирпича или камня, то без цемента вам попросту не обойтись. Посетив наш он-лайн магазин, вы всегда сможете заказать цемент с доставкой по Москве и Московской области по самым доступным ценам.
Цементный Процесс производства
* Выберите страну / regionUnited StatesCanadaAfghanistanAlbaniaAlgeriaAmerican SamoaAndorraAngolaAnguillaAntarcticaAntigua и BarbudaArgentinaArmeniaArubaAustraliaAustriaAzerbaijanBahamasBahrainBangladeshBarbadosBelarusBelgiumBelizeBeninBermudaBhutanBoliviaBosnia и HerzegovinaBotswanaBouvet IslandBrazilBritish Индийский океан TerritoryBrunei DarussalamBulgariaBurkina FasoBurundiCambodiaCameroonCape VerdeCayman IslandsCentral африканских RepublicChadChileChinaChristmas IslandCocos (Килинг) IslandsColombiaComorosCongoCongo, Демократическая Республика ofCook IslandsCosta RicaCote D’IvoireCroatiaCubaCyprusCzech RepublicDenmarkDjiboutiDominicaDominican RepublicEast TimorEcuadorEgyptEl SalvadorEquatorial GuineaEritreaEstoniaEthiopiaFalkland острова (Мальвинские) Фарерские острова, Фиджи, Финляндия, Югославская Республика Македония, Франция, Французская Гвиана, Французская Полинезия, Южные французские территории, Габон, Гамбия, Грузия, Германия, Гана, Гибралтар, Греция, Гренландия, Гренада, Гуаделупа, Гуам GuatemalaGuineaGuinea-BissauGuyanaHaitiHeard и McDonald IslandsHoly Престол (Ватикан) HondurasHong KongHungaryIcelandIndiaIndonesiaIran (Исламская Республика) IraqIrelandIsraelItalyJamaicaJapanJordanKazakstanKenyaKiribatiKorea, Корейские Народно-Демократической RepKorea, Республика ofKuwaitKyrgyzstanLao Народный Демократической RepLatviaLebanonLesothoLiberiaLibyan Arab JamahiriyaLiechtensteinLithuaniaLuxembourgMacauMadagascarMalawiMalaysiaMaldivesMaliMaltaMarshall IslandsMartiniqueMauritaniaMauritiusMayotteMexicoMicronesia, Федеративные StatesMoldova, Республика ofMonacoMongoliaMontserratMoroccoMozambiqueMyanmarNamibiaNauruNepalNetherlandsNetherlands AntillesNew CaledoniaNew ZealandNicaraguaNigerNigeriaNiueNorfolk IslandNorthern Mariana IslandsNorwayOmanPakistanPalauPanamaPapua Нового GuineaParaguayPeruPhilippinesPitcairnPolandPortugalPuerto RicoQatarReunionRomaniaRussian FederationRwandaSaint HelenaSaint Китс и НевисСент-ЛюсияСент-Пьер и МикелонСамоаСан-МариноСао-Томе и ПринсипиСаудовская АравияСенег alSeychellesSierra LeoneSingaporeSlovakiaSloveniaSolomon IslandsSomaliaSouth AfricaSpainSri LankaSth Georgia & Sth Sandwich Институт социальных Винсент и GrenadinesSudanSurinameSvalbard и Ян MayenSwazilandSwedenSwitzerlandSyrian Arab RepublicTaiwan, провинция ChinaTajikistanTanzania, Объединенная Республика ofThailandTogoTokelauTongaTrinidad и TobagoTunisiaTurkeyTurkmenistanTurks и Кайкос IslandsTuvaluUgandaUkraineUnited Арабские EmiratesUnited KingdomUruguayUS Малые отдаленные IslandsUzbekistanVanuatuVenezuelaVietnamVirgin острова (Британские) Виргинские острова (U. S.) Острова Уоллис и Футуна Западная Сахара ЙеменЮгославия Замбия Зимбабве
Производство цемента — обзор
6.5 Использование дополнительных вяжущих материалов для сокращения выбросов CO
2 сокращение и секвестрация Производство цемента является одним из крупнейших источников выбросов CO 2 . SCM частично или полностью использовались в качестве замены цемента или мелкого заполнителя в строительстве для снижения спроса на цемент и соответствующих выбросов CO 2 (Al-Harthy et al., 2003; Бабу и Кумар, 2000; Бондарь и Коакли, 2014; Cheng et al., 2005; Цзя, 2012; Хан и Сиддик, 2011 г .; Кунал и др., 2012; Лимбахия и Робертс, 2004; Lothenbach et al., 2011; Маслехуддин и др., 2009; Наджим и др., 2014; Ночая и др., 2010; Сиддик, 2011; Сиддик и Беннасер, 2012; Toutanji et al., 2004). Некоторыми из установленных SCM являются летучая зола, микрокремнезем, доменный шлак, стальной шлак и т. Д. Пуццолановые материалы, такие как летучая зола, стальной шлак и цементная пыль (CKD), при использовании в качестве замены цемента, улучшают долговечность Срок действия бетона, так как пуццолановая реакция требует времени. Но прочность SCM в раннем возрасте вызывает беспокойство, так как уменьшение содержания цемента вызывает меньшую гидратацию и, как следствие, меньшее образование геля CSH (Lothenbach et al., 2011). Проблема низкой ранней прочности SCM может быть решена путем отверждения карбонизацией в раннем возрасте.
Помимо секвестрации CO 2 , карбонизирующее отверждение также действует как механизм активации для SCM (Monkman et al., 2018). Многие исследования пытались оценить влияние ACC на использование SCM (Monkman and Shao, 2006; Sharma and Goyal, 2018; Zhan et al., 2016; Zhang et al., 2016; Чжан и Шао, 2018). ACC не только увеличивает степень гидратации альтернативных вяжущих материалов, но также улучшает характеристики бетона в раннем возрасте. Монкман и Шао (2006) оценили карбонизацию доменного шлака, летучей золы, шлака электродуговой печи (ЭДП) и извести. Все четыре материала по-разному реагировали при отверждении карбонизацией в течение 2 часов. Летучая зола и известь показали самую высокую степень карбонизации, за ней следовали шлак из ДСП, тогда как измельченный гранулированный доменный шлак (GGBS) показал наименьшую реакционную способность по отношению к CO 2 . Кальцит был основным продуктом реакции из летучей золы, извести и шлака EAF, тогда как арагонит был получен карбонизацией GGBS. Sharma и Goyal (2018) изучали влияние ACC на цементные растворы, изготовленные с использованием CKD в качестве замены цемента. Было обнаружено, что ACC улучшает прочность цементных растворов в раннем возрасте на 20%, даже для растворов с более высоким содержанием CKD. В нескольких исследованиях была предпринята попытка оценить способность стальных вяжущих для шлака удерживать CO 2 (Bonenfant et al., 2008; He et al., 2013; Huijgen et al., 2005; Huijgen and Comans, 2006; Ukwattage et al., 2017). Присутствие компонента C 2 S в стальном шлаке делает его потенциально вяжущим материалом, который может действовать как сток углерода для связывания CO 2 (Johnson et al., 2003).
Zhang et al. (2016) в своем исследовании обнаружили, что бетон из летучей золы более реактивен к CO 2 по сравнению с бетоном OPC. С уменьшением содержания OPC образовалась пористая микроструктура из-за недостаточной реакции гидратации. Увеличенное расстояние между зернами цемента способствовало более высокой вероятности реакции с CO 2 и, следовательно, более высокой степени связывания CO 2 . Характеристики SCM, подвергнутых отверждению карбонизацией, в значительной степени зависят от тонкости материала и содержания воды после карбонизации. Более мелкий размер частиц SCM обеспечивает более высокую удельную площадь для эффективной реакции карбонизации. В связи с этим во многих исследованиях было замечено, что бетон, изготовленный с использованием SCM, имел лучшую реактивность по отношению к CO 2 , чем OPC (Monkman and Shao, 2006).Посткарбонизация содержания воды также играет доминирующую роль в определении производительности SCM. Посткарбонизация с достаточным содержанием воды необходима для полной гидратации и пуццолановой реакции SCM (Monkman and Shao, 2006).
цемент | Определение, состав, производство, история и факты
Цемент , в общем, клейкие вещества всех видов, но, в более узком смысле, связующие материалы, используемые в строительстве и гражданском строительстве. Цементы этого типа представляют собой мелкоизмельченные порошки, которые при смешивании с водой становятся твердой массой.Отверждение и затвердевание являются результатом гидратации, которая представляет собой химическую комбинацию цементных смесей с водой, которая дает субмикроскопические кристаллы или гелеобразный материал с большой площадью поверхности. Из-за их гидратирующих свойств строительные цементы, которые схватываются и затвердевают даже под водой, часто называют гидравлическими цементами. Самый важный из них — портландцемент.
Процесс производства цемента, от дробления и измельчения сырья до обжига измельченных и смешанных ингредиентов, до окончательного охлаждения и хранения готового продукта.
Encyclopædia Britannica, Inc. В этой статье рассматривается историческое развитие цемента, его производство из сырья, его состав и свойства, а также проверка этих свойств. Основное внимание уделяется портландцементу, но также уделяется внимание другим типам, таким как шлакосодержащий цемент и высокоглиноземистый цемент. Строительный цемент имеет общие химические составляющие и технологии обработки с керамическими изделиями, такими как кирпич и плитка, абразивные материалы и огнеупоры.Подробное описание одного из основных применений цемента см. В статье «Строительство зданий».
Применение цемента
Цемент может использоваться сам по себе (т.е. «в чистом виде» в качестве материала для затирки), но обычно используется в растворе и бетоне, в которых цемент смешивается с инертным материалом, известным как заполнитель. Строительный раствор представляет собой цемент, смешанный с песком или щебнем, размер которого должен быть менее примерно 5 мм (0,2 дюйма). Бетон представляет собой смесь цемента, песка или другого мелкого заполнителя и крупного заполнителя, который для большинства целей составляет от 19 до 25 мм (0.От 75 до 1 дюйма), но крупный заполнитель также может достигать 150 мм (6 дюймов), когда бетон помещается в большие массы, такие как дамбы. Растворы используются для связывания кирпичей, блоков и камня в стенах или для визуализации поверхностей. Бетон используется для самых разных строительных целей. Смеси грунта и портландцемента используются в качестве основы для дорог. Портландцемент также используется в производстве кирпича, плитки, черепицы, труб, балок, шпал и различных экструдированных изделий.Продукция собирается на заводах и поставляется готовой к установке.
Заливка бетона в фундамент дома.
Karlien du Plessis / Shutterstock.comПроизводство цемента чрезвычайно широко, так как бетон сегодня является наиболее широко используемым строительным материалом в мире.
Оформите подписку Britannica Premium и получите доступ к эксклюзивному контенту. Подпишись сейчасПроизводство цемента — Интерактивное покрытие
Пример операции — Lafarge Seattle
Пример производства цемента взят из Лафарж Сиэтл.На рисунках 1 и 2 ниже показано отношение завода Лафарж к центру Сиэтла и трехмерные изображения завода Лафарж соответственно. Всего у Lafarge 20 заводов в Северной Америке, 16 из которых производят портландцементы, а четыре — шлаковые.
Рисунок 1. Лафарж Сиэтл Антенна предоставлена Microsoft Virtual Earth. | Рис. 2. Лафарж Сиэтл Антенна 3D любезно предоставлено Microsoft Virtual Earth. |
Lafarge управляет цементным заводом в Сиэтле, штат Вашингтон, расположенном на участке площадью 25 акров, граничащем с водным путем Дувамиш.Завод впервые произвел цемент в 1967 году под названием Ideal Cement. Сейчас завод производит несколько видов цементов, которые затем используются в производстве бетона. Кроме того, завод в Сиэтле производит около 600 тысяч тонн различных цементов в год. Продукция продается в основном в штатах Вашингтон и Орегон. Однако меньшие количества продаются на Аляске, Калифорнии, Гавайях, Айдахо, Монтане и Юте. Кроме того, большая часть цемента, производимого в Lafarge Seattle, продается производителям готовых смесей.
Производство
Производство цемента на заводе Lafarge в Сиэтле осуществляется «мокрым способом». В результате сырье смешивается с 30-40% воды во время измельчения с образованием хорошо перемешанной суспензии. Этот мокрый процесс выгоден благодаря повышенной совместимости с влажным климатом и более равномерному смешиванию сырья перед обжигом, а также более низким выбросам пыли из печи. Однако недостатком мокрого процесса является то, что он требует больше энергии для производства клинкера. См. Также [http://www.epa.gov/epaoswer/other/ckd/rtc/chap-2.pdf] для получения дополнительной информации о мокром процессе согласно EPA.
Рисунок 3. На этой фотографии показана часть печи мокрого процесса длиной 540 футов в Лафарж Сиэтл. | Рис. 4. Несколько кусков клинкера с завода Лафарж Сиэтл. |
Кроме того, цементный завод в Сиэтле Лафарж работает в различных печах и температурах из-за различных химических реакций, протекающих в трех широких температурных зонах.
- Зона сушки
- Зона обжига
- Образование клинкера (зона обжига)
Ступеньки
- Шаг 1
- Все сырье (например, известняк, сланец и загрязненная почва) смешивается, измельчается вместе с водой с образованием суспензии.
- Известняк, сланец, сырье для почвы измельчается так, чтобы не менее 50% проходило через сито 45 мкм.
- Химический анализ суспензии проводится каждые два часа, чтобы убедиться, что состав суспензии соответствует требованиям.
- Все сырье (например, известняк, сланец и загрязненная почва) смешивается, измельчается вместе с водой с образованием суспензии.
- Шаг 2
- Суспензия со всеми сырьевыми ингредиентами подается непосредственно в печь, которая производит клинкер вместе с другими побочными продуктами, такими как цементная пыль (ЦП).
- Шаг 3
- Клинкер измельчают до частиц малого диаметра с добавлением гипса для контроля времени схватывания.
Более подробная картина производственного процесса представлена ниже, предоставленная Lafarge Seattle.
Рисунок 5. Квитанция на портландцемент. Предоставлено Робом Шогреном, Лафарж Сиэтл.Произведено цемента
ASTM C150 (AASHTO M85)
- Тип I-II: Спецификация типа II способствует устойчивости к умеренному воздействию сульфатов.
- Тип III: Бетон высокой ранней прочности.
- Тип II-V: Этот цемент время от времени производится для рынка Калифорнии — повышает устойчивость PCC к воздействию сульфатов.* Тип V обычно используется, когда требуется высокая сульфатостойкость.
ASTM C595 (AASHTO M240)
- Тип I (SM): портландцемент с модифицированным шлаком для использования в обычных бетонных конструкциях — цемент содержит до 25% по массе доменного шлака. Лидерство в области энергетического и экологического дизайна (LEED) дается за использование этого цемента. Для этого цемента компания Lafarge использует торговое название MaxCem.
ASTM C989 (AASHTO M320)
- Гранулированный доменный шлак (GGBFS), сорт 100: Lafarge продает эту продукцию под торговым названием «NewCem.«Этот продукт может использоваться в качестве добавки к портландцементу (аналогично тому, как летучая зола используется в качестве частичной замены портландцемента) или в качестве замены 1: 1 для типов I-II.
Цена составляет около 90% от Типа I-II (или на 10% меньше, чем Типа I-II).
Общее сырье
- Известняк с острова Тексада (Канада)
- Сланец из Британской Колумбии
- Гипс из Мексики
- Гранулированный доменный шлак из Японии (используется для производства цемента типа I (SM))
- Взрывной песок — в основном из Сиэтла.
Источник топлива Сырье
Материалы, сжигаемые в печи для выработки энергии. При производстве цемента в Lafarge Seattle в качестве сырья для печи используется 30% альтернативных материалов. Около ½ топлива, используемого в печи, производится из переработанных материалов.
- Топливо из шин
- Уголь
- Почвы, загрязненные углеводородами
- нет. 6 Мазут
- Отработанные растворители
- Краски для печати
- Остатки краски
- Чистящие жидкости
Это сырье не только обеспечивает более высокую энергию для сжигания, чем уголь, который является преобладающим источником топлива, но и при сжигании «остатки золы от TDF могут содержать более низкое содержание тяжелых металлов, чем некоторые угли, и приводить к более низким выбросам NOx по сравнению многим U. S. угли, особенно угли с высоким содержанием серы »(EPA). Кроме того, «альтернативный или, скорее, метод первичного удаления, заключающийся в размещении этого опасного сырья на свалках, исследования показали, что он оказывает большое негативное воздействие на окружающую среду, такое как вымывание токсинов в грунтовые воды, изменение значения pH и накопление тяжелых металлов» ( EPA). По общей оценке (2001 г.), предприятия Lafarge Seattle потребляют от 600 000 до 1 200 000 цельных шин в год (WSDOE).
Рисунок 6.Сваи для хранения загрязненного грунта. | Рис. 7. Сваи для хранения загрязненного грунта. |
Рисунок 8. Переработанное масло доставляется в Лафарж и сжигается в печи. | Рис. 9. Внутри печи во время запуска (показано топливо — природный газ). |
Контроль загрязнения на заводе Lafarge в Сиэтле
Рис. 10. Электростатические фильтры, удаляющие выбросы твердых частиц, образующихся в печи.
Как уже говорилось, цементный завод Lafarge Seattle Cement работает на различных альтернативных источниках топлива. Эти альтернативные источники топлива, такие как TDF и почвы, загрязненные углеводородами, являются основными загрязнителями. Поскольку завод расположен в Сиэтле, крупном мегаполисе, большое количество этих загрязнителей нуждается в переработке, повторном использовании или утилизации.
Другим примером контроля загрязнения завода Lafarge Seattle является его работа в условиях почти нулевого сброса воды.Это означает, что практически весь сток и сточные воды собираются, обрабатываются или используются иным образом. Ежегодно образуется около 25 миллионов галлонов ливневой воды.
На любом крупном промышленном предприятии важны вопросы контроля за загрязнением и безопасности, которые регулируются федеральным правительством, правительством штата и местными властями. Выбросы в атмосферу цементного завода Lafarge в Сиэтле регулируются агентством Puget Sound Clean Air Agency, и компания Lafarge должна соответствовать:
- Федеральный закон о безопасности и охране здоровья в шахтах
- Закон о чистом воздухе
- Закон о чистой воде
- Закон о сохранении и восстановлении ресурсов
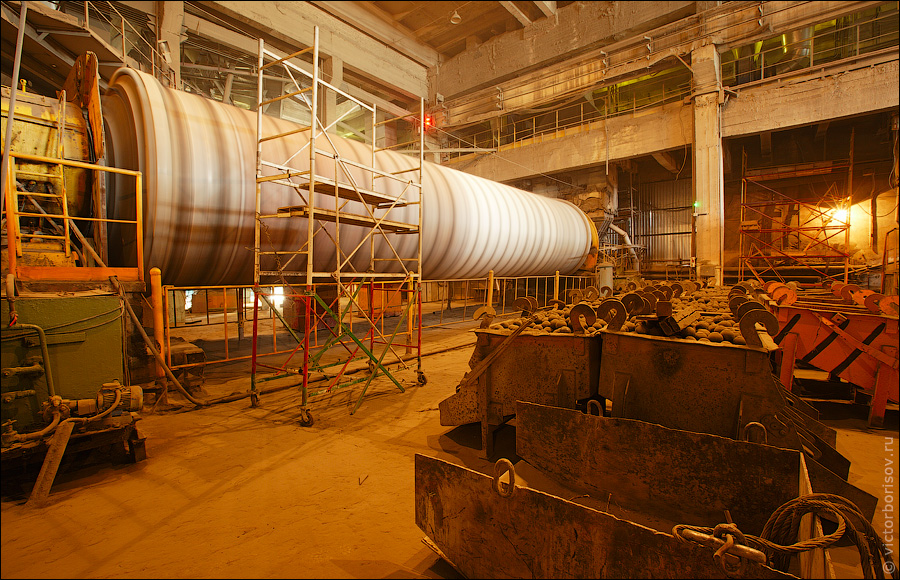
Выбросы в атмосферу от печи состоят в основном из следующих соединений:
Из-за времени горения материала (или времени выдержки) и высоких температур печи цементные печи не выделяют высоких уровней органических загрязнителей. Кроме того, выбросы NOx, которые типичны для любого процесса сжигания ископаемого топлива (электростанции, автомобили и печи) на заводе Lafarge в Сиэтле, составляют 95% NO и 5% NO2.Кроме того, хотя образуется значительное количество пыли, она в основном собирается с помощью электрофильтров.
В результате за счет создания инфраструктуры, развития наших сообществ, ремонта наших домов и вождения автомобилей мы производим огромное количество опасных отходов. Эти материалы загрязняют мир и производятся и используются с невообразимой скоростью. В результате существует огромная потребность найти способ утилизировать, повторно использовать или придумать новый способ утилизации всего этого опасного сырья. Цементные печи, такие как завод Lafarge Seattle, помогают утилизировать некоторые из этих опасных материалов способом, который EPA признает «лучшим использованием».
Источники
- Джо П. Махони. Профессор кафедры гражданской и экологической инженерии. Вашингтонский университет.
- Агентство по охране окружающей среды. Январь 2007 г. EPA. 24 марта 2007 ..
- WSDOE (2002), «Отчет о ломе шин SHB 2308», публикация № 02-07-029, Департамент экологии штата Вашингтон, декабрь 2002 г.
- Авторы статей
- Райлан Кнуттген
- Стив Мюнч
Как производят цемент и бетон
Цемент — важнейший ингредиент бетона. Это мелкий порошок, который действует как клей, скрепляющий бетон при смешивании с водой, песком и заполнителями.
Цемент производится путем нагревания точной смеси тонкоизмельченного известняка, глины и песка во вращающейся печи до температуры, достигающей 1450ºC.Это приводит к производству цементного клинкера, промежуточного продукта при производстве цемента. Цементный клинкер выходит из печи, охлаждается, а затем тонко измельчается для получения порошка, известного как цемент. На топливо, сжигаемое для обогрева печи, приходится около 40% выбросов при производстве цемента. Остальные 60% составляют «технологические выбросы», т.е. когда известняк перегрет, он высвобождает свои углеродные атомы и образует в печи CO 2 , которые практически невозможно восстановить. Канадская цементная и бетонная промышленность применяет ряд инновационных мер для дальнейшего сокращения углеродного следа.
Цемент — лишь небольшая часть рецептуры бетона, обычно составляя от 7% до 10% бетонной смеси. Другими основными компонентами бетона являются песок, гравий (мелкий и крупный заполнитель) и вода.
Химические вещества — так называемые добавки — иногда добавляют на стадии производства бетона для улавливания воздуха, удаления воды, изменения вязкости и изменения других эксплуатационных свойств. Производители улучшают процесс связывания цемента на стадии производства бетона с помощью дополнительных вяжущих материалов (SCM), которые поступают из промышленных стоков.
Основные ингредиенты цемента (известняк, песок и глина) и бетона (цемент, смешанный с песком, гравием и водой) являются одними из наиболее широко доступных сырьевых материалов на Земле.
Цементный порошок | Основные ингредиенты бетона: (цемент, смешанный с песком, гравием и водой) | Доля различных ингредиентов в типичной бетонной смеси |
Как цементная промышленность пытается уменьшить свои выбросы
Жарким июльским утром на испытательном полигоне за пределами Парижа группа ученых, инженеров и архитекторов в касках и защитных очках наблюдала через защитное стекло за тем, как машина формовала жидкую серую смесь в партии блоков размером с кирпич.Далее по линии оператор вилочного погрузчика осторожно загрузил блоки в камеру для выдержки, как буханки хлеба в пекарне.
То, что они стали свидетелями, было пробным запуском нового процесса производства бетона, разработанного Solidia Technologies, который, как надеется компания из Нью-Джерси, кардинально изменит способ производства этого строительного материала. Изменяя химический состав одного из основных ингредиентов бетона — цемента — и изменяя процесс его отверждения, компания заявляет, что может сделать бетон дешевле, чем традиционный процесс, и в то же время резко сократить выбросы углерода, связанные с производством цемента.
Цемент — одна из отраслей, наиболее сильно загрязняющих углеродные выбросы в мировой экономике. В 2015 году на долю цементной промышленности приходилось около 8% глобальных выбросов двуокиси углерода (CO2), если бы ее причисляли к отдельным странам, она была бы третьим по величине источником выбросов парниковых газов в мире после Китая и Соединенных Штатов. Прогнозируется, что в ближайшие десятилетия эта и без того огромная территория будет только расти по мере продолжения экономического развития и быстрой урбанизации в Юго-Восточной Азии и странах Африки к югу от Сахары. По данным Международного энергетического агентства и Инициативы устойчивого развития цемента, к 2050 году производство цемента может увеличиться на целых 23%.
Это представляет собой серьезную проблему для борьбы с изменением климата. Одно исследование 2018 года показало, что выбросы, связанные с цементом, должны сократиться как минимум на 16% к 2030 году, а после этого — намного больше, если страны достигнут цели Парижского климатического соглашения 2015 года, заключающейся в том, чтобы оставаться ниже двух градусов по Цельсию в этом столетии.
По мнению отраслевых экспертов, сокращения в таком масштабе потребуют повсеместного внедрения менее углеродоемких альтернатив цементу, которые сейчас разрабатываются в лабораториях по всему миру.Но на рынке, которым управляет горстка крупных производителей, которые опасаются вносить изменения в свои существующие бизнес-модели, при отсутствии сильной политики, стимулирующей более экологичные технологии, и в строительной отрасли, достаточно осторожно относящейся к новым строительным материалам, перспективы такого радикального изменения весьма далеки. от определенных.
Три тонны бетона на человека
Огромный углеродный след бетонной промышленности в основном связан с огромными масштабами использования материала. Этот искусственный камень, представляющий собой обычную комбинацию песка и гравия, склеенных цементом, настолько широко распространен, что является частью почти каждой структуры нашей современной застройки.
«Современное общество было бы невозможно без бетона», — говорит Роберт Курланд, автор книги Concrete Planet . Это самый распространенный синтетический материал из существующих, и, по данным Австралийской торговой группы Федерации цементной промышленности, если разделить весь бетон, который используется во всем мире каждый год, на каждого человека на планете ушло бы три тонны бетона, что делает его вторым по потреблению ресурсом в мире после воды.
Благодаря своему обилию бетон наносит огромный урон окружающей среде.Например, процесс изготовления портландцемента, наиболее распространенной формы, используемой для производства бетона, является одним из наиболее углеродоемких существующих производственных процессов; при производстве всего одной тонны получается более 1000 фунтов углекислого газа.
Процесс начинается с измельченного известняка, который смешивается с другим сырьем и затем подается в большую вращающуюся цилиндрическую печь, нагретую до температуры более 2600 градусов по Фаренгейту. Печь наклонена под небольшим углом, и материалы засыпаются в приподнятый конец.По мере того, как они движутся к реву пламени в нижнем конце печи, некоторые компоненты сгорают в виде газов, а остальные элементы объединяются, образуя серые шары, известные как клинкер. Комки материала размером с мрамор охлаждают, а затем измельчают в мелкий порошок, чтобы сформировать ключевой связующий элемент, который позволяет бетону затвердеть при отверждении водой.
[Исходное изображение: rpsonic / Blendswap] Этот процесс, который практически не изменился с тех пор, как был изобретен почти два столетия назад, производит выбросы углерода двумя способами.Во-первых, ископаемое топливо обычно сжигается для нагрева печи до высоких температур, необходимых для разложения материалов, с выделением углерода в процессе. Кроме того, сам процесс термического разложения приводит к выбросам, поскольку углерод, задержанный в известняке, соединяется с кислородом воздуха, образуя в качестве побочного продукта диоксид углерода.
Две трети связанных с цементом выбросов углерода возникают в результате этой реакции, поэтому производство цемента считается таким особенно сложным процессом для декарбонизации, — говорит Гаурав Сант, профессор гражданской и экологической инженерии Калифорнийского университета. , Лос-Анджелес (UCLA).По его словам, поскольку выбросы углекислого газа являются частью самого химического процесса, даже полный переход на источники энергии с низким или нулевым содержанием углерода для обогрева печей решит только часть проблемы.
Производители цемента уже предприняли шаги по сокращению выбросов. Благодаря повышению энергоэффективности и усовершенствованию бетонных смесей средняя интенсивность производства цемента по углекислому газу снизилась на 18% во всем мире за последние 20 лет. Некоторые компании также установили технологию, предотвращающую попадание выбросов углекислого газа в атмосферу, хотя такие системы могут улавливать только определенное количество и могут оказаться непригодными в масштабах, необходимых для оказания значительного воздействия.
В то время как лидеры отрасли недавно пообещали еще большее сокращение, Сант предупреждает, что существующие технологии могут обеспечить только часть экономии углекислого газа, необходимую для достижения целей в Париже. «Что действительно необходимо сделать отрасли, так это вложить деньги и усилия в производство новых или альтернативных типов цемента, которые требуют меньше или совсем не требуют клинкера», — говорит он. «Это единственный способ решить проблему выбросов CO2 в процессе производства цемента».
Достаточно ли технологий?
Компании пытаются разными методами уменьшить или исключить количество клинкера, необходимого для изготовления бетона.Компания BioMASON из Северной Каролины, например, использует бактерии, встречающиеся в природе, в качестве связующего вещества для изготовления бетонных кирпичей, в то время как CO2Concrete, дочерняя компания Калифорнийского университета в Лос-Анджелесе, разработала технологию, которая позволяет получать углекислый газ непосредственно из дымоходов электростанций для производства твердых минералов. карбонаты, которые затем можно использовать для замены традиционного портландцемента. Другие, такие как Banah в Соединенном Королевстве и Zeobond в Австралии, сосредоточены на использовании побочных продуктов других промышленных процессов для создания так называемых «геополимеров» для замены клинкера при производстве цемента.
Эксперты считают, что Solidia, компания из Нью-Джерси, которая летом прошла испытания во Франции, является одной из самых многообещающих. Его процесс, который был впервые разработан в 2008 году в Университете Рутгерса, включает в себя изменение химического состава цемента для значительного понижения температуры печи, необходимой для производства клинкера, а затем отверждение бетона, изготовленного из этого цемента, с использованием отработанного углекислого газа вместо воды.
«Сочетание этих технологий позволяет сократить углеродный след до 70% по сравнению с обычным бетоном на основе портландцемента — и при меньших затратах», — говорит Том Шулер, президент и главный исполнительный директор Solidia, получившей финансовую поддержку от известных венчурные компании Kleiner Perkins и Bright Capital, нефтяной гигант BP и швейцарская LafargeHolcim, крупнейший производитель цемента в мире.
Другая компания, работающая над альтернативными цементными растворами, — это CarbonCure со штаб-квартирой в Галифаксе, Новая Шотландия. Компания CarbonCure, детище гражданского инженера Роба Нивена, разработала систему, в которой сжиженный углекислый газ закачивается в влажный бетон по мере его перемешивания. По мере затвердевания бетона углерод из углекислого газа вступает в реакцию с бетоном, превращаясь в минерал, эффективно снижая потребность в цементе без ущерба для прочности или цены бетона.
«В любом конкретном строительстве или инфраструктурном проекте процесс минерализации CO2 снижает количество углерода, которое могут поглотить сотни, если не тысячи акров деревьев в течение года», — говорит Кристи Гэмбл, директор по устойчивому развитию CarbonCure.По ее словам, развертывание по всему миру может сократить выбросы двуокиси углерода примерно на 550 миллионов тонн в год, что эквивалентно снятию с дороги 150 миллионов автомобилей.
На данный момент технология CarbonCure, которая требует небольшой модернизации, состоящей из компьютерной системы, резервуара для хранения углекислого газа и трубы для закачки его в бетонную смесь, теперь установлена почти на 150 бетонных заводах по всей Северной Америке. Компания заявляет, что также расширяется в Юго-Восточную Азию и Европу.
Реальная демонстрация их продукта вырисовывается в Джорджии в строящемся многоэтажном коммерческом офисном здании в одном из самых модных районов Атланты.Строительство планируется завершить к концу года и станет первым крупномасштабным проектом, в котором во всей конструкции будет использован бетон, изготовленный с использованием CarbonCure. По словам Гэмбла, только этот проект предотвратит выброс более 750 тонн углекислого газа в атмосферу, что эквивалентно 800 акрам лесных угодий, улавливающих углекислый газ в течение года.
Хотя такие компании, как Solidia и CarbonCure, начинают продвигаться вперед, им еще предстоит пройти долгий путь, прежде чем они захватят хотя бы небольшую долю рынка.Шулер говорит, что серьезным препятствием является широко распространенный консерватизм в строительном секторе. «В индустрии принято смотреть, как это нужно, — говорит Шулер. Компания потратила около 100 миллионов долларов на исследования, разработки и испытания, подобные тем, которые проводились во Франции, чтобы убедить коммерческих клиентов.
Нежелание внедрять новые технологии понятно. «Когда дело доходит до обеспечения безопасности жизни в сооружениях, вы должны быть уверены, что то, что вы делаете, будет работать, — говорит Сант. Но он также утверждал, что сегодняшние правила техники безопасности не позволяют оценить новые процессы производства бетона, которые потребуются для значительного сокращения выбросов углерода в отрасли.
«Проблема в том, что мы слишком долго полагались на предписывающие кодексы и стандарты, которые предписывают нам конкретизировать конкретный путь, а не использовать критерии, основанные на производительности, которые будут стимулировать отраслевые инновации», — говорит он.
Еще одна важная проблема — это стоимость. «Хотя новые решения не всегда стоят дороже, чем обычные решения, в тех случаях, когда они это делают, готовность платить за дополнительные расходы ограничена», — говорит Джереми Грегори, исполнительный директор Concrete Sustainability Hub Массачусетского технологического института, исследовательской группы, специализирующейся на устойчивом бетоне. производство и использование.Исследование 2015 года показало, что, например, цементы на основе геополимеров могут стоить втрое дороже традиционных.
Политика компенсации этих более высоких затрат и поощрения инвестиций в экологически безопасные цементы также отсутствует, говорит Гэмбл, предполагая, что «технологический прогресс не может сам по себе снизить выбросы цемента». По ее словам, «необходимы такие меры, как ограничения на выбросы и штрафы, чтобы посылать рыночные сигналы и стимулировать широкое внедрение более экологичных технологий».
В конце концов, она признала, что низкоуглеродистый цемент еще очень далек от широкого распространения.Тем не менее, она остается уверенной: «Возможно, это займет 20, 30 лет, может быть, больше. Но мы начинаем видеть первые проблески этого пути ».
Принимая во внимание огромные масштабы углеродного следа, только цемент может сделать или сломать усилия по замедлению глобального потепления. Для Грегори единственный путь вперед — это продолжать подталкивать всю отрасль к ускорению ее усилий.
«Откладывать или избегать этого, — говорит он, — на самом деле не вариант».
Марчелло Росси — внештатный научный и экологический журналист из Милана, Италия.Его работы были опубликованы Al Jazeera, Smithsonian, Reuters, Wired, и Outside среди других изданий.
Эта статья изначально была опубликована на сайте Undark. Прочитать оригинальную статью.
Производство цемента: Gasmet.com
Цемент — основной ингредиент бетона, который является самым распространенным строительным материалом в мире. Цементная промышленность является одним из крупнейших производителей выбросов CO2, в основном из-за огромных производственных мощностей и процесса обжига, который является важной частью производства цемента.Производители цемента должны постоянно контролировать эти выбросы в соответствии с местными правилами выбросов. Прочтите о наших решениях для цементной промышленности!
Сжигание отходов в цементных печах
Цементная промышленность активно стремится увеличить использование альтернативных видов топлива для производства цемента. Как для уменьшения энергетической зависимости от традиционных ископаемых видов топлива, так и для смягчения негативного воздействия на окружающую среду.
Одна из этих альтернатив — использование отходов в энергию.Многие цементные заводы вырабатывают энергию за счет сжигания отходов. Опасные отходы можно сжигать на определенных предприятиях по переработке отходов в энергию, а также на предприятиях, имеющих разрешение на совместное сжигание отходов.
Обратной стороной является то, что при сжигании отходов в цементных печах в воздух выделяются токсичные выбросы, содержащие ртуть, свинец, кадмий, таллий и другие тяжелые металлы.
Мониторинг выбросов цементных заводов
Цементные заводы в целом придерживаются собственных стандартов мониторинга выбросов.На цементных заводах дымовой газ обычно включает диоксид углерода (CO2), оксиды азота (NOx), диоксид серы (SO2), ртуть и пыль. Выбросы SO2 в основном связаны с сырьем, тогда как более половины выбросов CO2 приходится на процесс обжига известняка, а остальная часть связана с используемым топливом и эффективностью процесса сгорания.
Если цементный завод действует как завод по совместному сжиганию и сжигает отходы, он подлежит строгому регулированию выбросов. Все установки по сжиганию отходов должны соответствовать как минимум строгим ограничениям выбросов, стандартам мониторинга, приема и обработки отходов, установленным Директивой по сжиганию отходов (2000/76 / EC), которая была преобразована в Директиву о промышленных выбросах (2010/75 / ЕВРОПА).
Чтобы узнать больше о мониторинге выбросов, загрузите наше Руководство по мониторингу выбросов.
Директива по сжиганию отходов требует от установок совместного сжигания непрерывного измерения, например, соляной кислоты (HCl), фтористого водорода (HF) и ртути (Hg). Измерение общего органического углерода (TOC) также является обязательным.
Наше решение: системы мониторинга для сложных измерений
Обе наши системы непрерывного мониторинга выбросов (CEMS) являются сертифицированными системами, разработанными для выполнения сложных измерений мониторинга выбросов.
- Система непрерывного мониторинга выбросов CEMS II e предлагает сертифицированное решение TÜV и MCERTS (QAL1) для широкого спектра требовательных приложений мониторинга выбросов. В системе CEMS II e используется технология ИК-Фурье-спектроскопии с преобразованием Фурье. CEMS II e также может быть оснащен анализатором кислорода ZrO2, который предназначен для непрерывного измерения содержания кислорода во влажных или сухих дымовых газах. Gasmet CEMS II e обычно используется для одновременного измерения следующих 16 газов: h3O, CO2, CO, N2O, NO, NO2, SO2, HCl, HF, Nh4, Ch5, C2H6, C3H8, C2h5, C6h24 и Ch3O.
- Системы непрерывного мониторинга ртути CMM AutoQAL и CMM имеют самый низкий сертифицированный диапазон в мире (0-5 мкг / м3). CMM AutoQAL имеет автоматический и интегрированный инструмент проверки QAL3. Системы идеально подходят для непрерывного мониторинга ртути в потоках горячих, влажных и агрессивных газов. В системах используется технология атомной флуоресценции холодного пара (CVAF).
У нас также есть система отбора проб диоксинов и фуранов:
- Система контроля диоксинов GT90 Dioxin + Сертифицированный прибор MCERTS, предназначенный для длительного отбора проб выбросов диоксинов и фуранов в соответствии с европейскими стандартами EN1948-1 и EN15267.Система представляет собой передовую технологию отбора проб диоксинов и выполняет все требования стандарта измерения диоксинов.
Почему выбирают Gasmet в качестве партнера по мониторингу выбросов?
Gasmet — идеальный партнер для цементной промышленности. Вот 5 основных причин, почему вы должны выбрать нас своим партнером:
- Снизьте риски с помощью оборудования, отвечающего всем нормативным требованиям
- Экономьте деньги с минимальными затратами на обслуживание, эксплуатацию и калибровку
- Увеличьте срок службы инвестиций с большим ожидаемым сроком службы
- Надежность ваших инвестиций в будущем.С решениями Gasmet, если возникнут дополнительные требования, новые соединения могут быть добавлены в измерительную установку без дорогостоящих изменений оборудования.
- Gasmet имеет репутацию поставщика аналитических услуг, предоставления качественных продуктов и услуг
Загрузите бесплатную копию нашего руководства по мониторингу выбросов ниже и узнайте больше о лучших доступных технологиях и решениях для эффективного мониторинга выбросов и отбора проб:
РУКОВОДСТВО ПО МОНИТОРИНГУ ВЫБРОСОВ
Прочитав руководство, вы будете знакомы с:
- Мониторинг промышленных выбросов и подходящие технологии
- Гарантия качества
- WI BAT Выводы для установок для сжигания и совместного сжигания отходов
- LCP BAT Выводы для крупных установок сжигания
- Решения Gasmet для мониторинга выбросов
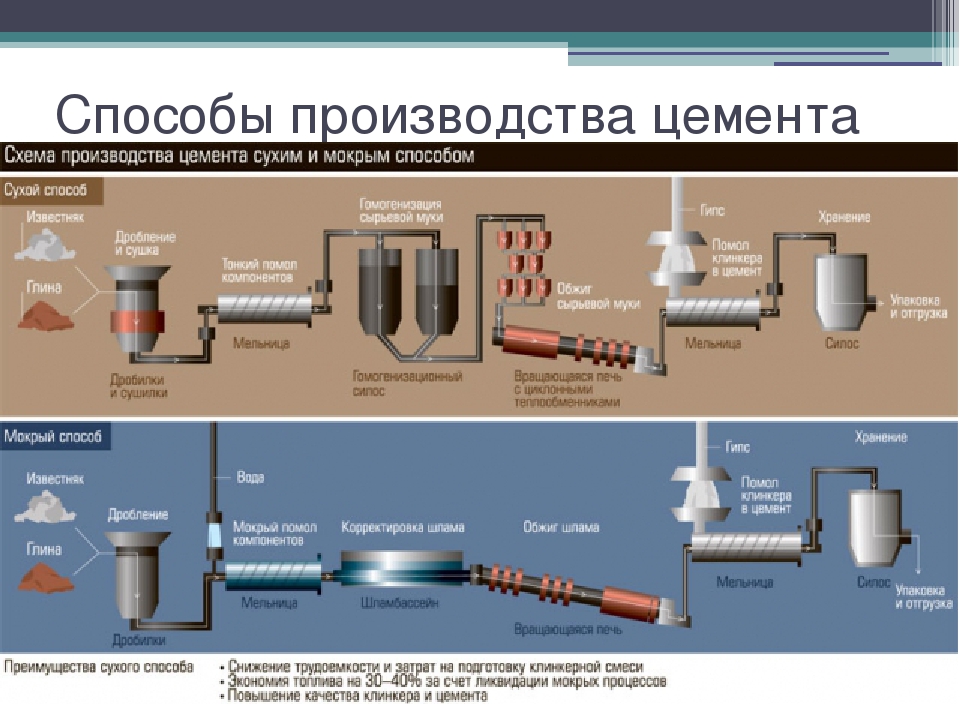